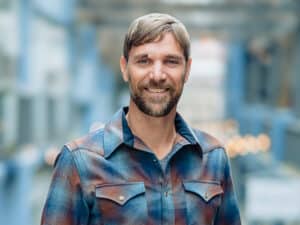
Q&A: Craig Gundry, president of Cormorant Maritime Projects
Written by Heather Ervin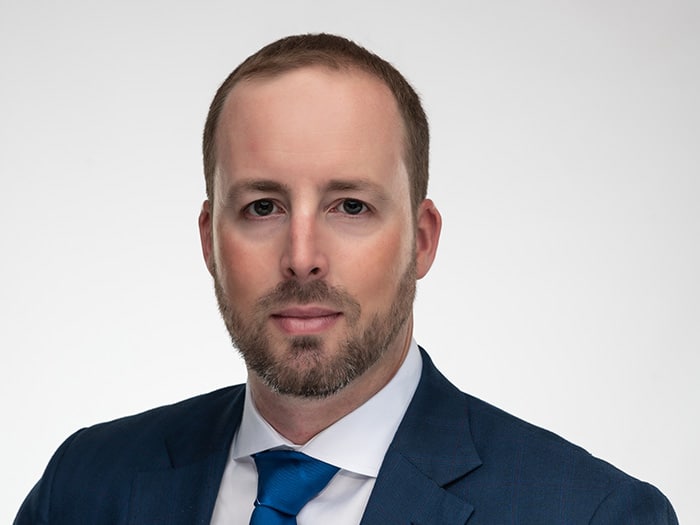
Craig Gundry
Craig Gundry explains his philosophy behind helping clients go green.
Marine Log (ML): For the past decade, you’ve been engaged in assisting shipowners, operators, shipyards and others in implementing green technologies into their business practices or operations. Can you tell us more about your process in doing this and what types of green technologies Cormorant Maritime Projects assists with?
Craig Gundry (CG): My core philosophy these days, especially in a turnkey project, is clients want a limited number of points of contact. They want to be able to talk to one person, whether that’s a shipyard or a contractor on behalf of the shipyard. Achieving a single point of contact is good because you reduce problems or mistakes or lost time that may happen due to missed communications.
So, wrapping in a client with the project team and key suppliers and OEMs. One person running the show as much as possible, so to speak. The part that is innovative for us, is addressing the gap between design and execution. Sometimes you can get situations that arise where a designer designs one way, and the installation manager comes back and says, “you can’t do it this way.”
We’ve learned to identify and train people to keep a consistency between design management and install management. Usually design managers aren’t the type to be in a drydock for 30-60 days or be on a ship for an in-service installation for a long time. They aren’t running a crew. And vice versa, most installation managers can’t sit in front of a desk and design. I’ve learned to identify and train individuals to do just that. When we engage in projects, whether it’s just design or just installation, ideally both, that management is consistent. Then, you have design managers that understand the practicality of installations and design in that way to save time and money while limiting material loss. Similarly, the install managers understand the thought process behind the design. They can then adjust on site and adjust in real time for the project.
Creating ownership of the entire scope to a single manager who can understand every element behind design and install is key. Very often our install managers catch design mistakes before we even begin the install. It’s not that it’s bad design, but they don’t know the realities of doing an install on a ship.
Over the beginning years when I had this idea, there was a lot of trial and error. It’s a mix of finding talent and personality and doing it in a way that introduces a new concept in a way that isn’t overwhelming. It works in one direction, to take a designer and make them an install manager. I’ve tried the other way, to make an install manager a designer, but we’ve found it’s a lot easier to have the design skill set to begin with. Some of these programs are not easy to learn and it take years to develop skills. All the programs have nuances. The designer then must get used to the physical aspect and learn how to communicate with people, and lead in a proper way.
ML: Last month, you spoke on green retrofits at Marine Log’s Ship Repair USA conference in New Orleans. What was the crux of your presentation and what were the top takeaways?
CG: Something that was very important to me during this presentation was to provide insight on different types of green equipment solutions that some in the audience may not have been aware of, which I will get into later.
There is a lot of fatigue in the industry with the barrage of new regulations and the equipment associated with. I believe I was successful in letting the audience know that there are organizations out there like Cormorant Maritime Projects, who can help guide and/or execute a smooth process. This will not only allow them to increase their environmental compliance but save valuable time and internal resources so that focus does not get taken away from operational safety or efficiency.
ML: Where are you seeing the most activity in green technologies from builders and operators?
CG: A lot of focus is on the ships themselves, but I want to focus on some technology available to shipyards. It’s important for shipyards to be greener too, and it helps save their costs. Making a shipyard greener translates to more available time which leads to more opportunities to implement green technologies.
This doesn’t have to be so painful. We know the organizations have fatigue; think about all the red tape we’ve gone through in the last 10 years. Scrubbers were tough, but ballasts became overwhelming, and people are realizing that maybe their decision wasn’t the best fit for their ship. A sort of analysis paralysis can arise. The biggest mistake is not taking enough lessons learned from the cruise industry. They have organizations and consultants that can give some important lessons. It’s always important to talk to environmental consultants from the cruise industry.
Whenever it comes down the pipe for the commercial shipping industry, it probably hit the cruise industry first. Cruises are going into very public areas that were regulated strongly before the commercial industry was. There are lessons to be learned.
ML: Are there any prevalent challenges you’re hearing about from customers in obtaining/maintaining greener vessels or tech? Are there any solutions to meeting those challenges?
CG: The biggest challenge is always time, many organizations do not give their teams enough time to properly plan these installations. A lot of that is because these vessels are chartered, if they’re not on the water, they’re not making money. Also, sometimes these charters don’t have a lot of control over the schedule. Or maybe they schedule a drydock period for improvements, and those classic maintenance sessions and valve replacements do help the overall efficiency of the vessel, of course.
The time factor is the biggest challenge. You see companies that must do major projects, but they’re not given the ability to plan. The shipyards, ship owners and contractors need to give more time to properly plan. It saves cost, it saves time, and it makes projects safer. No rushing. I’d be a billionaire if I collected all the money I’ve seen clients waste by not planning time properly.
Even though the technology has been around, there is still a fundamental misunderstanding with 3D scanning. It’s utilized, but just because you get a 3D scanning report doesn’t mean the shipyard has enough information to effectively quote a job. Just like any technology: bad info in, bad info out. The right person running the scanner will get a different result than someone who isn’t trained in 3D scanning and doesn’t understand installation. Where that camera is positioned can mean everything for planning and executing the job. If the scan is done in the wrong way, the proper materials won’t be ordered for the install. There’s more upfront cost to do it correctly, but a proper 3D scan will save money in the end.
ML: What do you see as being the top green technologies being adopted by vessel owners and operators over the next five years? (Consider all vessel sizes from tugs/towboats to ferries and cargo ships).
CG: In terms of new technology, with this test period of the CII (Carbon Intensity Indicator) rating, organizations need to be highly focused on what they can do to improve that rating. They’re looking to technologies that can help them improve this rating. One of the technologies is from a company called Frese. Frese FUELSAVE has found a way to dynamically control and optimize the freshwater cooling systems. This results in a drastic reduction of pump usage with leads to a drastic 3-9 percent fuel savings. Unlike some of the past technologies, it’s more aligned with the ballast with a relatively easy installation, you can implement it in the shipyard and in service with a minimal crew. You get a payback from it, and not just from avoiding a fine, there is ROI from the fuel savings, and it increases your CII ratings.
You’re seeing other types of equipment, propulsion systems that increase efficiency. The air bubble systems that a couple companies have come up with. Again, the cruise industry was one of the first adopters of this one. After this test period, a lot of those are going to hold when they start regulating it.