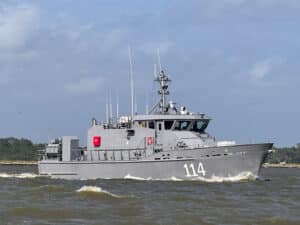
BargeRack WTIV solution gains ABS Approval in Principle
Written by Nick Blenkey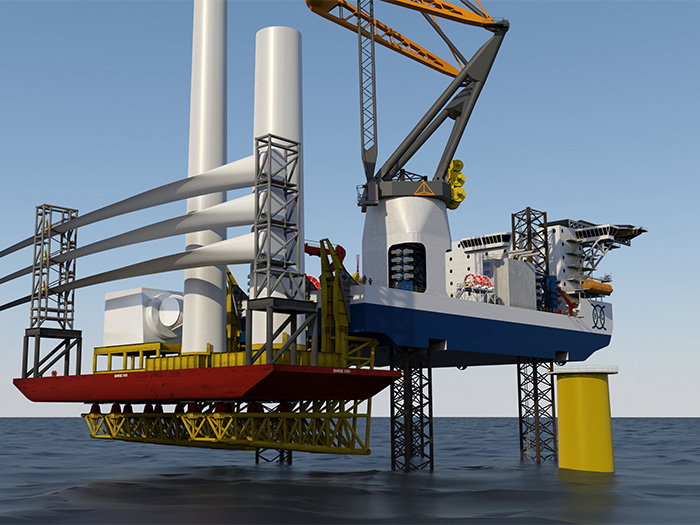
BargeRack utilizes a trussed rack fitted to the transom of a relatively small self-elevating vessel.
The American Bureau of Shipping (ABS) has granted Approval in Principle (AiP) to a coordinated design for a wind turbine installation vessel (WTIV) in conjunction with the innovative BargeRack feeder barge system by Friede and Goldman (F&G).
As we reported previously, BargeRack utilizes a trussed rack fitted to the transom of a relatively small self-elevating vessel. The feeder barge, with its turbine component cargo, is floated over the submerged rack. Once the feeder barge is secured, the self-elevating vessel uses its onboard jacking system to elevate, while also lifting the feeder barge completely out of the water.
The design was reviewed in accordance with the ABS 2017 Guidance Notes on Review and Approval of Novel Concepts.
“To achieve the scale of U.S. offshore wind market by 2030, the industry will be reliant on the delivery of the variety of vessels that will be needed to install and maintain the turbines, while navigating various port constraints” said Greg Lennon, ABS vice president, Global Offshore Wind. “ABS has been at the forefront of supporting this process, facilitating a succession of vessel developments that will prove critical to the future of this industry. This design from F&G is the latest where we are proud to be able to assist with our extensive knowledge of U.S. regulations and our deep involvement with the entire offshore wind supply chain here in the U.S.”
“F&G has developed a superior feeder vessel solution,” said Robert Clague, vice president of engineering at F&G. “Typical feeder solutions are inherently risky due to feeder vessel motions with the impact on equipment transfer. We’ve solved this problem by completely eliminating the feeder vessel motion, as well as reducing the feeder vessel cost by an order of magnitude compared to other feeder vessels.”
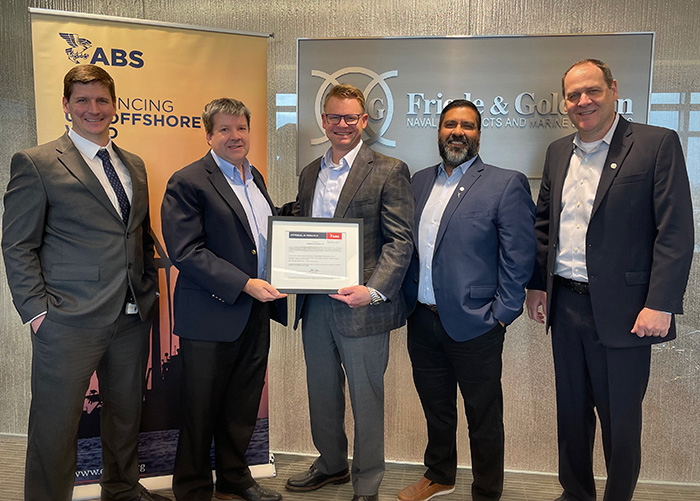