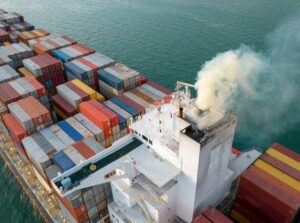
Energy-saving PBCF now adopted for 2,000 ships
Written byMitsui O.S.K. Lines, Ltd. (MOL) reports that the energy-saving Propeller Boss Cap Fins (PBCF) device has now been ordered for 2,000 vessels worldwide. The PBCF breaks up the hub vortex generated behind the rotating propeller, giving a 3-5 percent reduction in fuel consumption in the case of a large containership.
Developed by MOL, West Japan Fluid Engineering Laboratory Co., Ltd., and Mikado Japan, Ltd., the PBCF is sold by MOL Techno-Trade, Ltd.
Research and development on the PBCF started in 1986, and sales began the following year. By 2006, 1,000 vessels featured the PBCFs. Since then, it has gained worldwide recognition by vessel owners and operators, and the number of ships adopting it has doubled in just five years, reaching the 2,000 vessel milestone this year.
At a recent symposium in Germany, BMT Defence Services Ltd. of the U.K. presented a paper reporting on a before and after speed test of the PBCF using an Aframax tanker operated by a major firm, showing nearly 4% energy saving effect. This independent study once again brought the PBCF to the attention of the shipping industry and the public.
The MOL Group is promoting its next-generation vessel concept called Sempaku ISHIN, and the PBCF is one of its key technologies.
Reducing fuel consumption also, of course, reduces greenhouse gas emissions. MOL says that mandatory energy efficiency measures for recently adopted by IMO will make the PBCF even more valuable in the future.
PBCF features:
- 1) 3-5% reduction in fuel consumption and a corresponding reduction in CO2 emissions
- 2) A reduction in propeller torque
- 3) Reduced vibration in the stern less underwater noise
- 4) Reduced rudder erosion
- 5) Installation is simple and straightforward, requiring only the removal of the propeller boss caps and replacement with the PBCF. No hull modification is needed.
- 6) The PBCF is an integral part of the propeller, with no other moving parts.
- 7) The PBCF system is custom made, with design optimized for the shape of the vessel’s propellers. Lead time is three to four months from order to delivery.
- 8) It is maintenance free after installation, requiring only inspection and polishing when the vessel is in drydock, and performance does not decline over time.
August 12, 2011
Leave a Reply
You must be logged in to post a comment.