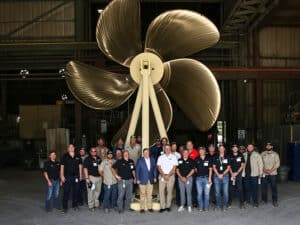
Mapping a path to 3D printing marine and offshore parts
Written by Nick Blenkey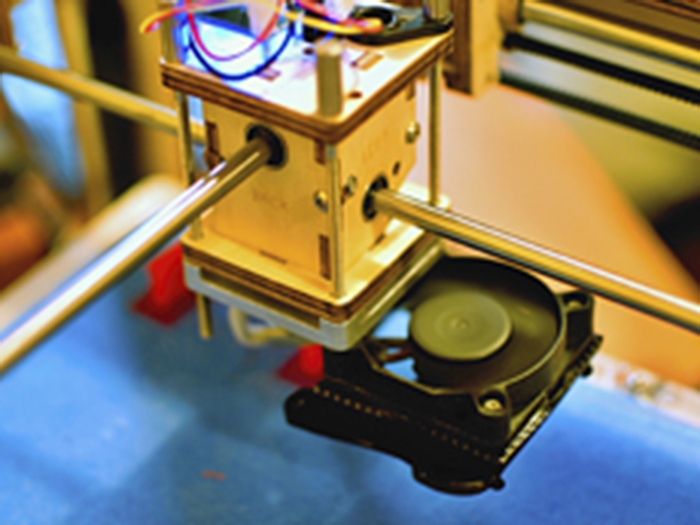
MARCH 30, 2017 — Additive Manufacturing (AM) is emerging as a preferred term for what most us call 3D printing. Be that as it may, using the deposition of material to build up a part, rather than machining material away — could soon be used to rapidly make large parts for the marine and offshore industry.
LR (Lloyd’s Register) recently held a qualification workshop for Keppel Marine and Offshore and the Singapore Centre for 3D Printing at Nanyang Technological University to map out a safe, sustainable and quality-driven approach to additive manufacturing (AM) of metallic parts intended for rugged environments, such as shipping and offshore oil and gas production.
Qualification is a critical step towards certification and adoption of industrial products made by AM. The workshop focused on a broad range of knowledge and skills required to demonstrate competency in AM and to meet industry quality and safety regulations and standards.
“The workshop covered the key risk areas of AM that we had examined before starting our AM program,” said Mr. Tan Kim Pong, Program Manager at Keppel Offshore and Marine Technology Centre. “The testing and inspection requirements were comprehensive and well thought out, which reinforced our confidence in this newly established manufacturing technology, which is fairly new to the industry. Moving forward, this workshop will serve as a platform in the development of our AM workflow, as well as understanding key engagement points with a third-party inspection organization such as LR.”
The three-day workshop covered topics that included:
- Design – designs can be optimised for AM but both designer and designs must still meet stringent assessment against various codes and standards.
- Materials – feedstock (powder and wire) are considered some of the riskiest points for quality in the AM supply chain, and subsequently require the most stringent controls for procurement, handling, testing and mixing.
- Manufacturing – the AM process is subject to numerous system and human variables found within the setup, printing and control of the AM and auxiliary systems.
- Post-processing – part removal, thermal processing and final finishing all require planning and control in order to meet the technical delivery condition requirements.
- Inspection and testing – testing and inspection is mandatory in most cases to ensure produced parts are suitable for putting into service and meet design, material specification and legal requirements.
“These workshops represent a collaborative, knowledge-sharing approach to new technology adoption,” said David Hardacre, LR’s AM Technical Lead and workshop leader. “Similar workshops are offered to clients globally to support them with cradle-to-grave considerations of AM – including business case justification, facility requirements, risk assessment, health and safety considerations and material certification.”
LR’s expertise is built from its audit and assurance activities for clients, its involvement on several standardization working groups and international joint industry projects, as well as its collaboration with the group’s charitable arm, the Lloyd’s Register Foundation, which is funding research programs to address wide-ranging safety challenges related to the adoption of additive manufacturing technologies.
Leave a Reply
You must be logged in to post a comment.