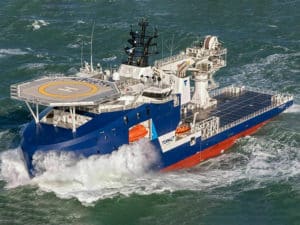
U.K. to convert offshore construction vessel to subsea protection ship
As last year’s incident involving the Nordstream pipeline in the Baltic underscores, subsea infrastructure can be extremely susceptible to sabotage. The U.K. is taking the problem sufficiently seriously that last November it