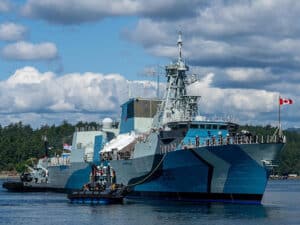
Seaspan Victoria Shipyards delivers HMCS Calgary back to Royal Canadian Navy
Victoria, B.C.-based Seaspan Victoria Shipyards has delivered the Halifax-class frigate HMCS Calgary back to the Royal Canadian Navy, marking the successful completion of the company’s second full docking work period (DWP) under