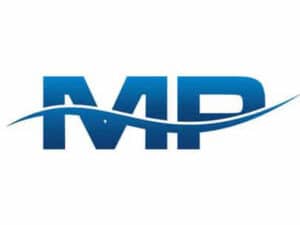
Op-Ed: Dry docks and the future of U.S. shipbuilding
Written by Heather Ervin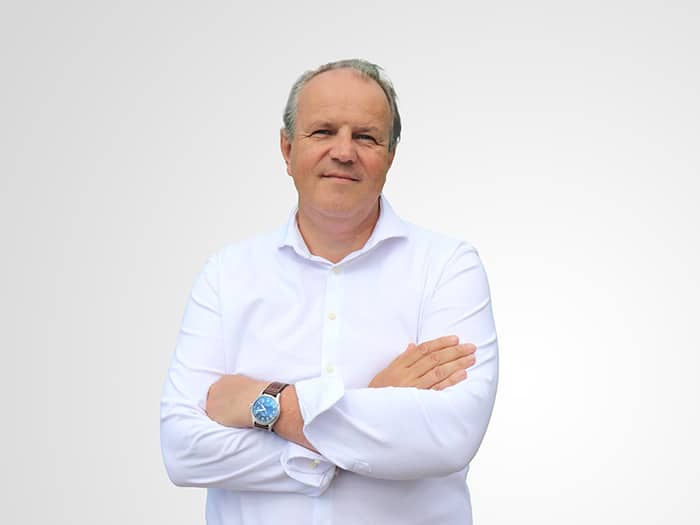
René Fredriks
By René Fredriks, Managing Director, Trelleborg Marine & Infrastructure
As global shipbuilding powerhouses ramp up capacity and innovation, U.S. shipbuilding finds itself at a critical moment. With over 100,000 American jobs and $40 billion in GDP linked to the sector, shipbuilding is not just an industrial engine, it’s a strategic asset. From naval defense and energy transport to commercial shipping and offshore wind, the infrastructure behind U.S. shipyards underpins critical national interests.
But many of those shipyards are showing their age.
Across the country, dry docks built for an earlier era struggle to accommodate today’s vessel designs, technologies, and sustainability expectations. As ships grow more complex, with hybrid propulsion, LNG systems, wind-assist devices, and high-spec military features, the dry docks that support their construction and maintenance are now as important as the ships themselves.
The recent proposed plans for the White House Office of Shipbuilding signals momentum. It brings with it the promise of funding, tax incentives, and a renewed national focus. But infrastructure modernization cannot rely on investment alone. It requires precision engineering, sustainability, and forward-thinking solutions that meet both operational and environmental demands.
Many existing dry docks use legacy systems, including conventional D-fender seals, that are no longer fit for purpose. These outdated systems often fail to deliver full watertight integrity, requiring continuous pumping to mitigate leakage, sometimes severe leakage. The result is not only higher energy consumption and CO₂ emissions, but also noise pollution, water contamination, and infrastructure degradation over time.
In a high-value, high-risk environment like shipbuilding, these inefficiencies are a liability. They increase costs, extend project timelines, and jeopardize compliance with tightening environmental regulations. And with growing demand for military builds, offshore wind vessels and retrofit programs, capacity shortfalls and avoidable delays are not an option.
Modernization doesn’t always mean massive overhauls. In fact, some of the most impactful changes come from upgrading core components.
Trelleborg’s Gina gasket sealing systems offer a prime example. Unlike multi-part D-fender arrangements, Gina gaskets provide a single, continuous watertight seal, reducing energy use, maintenance costs, and structural stress on dry dock doors. They also simplify installation and improve safety during operation. With durability of up to 120 years, these gaskets are engineered to withstand fluctuating hydrostatic pressure while, reducing rubber waste by more than 13 tons annually.
Across Europe, leading shipyards are already demonstrating what effective dry dock upgrades can deliver. At the Royal Van Lent (Superyacht) yard in Amsterdam, a Gina gasket ensures that luxury superyachts remain fully protected during construction. In Finland, a custom gasket and UHMW-PE fender panels were used to preserve the 120-year-old Pommern Museum Ship—enabling safe, watertight refurbishment without compromising heritage value.
These solutions are scalable, adaptable, and ready to be deployed in U.S. shipbuilding preparing for a new generation of naval and commercial vessels.
With Chinese shipbuilders benefiting from scale and subsidies, and new fees imposed by the U.S. Trade Representative on Chinese ship imports reaching $1.5 million per vessel, now is the time for American yards to step forward. Global competition is intensifying. But so is the opportunity to lead.
If the U.S. is serious about rebuilding a resilient, competitive shipbuilding sector, the path forward must be smarter, not just bigger. That means engineering infrastructure that performs at the same level as the ships it serves.
Modern dry docks aren’t just about concrete and steel. They are strategic enablers of national security, energy independence, and industrial growth. They reduce project risks, improve sustainability, and strengthen long-term competitiveness.
As the industry’s focus turns to next-generation vessels and low-carbon innovation, it’s time to elevate the conversation around the infrastructure that makes them possible.