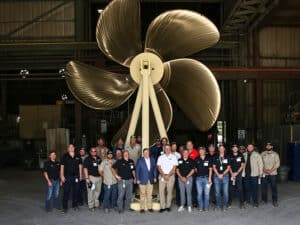
Harrison Pye called in to cure WHR headaches
Written by Nick Blenkey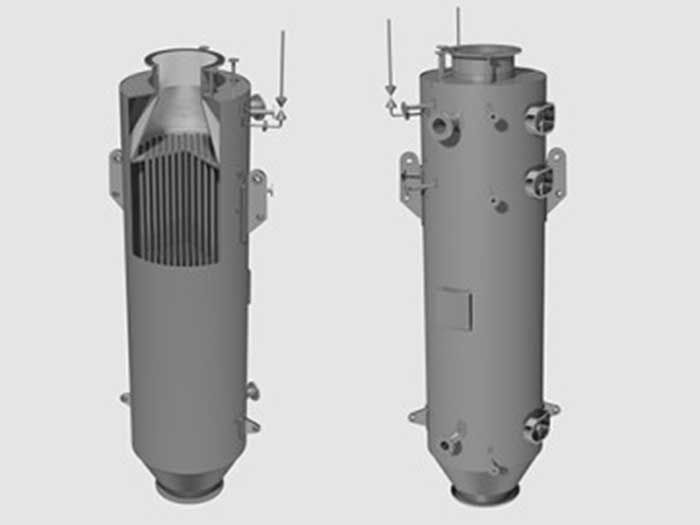
SEPTEMBER 27, 2016 — U.K.- based Harris Pye Engineering Group reports that it is actively working globally with more than ten companies and shipyards on a variety of waste heat recovery (WHR) system issues, including scenarios involving FSRUs, LNG carriers, containerships, bulk carriers and tankers.
Scopes range from standard waste heat recovery units for installation in the exhaust of gas turbines, to complete efficiency evaluations recovering usable heat from multiple sources on board.
“Vessel managers are increasingly operating their vessels in situations where slow steaming, or long periods at anchor result in reduced recovery of heat from the main engine exhaust,” explains Harris Pye’s Chief Technical Officer, Chris David. “This can result in an increase in the cost incurred in firing the auxiliary boiler. Use of the waste heat from other systems, especially from the auxiliary engine exhaust gas, can significantly reduce this additional fuel cost, and in some cases, prevent the auxiliary boiler from having to be fired.
“Waste heat recovery steam generators can also provide additional redundancy to many marine systems by ensuring that steam generating capacity for essential services can be made available, even when the primary steam generating plant is out of service or under maintenance.”
Some of the solutions that Harris Pye is currently undertaking include improving overall efficiency; analyzing slow steaming production, reducing consumption in port; offsetting ballast water treatment system running costs with heat recovery (highly topical now with the IMO BWM Convention set to enter into force in September 2017) and providing essential services during maintenance.
ANCHORED AFRAMAXES
One scenario relating to improving overall energy efficiency that Harris Pye is working with a client, concerns 25 Aframax tankers at anchor for 120 days within an ECA (Emission Control Area). The current spend on auxiliary boiler low sulfur diesel oil is in the region US$ 60,000-90,000 per year. Harris Pye is currently analyzing the possibility of using auxiliary engine cooling water to preheat the main engine jacket water as part of the overall solution.
“Of course essential services such as lube oil (LO) purifiers, hot water calorifiers, and bunker heating are still required,” explains Chris David. “So, we are undertaking evaluation and cost comparison between using electrical heating, or generating steam from the auxiliary generator engines. The payback time is then calculated from the cost of the various modifications against the consumption of low sulfur diesel oil.”
SLOW STEAMING BOX SHIPS
Another scenario relates to large container vessels slow steaming between ports and energy consumption when they are actually in port.
“Main engine waste heat recovery is not always sufficient for demand, and in-port consumption of steam can be comparatively high,” says Chris David. “Four auxiliary engines are fitted to each vessel. We have undertaken a complete analysis of various trading patterns to ascertain current consumption, power available from the auxiliary engine exhaust to produce steam, and resultant payback time for an optimised waste heat recovery unit.
“The balance of engine hours for maintenance cycles was also taken into account. Economically it is not always sound to put a waste heat recovery unit on each engine. In order to avoid excessive running hours on the engines that have been fitted with waste heat recovery, a load plan analysis was carried out to use these engines only when the main engine was unable to produce the required demand. The balance of hours over a two year per period was achieved. Payback time and long term savings were then calculated against the full turnkey installation of a waste heat recovery unit.”
POWERING BWTS
Harris Pye offers complete turn-key installations for ballast water treatment systems (BWTS). Most BWTS require a significant amount of power to run, especially to meet the more stringent USCG (US standards.
“We have undertaken a generator load analysis to ascertain the eventual load on the generators with the BWTS running in each mode of operation,” says Chris David. “The power available from the exhaust gas of the auxiliary engine has been calculated and offset against the consumption of the BWTS. The next step was the design of the waste heat recovery system and long term pay back / offset calculation provided against initial purchase cost of the BWTS.”
POWERING ESSENTIAL SERVICES
Harris Pye is working on a case involving routine maintenance on the main steam plant on a FPSO.
Steam required is for essential hotel and heating services – the cost of hiring temporary equipment and shipping to offshore location is significant.
“In this instance, working with our client we have undertaken an analysis of steam consumption under various conditions, and the required steam demand,” says Chris David. “We have also analyzed the electrical load under these specific conditions, and the theoretical power available from the exhaust of the auxiliary engines.
“Then, once again we have designed suitable waste heat recovery system, and provided a pay back calculation against the hire and freight cost of the temporary heating systems. “In working on all of these scenarios we, and our clients, are increasingly convinced that waste heat recovery systems have a vital part to play in effective energy management on a wide variety of vessels.”
Leave a Reply
You must be logged in to post a comment.