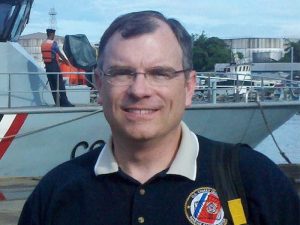
USCG names 2021 Coast Guard Engineer of the Year
Timothy Meyers has been selected as the recipient of the 2021 Coast Guard Engineer of the Year Award. Assigned to the Office of Design and Engineering Standards in Washington D.C., Meyers leads
Timothy Meyers has been selected as the recipient of the 2021 Coast Guard Engineer of the Year Award. Assigned to the Office of Design and Engineering Standards in Washington D.C., Meyers leads
SSG Michael H. Ollis: First of three new Staten Island Ferries Built by Eastern Shipbuilding Group, the 320 foot long by 70 foot beam SSG Michael H. Ollis is the lead ship
As the maritime industry continues to increase diversity and bring more women into its ranks, we wrap up 2021 for the second year in a row by bringing to you our list
The disclosures of rape and sexual assault made by the female U.S. Merchant Marine Academy cadet now known as “Midshipman X” underline the urgent need for action to eliminate violence in the
[Sponsored Content]: Cummins has long provided engines, gensets, and other applications and accessories to ferries, tugboats, towboats, fishing vessels and more. Wabtec Corporation, of which Cummins has partnered with on various sales
West Coast Clean Fuels LLC (WCCF) reports that it has executed delivery service agreements to develop, permit, manage and operate the end-to-end clean fuel supply chains for two first-of-their-kind, decarbonized maritime operations––one
By Jonathan Barnes, Marine Log Contributor Around the Great Lakes region, shipyards are busy. The need for vessels, maintenance and retrofits, and necessary infrastructure improvements, have led to a hike in activity
SPONSORED CONTENT: Beneath the decks of vessels across the country, a quiet revolution is underway. Inside their underbelly is a high-tech set of components that work in unison—quietly humming together to push
The California Energy Commission has awarded Zero Emissions Industries (ZEI) a $2 million grant to design, build and test a first-of-its-kind hydrogen fuel cell powered small, fast harbor craft. Formerly known as
Gulf Island Fabrication Inc. (NASDAQ: GIFI) today reported that it has sold the assets of its Shipyard Division along with certain long-term vessel construction contracts to Bollinger Shipyards LLC for approximately $28.6