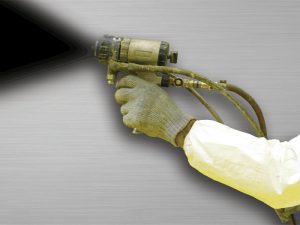
Advantages of fast-curing polyurethanes for BWTs
The use of ballast water is critical to the safe operation of ships, but also poses challenges due to the need to maintain the structural integrity of ballast water tanks (BWTs) despite highly corrosive conditions. Appropriate protective coatings act as barriers to corrosion and if applied carefully to properly prepared surfaces can significantly extend the life of BWTs. Two-coat epoxy systems are commonly used today, but rapid curing polyurethanes have performance properties that make them attractive as alternative coating solutions, including tunable properties that allow the formulation of flexible yet hard coatings that resist cracking, excellent adherence to steel, high resistance to corrosion, chemicals, and abrasion and fast return to service.
Ballast tanks located at the bottom, around cargo holds, and near the bow and stern of ships provide a mechanism for maintaining balance. Water is filled or released from the tanks to stabilize and trim ships during sailing and to keep them evenly afloat during the loading and unloading of cargo. Ballast water tanks (BWTs) are typically dedicated for this purpose. Ballast tanks are also used to adjust the buoyancy of submarines and stabilize offshore oil platforms and floating wind turbines.
In marine vessels (tankers, bulk carriers, etc.), ballast tanks typically comprise the largest surface area of steel. Corrosion of these tanks can therefore significantly reduce ship safety and operational life. In the past, ships suffering from severely corroded ballast tanks have experienced total failure of their hull shell plates. There is general agreement in the industry that prevention of corrosion in BWTs is the second most important factor after design integrity in determining the operating life of a ship.
Corrosion prevention in BWTs is not a simple matter, however. The water in ballast tanks can have a high salt content, vary in the type and concentration of other ions and have a wide range for pH and may also contain corrosive chemicals. Empty ballast tanks, on the other hand, are exposed to corrosive atmospheres that cycle with the temperature of the tank. Tanks, when partially full, are also subject to continuous movement of the water.
In fact, different parts of ballast tanks corrode via different mechanisms and at different rates, and empty tanks behave differently than tanks that are often filled with water. For Example, some parts of tanks are exposed to cyclic heating and cooling and/or local heating from warm, adjacent cargo tanks and engine rooms. Additionally, the exterior of the BWT is exposed to the weather above the water line and the differing temperatures of the sea below the water line. Therefore the same tank can experience uneven thermal cycling due to the extreme differences in its exterior exposure. Because the upper portion of the tank is exposed to extreme thermal cycling and repetitive wet and dry service, anodic oxidation is the main source of corrosion in this part of the tank. On the other hand, the bottom area of a tank is constantly exposed to the sea and therefore is maintained at a lower temperature and is subject to cathodic blistering. Any microbes in sediment on the bottom can also cause microbial corrosion.
Many other factors such as bacterial biofilm, mechanical vibration and effectiveness of sacrificial or impressed current anodic protection play a moderate role in determining the rate of corrosion in ballast water tanks.
To prevent corrosion in BWTs, high-performance protective coatings are applied during construction of the ship. Typically two thin layers of a suitable coating with a total dry-film thickness of approximately 300-320 microns are sufficient to provide an effective barrier against corrosion. Such coatings must meet many regulatory requirements related to their environmental and performance characteristics.
Current Coating Technologies
Preferred coatings not only provide a long lifetime of protection (15 years or more is required by the International Maritime Organization (IMO) Performance Standard for Protective Coatings (PSPC)¾see below), they must be easy to apply under the varying conditions found at different shipyards around the world and easy to maintain. Coatings that provide greater coverage for less material usage and are more tolerant of poorer surfaces are also in demand. A low volatile organic compound (VOC) content (< 250 g/l) is also necessary.
The majority of BWT coatings applied today are epoxy-based systems. Most are solvent-based, high solids formulations, although some European shipbuilders use solvent-free coatings to meet the requirements of the EU Solvent Emissions Directive (SED). The latter 100% solids epoxy systems have good performance properties, but tend to suffer from poor wetting properties and slower curing rates at low temperatures. Good wettability is necessary to ensure that pitted areas are filled rather than bridged, and thus do not leave a void below the paint film that can act as a starting point for corrosion.
Rapid curing is a very desirable property for BWT coatings because it translates into shorter construction times for new builds and reduced time in dry-dock for recoating and repair. The US Navy has developed a series of 100% solids coatings based on amino polyols prepared from either alkanol amines and polyfunctional epoxy materials or polyamines and monofunctional epoxides that are applied using plural component equipment, which eliminates the poor flow concerns. They are referred to as “single-coat” systems because the necessary two coats can be applied in one day, rather than in two. The technology for a light-to-medium-duty coating based on a medium-viscosity resin has been licensed and is commercially available. In a study at a commercial shipyard in Asia, the rapid curing coating, which meets the IMO PSPC requirements, was shown to provide a nearly 40% increase in painting productivity and a 20% overall cost savings.
Advantages of Polyurethanes
Certain polyurethane (PU) coatings have also been shown to have significant potential as highly protective barrier coatings for ballast water tanks. Specifically, 100% solids rigid and structural polyurethane coatings are promising because they cure very rapidly, even at cold temperatures, and have superior resistance properties.
One of the major issues with epoxy coatings is their inability to build desired dry film thickness at sharp edges, corners, weld seams and other defect sites. Coating failures generally occur first in these areas, usually do to crack formation. Unfortunately, there are many of these sites present in BTWs. While the PSPC does require that sharp edges be addressed prior to coating, this problem remains a concern in the industry. Advances in epoxy coating technology have helped, but further improvements are still desired.
Polyurethanes have the key advantage of property tunability. Careful selection of the polyisocyanate and polyol segments can provide coatings with very specific properties. For ballast water tank applications, a hard coating is needed that retains some flexibility to allow for high film builds at edges, seams and defect sites. This unique mix of properties, which cannot be achieved with epoxy systems, is possible with polyurethane coatings. Careful preparation of the PU resin and development of the formulated PU coating can provide coatings with desirable edge retention properties.
With the appropriate choice of starting materials, it is also possible to formulate polyurethane systems with curing times that allow for the application of perfectly smooth, high-build coatings. These barrier coatings are applied with no defects in one continuous application and serve as abrasion- and impact-resistant protective barriers to corrosion. Furthermore, because they contain no solvent, 100% solids polyurethane coatings are “green” coatings that meet stringent environmental regulations, and most are odor-free, providing a better shipyard application environment than high-solids epoxies.
Surface adhesion, as for all coating applications, is crucial for BWT coatings and has a significant impact on coating performance. More forgiving coatings that have strong adhesion to the different types of steel used in shipbuilding and the different types of surface conditions that can be present are therefore highly desired for the protection of ballast water tanks. Polyurethanes meet this requirement and generally surpass the adhesion properties of many epoxy systems.
The inherent barrier properties of polyurethane coatings are also excellent. PUs show high resistance to corrosion and chemicals. In addition, they provide superior abrasion and impact resistance, which is not true for epoxies systems. Finally, the very rapid curing of polyurethanes over a wide temperature range makes them suitable for application to water ballast tanks regardless of where they are built or dry-docked and ensures reduced coating times during newbuilding and fast return to service for repair/maintenance operations.
Performance Requirements: PSPC and Invasive Species Control
The IMO PSPC became effective in 2008 and provides specific requirements for the types of corrosion control coatings that can be used on ballast water tanks, as well as appropriate application, inspection and maintenance procedures. Extensive documentation is also specified in the standard. The intent is to have all BWTs coated with systems that will provide a 215-year service life.
Coating systems must be pre-qualified/certified prior to use in ballast water tanks. Certification can be obtained from an approved, independent testing laboratory, through demonstrated performance in the field for a minimum of five years, or by presenting results from previous, relevant tests. Coating application during the newbuilding process must be extensively monitored, and inspections performed at numerous phases. For example, testing of the surface profile and water-soluble salt content are required before application of the first coat, and a thorough inspection of the first coat is necessary before the second coat can be applied. These requirements can slow down the coating process and increase the cost. Consequently, rapid-cure coatings that allow the application of two coatings in a single day are attracting significant attention.
Recent regulations attempting to prevent the spread of invasive species through ballast water must also be considered when installing BWT coatings. There have been several cases of the transport of invasive species around the world, some of which have had severe ecological and/or economic impacts. However, many of the current chemical technologies available for destroying harmful marine organisms in ballast water are based on oxidizing agents (e.g., chlorine dioxide, ozone) that are damaging to the coatings and can lead to corrosion problems. Mechanical systems based on filtration/separation and those that use ultraviolet radiation tend to be less problematic. Therefore, it is crucial that testing of corrosion control coatings for ballast water tanks be performed under maximum treatment conditions for a given application.
A Word about Surface Preparation, Quality Assurance and Maintenance
As with all coatings, surface preparation is critical to the performance of BWT coatings. In fact, lack of proper surface preparation is one of the main causes for coating failures in ballast water tanks. It is imperative that appropriate surface preparation standards (SSPC/NACE/ASTM) be met. Attention should be paid to both surface profile and soluble salt content.
Application conditions must also be considered, as temperature and relative humidity during application can affect the ultimate performance of many coating systems, particularly epoxies. While most large, modern shipyards have enclosed areas for conducting abrasive sand blasting and painting (with temperature and humidity control), some smaller facilities do not. Work is therefore performed under ambient conditions using power tools, which can result in poor surfaces for coating. Polyurethanes offer advantages in these situations, as they have superior adhesion to poor surfaces and temperature and humidity do not impact their curing or ultimate performance properties.
PUs are Good for Potable Water Tanks
The properties of polyurethanes that make them ideal as corrosion protection coatings for ballast water tanks also make them well-suited for use as protective systems for marine potable water tanks. Many polyurethanes meet the requirements of the ANSI (American National Standards Institute)/NSF (National Sanitation Foundation) Standard 61 – Drinking Water System Components, which establishes stringent requirements for the control of leachables and extractables from materials that come in contact with either potable water or products that support the production of potable water.
Conclusion
Preventing corrosion in ballast water tanks is crucial for ensuring the safety and longevity of on marine vessels. While epoxy systems are currently the most common coatings used in this application today, properly formulated, fast-curing polyurethanes are attractive alternatives with significant potential to reduce lengthy coating processes, increase shipyard productivity and thus reduce costs.