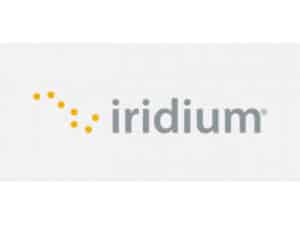
Offshore accommodation vessel surveyed using laser scan
Written byWith the help of laser scanning, Dale Stockstill & Associates (DS&A), McNeill, Miss., recently provided as-built dimensional control to a Gulf Coast shipyard for a five-story accommodation module and helipad for a vessel that serves as living quarters for offshore oil workers.
Determining whether or not such a vessel was constructed according to specified 3D design tolerances for QCI Marine Offshore, Pascagoula, Miss., was challenging, due to the flexural forces of the steel, malleability of the steel under welding and the difficulty of access. Also, crews were constructing the vessel while the as-built surveying occurred, and the sheer size of the structure made surveying difficult.
Using ScanMaster software, “bes-fit planes” along each side of a point cloud were intersected to establish the corners of the accommodation module.
After carefully choosing and tying in his scan positions, the crew chief of DS&A’s scanning crew performed the necessary scans of the helipad using DS&A’s GLS-1000 high-definition laser scanner from Topcon Positioning Systems. After the scans were registered, DS&A’s technicians provided 2D control drawings to QCI in addition to introducing the client to color mapping, which provides a visualization of design deviations. QCI provided DS&A with a 3D model of the helipad. This model was inserted into DS&A’s PolyWorks software along with the registered point cloud. A best fit between the cloud and model was obtained and the resulting deviations were depicted in a color map.
Dale Stockstill & Associates used a GLS-1000 high-definition laser scanner from Topcon Positioning Systems to develop a 3D survey of the accommodation vessel.
Extremely high-tolerance specifications for some of the required structures ranged from 3 to 15 mm. The survey crew chief proposed using the laser plummet on his Topcon GPT-3100W total station to establish four control points that were to start on the top deck and extend downward through all of the decks to the pavement beneath the structure. With the help of QCI Marine employees, the four points were positioned to avoid hitting critical components on the way down. Once finalized, the crew chief set up either the total station or the scanner on the top deck and a hole was drilled in the deck, allowing the laser plummet beam to pass through to the deck below. A closed traverse loop was run around these four points and was later adjusted and balanced out using standard survey procedures.
The crew then used its Topcon DL-502 digital level to establish precise vertical control for each control point on all decks. Starting at a previously established benchmark, the crew alternated between standard and inverted level rod shots. The standard rod was used to obtain the instrument HI (height of instrument) and the inverted rod was used on the overhead deck. After obtaining the precise elevation of the overhead deck, the survey crew chief would add 6 mm (the thickness of the deck), move to the next level and repeat the procedure. This procedure was repeated for all four control points until the crew reached the top deck. Once the control was established, precise measurements were taken on specific beams, frames and bulkheads using DS&A’s total station, GLS-1000 laser scanner and even a certified tape measure.
The high-definition laser scan determined if the structure was built to specifications, e.g., if total outside dimensions were within tolerance and if the structure was square. Starting at the closed control loop under the structure, the crew set “flypoints” for scan positions out in the shipyard. The structure was scanned on all four sides and top and the clouds registered in DS&A’s ScanMaster software. A ScanMaster routine provided a “best-fit plane” along each side of the cloud. These planes were intersected to establish the corners of the box . The cloud also contained much more information that was extracted, e.g., confirming deck heights.
Dale Stockstill & Associates also provided color maps of the bulkhead walls, which detailed the amount of “hogging and sagging” in the bulkheads. The client provided DS&A with its 3D model of the structure. The model of a given section and the cloud were placed together in PolyWorks, a color scale was chosen and comparisons were made.
According to QCI, the color-coding was greatly beneficial because that allowed QCI to define the deviations to a structural engineering firm to analyze the as-built structure in a global structural analysis in order to certify the integrity of the accommodation module. It is critical for fabrication tolerances to be within tolerance due to the direct relationship to the results of the initial structural analysis.
The laser scanner used to scan the accommodation module and helipad does not even represent the fastest available technology. In March 2010, Topcon Positioning Systems unveiled the GLS-1500, which speeds up point cloud collection at a rate of 30,000 points per second–vs. the GLS-1000’s 3,000 points per second–and a range of 150 meters with additional ranging past 330 meters.
September 12, 2011
Leave a Reply
You must be logged in to post a comment.