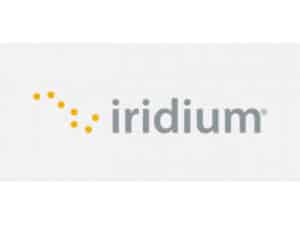
Innovative robot increases shipyard productivity
Written byThe maritime industry has often been accused of being slow to catch up when it comes to modern technology. But over the course of the last few years, companies within the industry have made some major innovative breakthroughs.
Chariot Robotics, for instance, has developed a semi autonomous robot, the ENVIROBOT, that will render the use of grit blasting, and perhaps even manual UHP water blasting, obsolete. The Florida-based company prides itself in providing a product that is not only environmentally friendly, but also beneficial to a workers safety and health.
In the past, grit blasting has been the go-to method for fast removal of coatings. But it’s an archaic and dangerous process that creates dust clouds and hazardous conditions for workers. To alleviate environmental and safety concerns, some shipyards have implemented the use of ultra high power (UHP) water jets via manual blasters for stripping, but the method has proven to be labor intensive and incredibly time consuming. Chariot Robotics saw this as an opportunity for innovation.
The initial technology for the ENVIROBOT was the result of a collaborative effort between the company and Carnegie Mellon University’s National Robotics Engineering Consortium. The partnership’s goal was to develop a highly flexible and productive robot that would strip paint using ultra high-pressure (UHP) water jets—and then, recover the water and debris in a way that would benefit the environment and worker’s safety.
THE ENVIROBOT
Considered the most technologically advanced system for removing paints and coatings from steel surfaces, the ENVIROBOT is recognized as the fastest most productive semi automated UHP surface prep equipment on the market, offering up to 1,000 ft per hour of full coatings removal—one system is equal to 20 UHP manual blasters and up to 10 manual grit blasters.
The way the robot operates is fairly simple. It holds onto the hull’s surface via special proprietary magnets—these magnets keep the robot attached to the hull whether it’s traveling vertically on the hull, or under it. Using a wireless remote control joystick, an operator at the shipyard will “instruct” the robot to travel across the hull’s surface and as it goes along UHP water jets are blasting water at 55,000 psi stripping the hull down to the bare metal. The robots vacuum then recovers all the water along with any paint particles and debris. This complete containment of paint and contaminated water is environmentally friendly and efficient since no secondary cleanup is necessary.
Aside from its environmental and safety benefits, the ENVIROBOT is also increasing yard productivity and reducing drydock time. The robot’s efficiency recently enabled a shipyard in Singapore to shave seven drydocking days off of the schedule on a Petrobras FPSO, saving all parties involved both time and money.
For more information on the robot and to watch the ENVIROBOT in action visit www.chariotrobitcs.com
Leave a Reply
You must be logged in to post a comment.