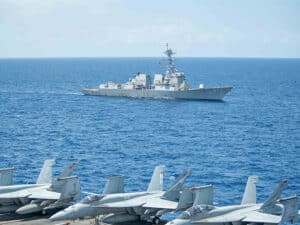
Steel-aluminum foam sandwich weld holds promise for shipbuilding weight savings
Written by Nick BlenkeyIn a promising development for lightweight shipbuilding constructions, Germany’s Laser Zentrum Hannover e.V. (LZH) and its partners in a joint project have laser welded a demonstrator for marine gear unit foundations made of steel and aluminum foam sandwich material.
Large scale metal-foam sandwich materials are especially interesting for highly stressed ship structures such as foundations for machines, or for rudder structures, since weight reductions of up to 20 percent are possible.
Metal foams are highly porous, lightweight materials which, due to their cellular structure, can absorb energy in the form of vibrations and knocks, or noise. They are also heat resistant and provide insulation against electromagnetic waves. Metal foams, embedded in sandwich constructions with aluminum or steel sheets, have a much higher bending stiffness than solid sheets, and due to their lower weight, are especially suitable for lightweight construction, or for highly stressed parts.
However, steel-aluminum lightweight structures are difficult to weld, due to inhomogeneity of the foam core, high stiffness, and the material thicknesses. One problem is, for example, the thermal effects of foaming the aluminum core in mixed sandwich materials, which can distort the material. Welding can also lead to intermetallic phases, causing cracks in the welding seam.
Scientists in the group “Joining and Cutting of Metals” have developed a process for laser welding large scale, metal-foam sandwich materials, in which intermetallic phases do not occur. Their investigations are being made within the framework of the joint project MESCHLAS.
This process was recently tested on a gear unit foundation at Blohm + Voss Naval GmbH in Emden. It uses a transportable axis system and a mobile diode laser, which were provided by the companies Scientific and Efficient Technologies Ltd. (SET) und LASER on demand GmbH (LoD).
As the first step, mechanical preparation of the panel edges is necessary. The aluminum foam which adheres to the steel top sheets (S235JR) is removed, thus preventing intermetallic phases. Then the components must be exactly positioned, forming a zero gap. Due to the size of the panels, this step is rather challenging. Following this, the sandwich panels are fixed using conventional spot welding. Laser welding of the butt welds and fillet welds then takes place, using a diode laser with a wavelength between 900 and 1030 nm and an output of 5 kW. Tests show that a gap of 0.6 mm can be bridged, and continuous weld seams are possible. Depending on the material thickness (up to 5 mm), speeds of 0.2 to 1.5 m/min. were possible.
The project MESCHLAS aims at providing lightweight construction using sandwich technology, including the processing necessary to accomplish this. The LZH is working together with the Fraunhofer Institute for Machine Tools and Forming Technology (IWU) and Blohm + Voss Naval GmbH and Precitec Optronik GmbH to accomplish this goal. The project is financially supported by the German Federal Ministry of Economics and Technology April 23, 2012
Leave a Reply
You must be logged in to post a comment.