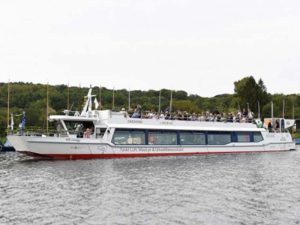
Methanol fuel cells power German excursion vessel
JANUARY 17, 2017 — Now operating on Lake Baldeney in Essen, the excursion boat MS Innogy is Germany’s first vessel powered by methanol power cells and is the result of a joint
JANUARY 17, 2017 — Now operating on Lake Baldeney in Essen, the excursion boat MS Innogy is Germany’s first vessel powered by methanol power cells and is the result of a joint
AUGUST 2, 2017—The U.K.’s Galloper Wind Farm, currently under construction 30 km off the coast of Suffolk, will come on line in 2018, generating enough power for up to 336,000 homes. Starting
MARCH 5, 2017 — Norway’s Ulstein Group has delivered the second of two SX 175 design wind farm service vessels built for Hamburg based shipping company Bernhard Schulte and Beijing based financial
JANUARY 24, 2017 — Two months ahead of schedule, the first of 67 Siemens 6 MW wind turbines has started started supplying the German electrical grid with energy from the Veja Mate
SEPTEMBER 9, 2016 — Today, Seattle, WA, headquartered Blue North, christened the F/V Blue North, one of the world’s most advanced, innovative fishing longliners. Built by Dakota Creek Industries Inc. at its
ML: Tell us a bit about your background. How did you get started in the marine business?
MD: Originally from the UK, my introduction to the Marine world can be traced back to growing up and learning to sail in my early teens—as well as the influence of my father, a mechanical engineer. To complement my understanding of science and engineering, and my sailing hobby, by the time I was University age, I chose to undertake a Naval Architecture and Offshore engineering degree. A graduate of both the Lloyds Register (LR) internship program and Lloyds Register Graduate training scheme, I have been fortunate, but also driven to obtain a diverse understanding of the global supply chain and Marine business as a whole over the 16 years I have worked for LR. Having held a variety of roles across our business and areas of operations—from London, Dubai, South Africa, South East Asia and now the Americas—each role has been an incredible professional and personal learning experience, and has given me a broad view of our clients, their challenges, the global interconnected nature of our Marine business as well as the place and importance of Lloyd’s Register both now and as we look to the future.
ML: You’ve worked with Lloyd’s Register in Europe, the Middle East and Asia. Are the challenges for a classification society any different in Americas than the rest of the world?
MD: Irrespective of geography, at Lloyd’s Register our primary aim is about helping to shape the future of shipping, while delivering solutions today – helping clients and stakeholders make the best commercial decisions based on the best technical insight. Over the years this has seen an evolution in how and what all Classification societies view as their part in the industry, from core classification to industry and individual client advisors. Clearly irrespective of geography, many of our client challenges are similar and I think one thing my global experience has taught me is that there are many synergies between geographies, segments, and clients that enable us in the Americas to be agile and expedite the best solutions for our clients.
In the Americas specifically, we operate across 14 countries and it’s important that we have both the right existing as well as future resource and knowledge base to address the challenges of our client bases as markets, ship segments, energy and social economic policies impact their operations and future strategic direction across those countries. Looking at the future of our services across the Americas, therefore, we have recently made enhancements to how we serve and work with our client bases across the region. Outside of our core Classification business and surveyors on ships, this ranges from working with the Royal Canadian Navy to developing a Regulatory regime for Naval Safety and their shipbuilding program to developing new propulsion configurations with our GE COGES (COmbined Gas turbine Electric and Steam) Joint Industry Project for LNG and ULCS construction right across the spectrum to helping understand small scale and inland waterways LNG solutions in the Gulf, South and Central America. While the challenges may be geographically unique, and different markets may require different solutions, our aim has always been to provide solutions and aid decision making for our industry.
ML: What are the biggest challenges faced by vessel operators today? Complying with stricter environmental regulations? Cybersecurity? Crew training?
MD: As you know these are very interesting times for the Marine Industry as a whole and inherent stakeholders there-in. Interestingly with the downturn in many sectors, we are seeing the emergence of an industry that, while remaining the enabler of world trade, is more open to drive innovation, offering interesting, dynamic technical solutions and careers as we search for answers to questions about the future of Marine and Offshore. The solutions to many of the challenges faced by owners today are also increasingly coming from other industries or providers not traditionally known within Marine. Aside from the ongoing regulatory changes, we are working with many owner/operators and shipyards across the world in so many areas. Sensors, data and robotics could drive safer, autonomous operations and surveys; new fuels are going to emerge to help lower greenhouse gases as well as improve local air emissions; new software tools will be developed to improve vessel design and safety oversight while also optimizing performance outcomes; and a new cyber enabled shipping that will see the development of things that we can’t predict and possibly lead to a significant and exponential disruption in the industry. We are also seeing the increasing challenge of obsolesce in newer and newer assets as well as a shift in firstly attracting then maintaining and training next generation crews.
These are very technological, challenging yet interesting and visionary times for Marine and Offshore.
ML: How do you see class evolving over the next decade? What challenges does your organization face in the years ahead?
MD: The role and place of Class societies has markedly changed over the last decade and looking forward the pace of industry change and technological advancement means we are already scenario planning for what may be needed in the next decades. It’s critical we understand and address these changes not only in terms of future core surveying capabilities and technologies but importantly to remain relevant and agile in maintaining our technology leadership and aims as an industry advisor. We often say “We are our people” and as someone who’s worked across the globe I have seen first-hand the breadth of our global knowledge base, connection and industry expectations. Ensuring we adapt to these changing needs is vital as well as ensuring we continue to invest either time or capital in understanding and shaping technology impacts to our own business with the agility to redefine what we do. To this aim we’ve working closer with industry visionaries many of whom reside in the Americas both historical marine companies but increasingly from outside of Marine. Real world solutions to industry challenges such as our joint venture project with Siemens, Dresser-Rand, Waller Marine and Conrad are examples of greater cross-industry collaboration in meeting tomorrow’s challenges.
MARCH 21, 2016 — The Bureau of Ocean Energy Management (BOEM) has taken its first step toward potential leasing for commercial wind energy development in federal waters offshore California. The agency has
FEBRUARY 25, 2016 — Waller Marine, Inc., (WMI), Houston, TX, has been contracted by Vires Energy Corporation of the Philippines to produce the Front End Engineering Design (FEED) of a nominal 400
Shipping is a crucial contributor to the economies of the Nordic countries—Denmark, Finland, Norway, and Sweden—and the industry continues to be a magnet to attract bright young talent. The region’s ship operators maintain an edge over competitors from lower cost areas by investing in newer tonnage that can be operated efficiently and they are ready to take advantage of every benefit than can be reaped from advances in technology. And, in today’s regulatory climate, it doesn’t hurt that the ecologically conscious Nordic countries are an incubator for green technology.
If we take a look at the numbers of ships controlled from Scandinavia countries published by UNCTAD, the statistics can be misleading. While Finland doesn’t make UNCTAD’s cut of the top 35 shipping nations, the Finnish Shipowners Association says its membership consists of 21 companies operating 101 ships.
What these numbers don’t show is the number of ships chartered in by the region’s shipowners or their strengths in some key sectors. The obvious example of this is Maersk Group. It is the world’s second largest shipowner in terms of its owned fleet (720 vessels totaling 25.5 million gt) but the largest in terms of number of ships controlled (767 vessels totaling 31.7 million gt).
As of the third quarter of last year, the average age of ships in the Norwegian fleet of foreign-going vessels (under Norwegian and other flags) was 10.9 years. Indicating how Norwegians keep the fleet fresh: In the first nine month of last year, 57 newbuildings totaling 2.09 million dwt were added along with 38 pre-owned vessels totaling 818,000 dwt. Equally significantly, disposals and losses totaled 126 ships and 2,.29 million dwt.
The Danish fleet is also young, in gross tonnage terms, 31.9% is under five years old, 28.7% is 5-9 years old, 23% is 10-14 years old, 12.2% is 15-19 years old and just 4.1% is 20 years old or more.
Keeping fleets young means ordering ships. Breaking down 2015 world newbuilding orders by owner’s country of domicile, we find Norway coming in at number 8, ordering 188 vessels totaling 8.7 million dwt and Denmark in the 11th place placing orders for 131 ships totaling 7.2 million tons.
PARTNERING WITH SUPPLIERS
Wherever ships are built—and whoever is buying them—a large percentage of their value is likely to be equipment produced by companies based in the Nordic region, who benefit from a willingness by the region’s shipowners to partner in trialing of equipment aboard ship in real life, working conditions.
Historically, this loop used to also include shipyards, but with the shift of shipbuilding to Asia, this is less the case today. Last year’s Danish Maritime Days included a workshop on “Lack of yard presence in innovation supply chain — How can we as an industry enable improved technology uptake through earlier involvement with the yards?”
Nobody in the room had an instant answer. But there were anecdotal references to the dangers of sharing information too readily with Asian shipyards that see nothing wrong with putting one shipowner’s bright ideas into competitors’ ships.
What remains of the region’s shipbuilding industry is mostly focused on smaller, specialized tonnage, but it retains much of the infrastructure of earlier days including, the intellectual property found in classification societies, design houses, research institutions, model basins and similar facilities—creating ships on the drawing board, the computer and in models that will eventually come to life in full-scale steel in Asia.
Meantime, of course, some yards remain very much in business and winning orders.
DENMARK: MOVING BEYOND
With shipbuilding migrating to lower cost countries, the shipyard capacity in the region has shrunk considerably. For example, there are only a handful of yards in Denmark.
One of those is Fayard A/S in Munkebo. Located on the Odense fjord, it is a large, primarily ship repair, facility whose slogan is “Speed is all—Quality is everything.” It has four large graving docks, all served by high capacity cranes, and a 700 m working berth.
Dry Dock 3, measuring 315/415 m in length and 90 m in width, is the largest dock and is capable of undertaking simultaneous construction work on a variety of ships. Dry docks 1 and 2, may be smaller in size but are 280/303 m lengths and 44/45 m widths and are used for repair and maintenance work on ships. Dry docks 4, measuring 145 m x 30 m x 8 m, is primarily used for smaller vessels. Docks 1, 2 and 4 have modern dock gates and pumping systems that allow the yard to start working on a vessel with 3-4 hours of arrival. The dock gates open or close in just four minutes.
Karstensens Skibsvaerft A/S in Skagen currently has a labor force of around 250, and can build vessels up to 135 m in length. While most are fishing vessels, the yard has been building three Knud Rasmussen-class of offshore patrol vessels, the third of which is near completion using a hull built at Poland’s CRIST shipyard last April.
Orskov Yard A/S in Frederikshavn converts and repairs all types of vessels in facilities that include two graving docks two floating dry docks with a capacity of up to 215 m x 34 m. The yard employs 230 people and cooperates closely with a wide range of subcontractors to provide all-round, one-stop solutions.
Søby Værft AS in Søby Ærø offers ship repair services using three graving docks with capacities up to 115 m x 24 m x 6 m. It also undertakes newbuildings and one project it is getting set for is the EU-supported E-ferry project, aimed at bringing into service a 4.2 mWh battery capacity electrically powered, ICE class B, single ended, drive-through RO/RO passenger ferry with one continuous main deck for trailers and cars. It will use state-of-the-art electric only systems with an automated high power charging system.
The initial aim is to demonstrate an energy efficient and emission free ferry for passengers and vehicles in an operational viable setup on the Soeby-Fynshav and Soeby-Faaborg connections in the Danish part of the Baltic Sea. The longer term aim is to see 10 more E-ferries in operation in Europe and worldwide every year, reaching a total of 100 or more by 2030— saving 100,000-300,000 tonnes of CO2 annually.
SWEDEN: WHERE DID THE YARDS GO?
The Nordic country with the fewest surviving shipyards is Sweden, where the once gigantic industry has shrunk to the point that it apparently no longer supports a national shipbuilding association—so statistics on it are hard to come by.
Newbuilding is pretty much confined to Saab Kockums naval shipbuilding activities and a handful of small yards involved in smaller tonnage.
Two large repair facilities are still operational. Oresund Dry Docks, in Landskrona on the Øresund Strait beween Denmark and Sweden has facilities that include a 195 m x 35 m graving dock and a 165 m x 28 m floating dock. Damen Oskarshamnsvarvet, on the west coast, has facilities that include an 80 m x 15 m floating dock. Activities at Damen Shiprepair Götaverken in Gothenburg ended in 2014, due to “the depressed situation of the Scandinavian shipping market, the increased number of Baltic repair docks and the appreciation of the Swedish Krona (SEK).
Though Gothenburg no longer has a shipyard, it still has one of Europe’s best known towing tanks, operated by SSPA Sweden AB.
SSPA has the capability to perform most kinds of model testing in its facilities: the towing tank, the large cavitation tunnel and the seakeeping and maneuvering basin – Maritime Dynamics Laboratory, (MDL). Wind tunnel tests can be performed at external test facilities.
All test facilities at SSPA are designed for performing tests with large models, which have many advantages as scale effects are reduced and more reliable measurements can be performed.
NORWAY, HANGING IN THERE
For those interested in the preservation of Norwegian shipbuilding capability, a big question in the months ahead will be whether the Vard Group, a Fincantieri company, can continue to keep five Norwegian shipyards alive based on its previously successful strategy of supplying primarily the offshore oil and gas sector with specialized vessels designed and fitted out in Norway using hulls built in Romania.
In addition to its Norwegian yards, Vard has two yards in Romania, two in Brazil and one in Vietnam. Vard’s biggest recent headaches have included well-documented problems with its Brazilian activities and it has said that these are under review.
Outside of Brazil, Vard’s problems are those shared by all shipbuilders historically dependent on the oil and gas sector—getting enough orders to keep capacity occupied and diversifying into other sectors.
Its most recent order came in November and was for design and construction of what was described only as “one offshore vessel for an undisclosed international customer.” It is being designed by Vard Design in Ålesund, Norway. The hull will be constructed at Vard Braila in Romania and outfitting and delivery is scheduled from Vard Langsten in Norway in 2017.
That order followed contracts worth a total $100 million for the design and construction of two offshore subsea construction vessels for Dubai-based Topaz Energy and Marine. The hulls will be constructed at Vard Tulcea in Romania, with delivery scheduled from Vard Brattvaag in Norway.
In the fisheries sector, Vard last year secured an order from Brevik AS of Norway for a coastal fishing vessel, but, for this vessel, Vard Braila in Romania will undertake all stages of production.
Another fisheries order came from a Canadian client and was for a 79 m stern trawler of Rolls-Royce NVC 374 design. Vard Braila will build the hull and the vessel will be fitted out at Vard Aukra in Norway in the fourth quarter of 2016.
Thus far, Vard has either not been looking at the offshore wind sector or has been keeping very quiet about it. That’s not the case with other Norwegian shipbuilders.
A significant current project currently under way at the Ulstein shipyard is the fitting out of the first of two innovative offshore wind industry Service Operation Vessels (SOV) being built for Germany’s Bernhard Schulte Offshore GmbH that will be Ulstein’s first for the offshore wind industry — and the first to feature its innovative X-Stern which allows a vessel to be positioned with the stern faced towards the weather instead of the bow.
The hull of the first X-Stern SOV hull arrived at Ulstein’s Ulsteinvik shipyard in January and is scheduled for sea trials starting late spring. Starting this summer, the vessel will work at the Gemini wind farm in the Netherlands for Siemens Wind Power Service.
A project underway at Fjellstrand AS is another pointer to the growing attraction of offshore wind service opportunities in a depressed oil and gas market. It is converting a platform supply vessel it delivered only in April of last year into a wind farm support vessel.
Havyard Group established its credentials in the offshore wind sector with the delivery last February of the first of three Havyard 803 SOVs to Denmark’s Esvagt. In addition, Havyard has an order from Esvagt for aa design and equipment package for a Havyard 931 CCV crew change vessel that will be built at Spanish shipyard Astilleros Zamakona.
Late last year, Esvagt ordered a further Havyard SOV, aimed at a new niche for vessels of this kind, smaller wind farms. This Havyard 831 design is described as compact and efficient, but with ample capacity to transport service personnel and equipment. The first Havyard 831is also being built outside Norway, at the Cemre shipyard in Turkey.
Though design and equipment deals are obviously profitable for Havyard, that leaves shipyard capacity to be filled and another sector where it has been successful is the design and construction of large fish carriers. Last November Havyard was able to fill a gap in production of these vessels by using the covered building dock at its Leirvik shipyard for refit and refurbishment of two Faroese fishing trawlers.
Kleven, operates two shipyards—Myklebust Verft and Kleven Verft—and its orderbook includes a deep sea minerals exploration vessel and several fisheries vessel in among the AHTs and OCVs.
A recent contract came from Sølvtrans and is for delivery of a live fish carrier vessel for Myklebust Verft. This is Kleven’s second order from Sølvtrans for this type of vessel, both of which are being built to to Rolls-Royce NVC 387 design.
While ship designs are part of the stock in trade at Ulstein, Vard and Havyard, Kleven’s orderbook is pretty much a portfolio for Norwegian specialist ship design firms. The deep sea minerals vessel, which is on order for De Beers Marine Namibia, is being built to MT 6022 design from Marin Teknikk. This design is well proven in the offshore construction segment, but the De Beers ship will include a wide range of tailor made equipment and features.
A large pelagic midwater trawler/ purse seiner that Kleven is building for Gitte Henning AS in Skagen, Denmark, is based on a design from another well known independent design house, Salt Ship Design, which in October had 16 vessels of its design under construction at Norwegian and foreign shipyards.
“Unlike the current offshore market, fisheries and fish farming are doing very well and these segments represents an increasingly important market for Salt,” it said.
In addition to the independent design houses and shipyard design divisions, Norway is also the home of Rolls-Royce’s and Wärtsilä’s Ship Design divisions, which have absorbed various independents over the years. Having a ship design department makes all sorts of sense for both of them, as a ship design is the envelope for, quite literally, a boatload of equipment and systems.
FINLAND, BACK FROM THE BRINK?
In Finland, thanks largely to government support —including diplomatic efforts— a large part of the shipbuilding industry has emerged from the ashes of what was STX Finland.
Most importantly, with a lot of Finnish Government coaxing, Germany’s Meyer Werft has acquired the Turku shipyard, enabling it to continue as one of the world’s premier cruise ship yards.
Shipbuilding has also returned to the Rauma shipyard after STX announced its closure in 2013, with the site being sold to the local municipality. The shipyard reopened as Rauma Marine Constructions Oy (RMC) the following year and in December 2015 reported that it was to “receive a major infusion of capital for further growth from the government backed Finnish Industry Investment Ltd, and two investment companies, Finda and a fund managed by Taaleritehdas. That news came the day after the Finnish Ministry of Defense issued a Request For Information to kick off a long planned plan to build four new corvette size vessels.
The Rauma shipyard also has considerable expertise in the area of icebreaking vessels — which keeps what is now Arctech Helsinki Shipyard from having a monopoly in that area. When STX Finland ’s troubles threatened the survival of the Helsinki yard, Russia’s United Shipbuilding Company took a 50% stake in and subsequently took total ownership control and the yard’s orderbook primarily includes advanced icebreaking tonnage for Russian projects, though an icebreaker for the Finnish Transportation Authority is currently fitting out.
The other repository of Finnish icebreaking knowhow is ice-going vessel design and engineering specialist Aker Arctic, whose capabilities include ice model testing. Its largest shareholder is Finnish Industry Investment, which is also major stakeholder in the reborn Rauma yard.
MV Veteran, 80m Ice Class Ferry
Delivered this past October by Damen Shipyards Galati, Romania, the RoPax ferry MV Veteran is built to handle the tough environment of the Arctic region. The 200-passenger vessel was designed to operate specifically in icy waters by a partnership comprised of Fleetway Inc., for the Government of Newfoundland and Labrador, and Denmark’s Knud E. Hansen.
The MV Veteran can handle 40 cm-thick floating ice at 4 knots, says Jan van Hogerwou, Damen Manager, North America. The ferry’s “rudders, hull and propellers have been strengthened and are outfitted with extra plate thickness for heavy winter conditions.”
Three MTU 16V 4000M23S engines generate 1,700 kWe, 400V, at 1,800 rev/min. The emergency genset is provided by one Volvo D16 engine generating 440 kWe 440V, at 1,800 rev/min. Its propulsion set is made up of two 1,600 kW Rolls-Royce azimuth thrusters, Electric Drive, and two 2,600 mm ice strength fixed pitch propellers.
And while the vessel was built in Romania, its very much a Canadian product, with several Canadian companies providing services for the vessel, with products including electrical equipment to fire-fighting systems.
MV Veteran has roll-on, roll-off capacity for 60 vehicles, is 80.9 m long with a beam of 17.2 m and can operate at a cruising speed of 14 knots.
The first in a two-vessel contract, the Veteran, and its sister ship the MV Legionnaire, are part of a large “lifeline” vessel replacement program being undertaken by the Provincial Government to modernize its fleet. The fleet transports over 900,000 passengers, 400,000 vehicles and 20,000 tonnes of freight with more than 50,000 arrivals and departures every year.
MV Veteran is class by ABS +A, Vehicle Passenger Ferry, Ice Class 1AA, Near Coastal, Voyage Class II, E, +AMS, HAB+, ACCU GP.
Product Director at Damen Ferries, Henk Grunstra, acknowledges that the Ice Class 1A Super certificate in the highest available for ferries. He also says the vessel has redundant systems in place for safe operation.
MV Veteran features 127 seats in the forward passenger lounge, 88 seats in the aft passenger lounge, 15 single crew cabins.
The Sally Fox, 105 ft fast ferryLast April, a new foxy lady on the Puget Sound made her presence felt. Built by All American Marine, Bellingham, WA, the MV Sally Fox, is the first of two new ferries ordered by King County’s Marine Division. The vessel is also the first ferry to be built under the U.S. Coast Guard’s Sub-Chapter K rule, and delivered under the new 5A Space Performance Guidelines issued.
The 5A Space Performance Guidelines make it possible for a boat builder, such as All American Marine (AAM), to design and implement suitable structural fire protection in very low fire load spaces in the construction of weight-sensitive high-speed passenger vessels.
The 105 ft x 33 ft catamaran was designed by AAM, however, for its wave piercing hull design the builder called upon New Zealand-based naval architecture firm Teknicraft Design Ltd. The wave piercing hull design helps reduce drag and enhance passenger comfort.
Sally Fox is powered by twin Cummins QSK-50 tier II engines rated at 1,900 rev/min. The 250-passenger ferry operates at a service speed of 28 knots across the Puget Sound from Vashon Island to downtown Seattle.
Special attention was paid to each passenger deck’s layout in order to facilitate and streamline the boarding and disembarking process. Additionally, the new ferry features some green technologies, for example, instead of paint, the decks are covered with a peel-and-stick non-slip tread, while the exterior of the superstructure is wrapped in UV-stable vinyl.
Funded by federal grants, the new water taxi will replace the Melissa Ann, a 27 year old vessel leased to operate on the route since 2010. Its sister ferry, the MV Doc Maynard was delivered by AMM September 2015.
Baynes Sound Connector, Longest Cable Ferry
Next month, BC Ferries’ first ever cable ferry, the Baynes Sound Connector will make its long awaited debut and begin operations. Built by Seaspan’s Vancouver Shipyards, the 78.5 m ferry will accommodate 150 passengers and 50 vehicles on a 1,900 meter (about 1.9 km) route, making the ferry one of the longest cable ferries in the world.
Baynes Sound Connector will travel at a speed up to 8.5 knots between Buckley Bay and Denman Island. The ferry operates on one drive cable, and two guide cables along the route on the Baynes Sound Channel. Operator BC Ferries expects the cable ferry will help reduce operational costs, saving the company over $80 million over its expected 40-year service life; will have a smaller environmental footprint and lower fuel emissions.
While the news of the Baynes Sound Connector is exciting, the project was initially met with fears from the local community that felt a ferry operating on cables would be unsafe and wouldn’t be able to meet BC’s promise of a more efficient ferry on the run.
BC Ferries has stated that the ferry has been designed and built to safely operate in the Bayes Sound environment, which is a relatively low marine traffic area, and was tested in some of the worst weather conditions.
To further safety, it was recently announced that transit lights have been installed at both the Buckley Bay and Denman West terminals to secure safe passage for the cable ferry and other vessels in the area. A green light would indicate that the Baynes Sound Connector is docked at a terminal and boaters can safely cross the channel. A red light indicates the ferry is in transit, and it may not be safe for other vessels to cross the channels since the cables in operation may not be fully submerged.
Texelstroom, CNG Hybrid FerryBuilt by Spanish shipbuilder Construcciones Navales del Norte—La Naval, the 135m Texelstroom will offer its owner, Royal N.V. Texels Eigen Stoomboot Onderneming (TESO), a unique energy efficient vessel package that will combine a variety of green energy sources to help reduce its environmental impact when its delivered 1Q 2016.
The 1,750-passenger ferry is equipped with a hybrid propulsion system comprised of dual fuel (diesel/CNG) generating sets and a battery system, feeding the propulsion electric motors. The ferry is expected to operate mainly on the natural gas that will be storing two batteries of Compressed Natural Gas (CNG) bottles installed on the top deck.
The double-ended ferry was designed with two separate navigation bridges and two independent engine rooms. One engine room is fitted with two ABC diesel engines, each generating 2,000 kW of power; and the other engine room is fitted with two ABC dual fuel engines, also generating 2 x 2,000 kW. Each ship end will be fitted with two Rolls-Royce azimuth propeller.
The ferry, designed by La Naval in close cooperation with TESO and C-Job Naval Architects & Engineers, and classed by Lloyds’ Register, will also feature over 700 m2 of solar panels, helping the ship to be more sustainable. Additionally, according to LR, the ferry’s design is supported by the European Union’s “I.Transfer” program. The goal of the program is to make ferry transport accessible and sustainable.
The ferry will be ice class, featuring a strengthened hull to operate through winter ice, and will have a notation for Passenger and Crew Accommodation Comfort (PCAC) to ensure a safe and comfortable journey for passengers and crew.
Texelstroom will provide services in The Netherlands, between the island of Texel and the port of Den Helder. The ferry, which will also have capacity for 350 vehicles, will operate between 10 to 15 knots.
Ampere, Zero-emission Battery Powered Ferry
Norway was one of the first countries to embrace the move to alternative energies; the country was one of the earliest adopters of LNG as a marine fuel, and now it is the homebase for the world’s first battery powered electric car/passenger ferry. Built by Fjellstrand Shipyard, the 80 m long x 21 m wide Ampere produces zero emissions thanks to its Siemens’ BlueDrive PlusC electric propulsion system. The ferry does not use any fuel tanks or engines. Instead, it derives its power from its batteries which enable Norled to reduce its fuel costs by up to 60%, and save one million liters of fuel annually.
Ampere’s power system is made up of 224 Corvus Energy AT 6500 modules with a total capacity of 1.46MWH, an energy management system, a steering system, thruster control and an alarm system. The Energy Storage System (ESS) is split into four parts. Each of the vessel’s ends is fitted with a vessel mount and a shore power station—this enables and facilitates the rapid recharging of the batteries.
The innovative vessel is meant to be as environmentally friendly as possible, from the inside-out. Constructed from light-weight aluminum, the Ampere, weighs just half of what a conventional ferry would weigh. Its service life is double that of a steel hull ferry, and the vessel requires fewer drydock periods which help lower the vessel’s maintenance costs.
The Ampere is also equipped with LED lighting, high efficiency thrusters with feathering propellers from Rolls-Royce, and a HVAC system with extensive heat recovery. The ferry, which has passenger capacity for 350 and room for 120 cars, is classed by DNV-GL as 1A1- LC R4(nor), CF, C, BP, IOPP-A.
Mein Schiff 4, 99,500 grt cruise shipDesigned for the German premium-class cruise market, the 99,500 gt Mein Schiff 4 is the fourth in a series of cruise ships being built for TUI Cruises, a joint venture between TUI AG and Royal Caribbean.
Mein Schiff 4 was constructed using advanced and eco-friendly technologies according to ship builder Meyer Turku Shipyard, Finland. The ship was built to be as environmentally friendly as possible. Its expected to consume 30 percent less energy when compared to other ships its size. The cruise ship is also fitted with a combined exhaust after-treatment system, made up of a scrubber and a catalyzer, lowering sulfur emissions by as much as 99 percent, and NOx by 75 percent.
Engine power is provided by two Wartsila 12V46 diesel engines and two Wartsila 8L46F diesel engines.
The ship is 294m long x 36m wide, with an 8m draft. It features 1,253 cabins, and has capacity for 2,790 passengers and 1,030 crew members.
Mein Schiff 4’s initial itinerary included traveling through a variety of routes in the Baltic Sea to the Baltic States and in Northern Europe around Norway. This winter, the ship will travel to the Canary Islands making stops along Morocco and Mediera.
Mein Schiff 4 is classed by DNV-GL +1A1 Passenger Ship BIS Clean F(M) Fuel (991 kg/m3, -7°C, 380 cSt) LCS(DC) TMON. Sister ships Mein Schiff 5 and 6 will be completed and delivered by the Meyer Turku yard by 2017.
Samish, 144-Car Ferry
The second in a series of four Olympic Class ferries for Washington State Ferries, the 144-Car Samish, was named in honor of the region’s native Samish Indian Nation. It’s name means “giving people,” and Washington State Ferries is hoping to do just that, by giving back to the community with the addition of the Samish to its growing ferry fleet.
Delivered by Vigor Industrial, the new $126 million ferry, like its sister ship, the Tokitae, is based on the Olympic Class design by Seattle-based Guido Perla & Associates, Inc. The ferry measures 362 ft x 83 ft and has capacity for 144 cars and 1,500 passengers.
The Olympic Class, is built by a group of Washington-based companies—led by Vigor Industrial—offering the very best the state has to offer in design and production; and generating and supporting over 500 jobs in the Puget Sound.
Its superstructure was build by Whidbey Island, WA-based Nichols Brothers Boat Builders. Nichols built the superstructure for the Tokitae and will do the same for the third and fourth vessels in the series.
Olympic Class vessels were designed with passenger comfort in mind. The class provides wider lanes and more spaces for cars and trucks, additional comfort for passengers with two Americans with Disabilities Act-compliant (ADA compliant) elevators, an ADA-compliant car-deck restroom; flexible seating configurations; improved heating and ventilation; and wider stairwells and passageways.
Samish’s main propulsion is provided by two Electro-Motive Diesel (EMD) engines developing a total 6,000 hp, enabling the vessel to reach speeds up to 17 knots on its Anacortes to San Juan Islands route. Olympic Class ferries are also equipped with the latest emergency-evacuation and fire-suppression systems.
Samish and the other vessels in the Olympic Class also provide WSF with improved efficiency and better fuel consumption. Its hull design helps reduce wake, further improving fuel efficiency. The ships will replace the aging Evergreen State Class vessels which have been in operation since the 1950’s.
F.A. Gauthier, First LNG ferry for North AmericaCanada’s Société des Traversiers du Québec (STQ) is committed to a greener future. To that end the company invested in the construction of three LNG-fueled ferries in between 2014 and 2015, including the F.A. Gauthier, which was delivered to the operator this past summer.
Built by Italy’s Fincantieri Castellamare di Stabia shipyard, the F.A. Gauthier has the distinction of being the first LNG-fueled ferry to operate in North America. Classed by Lloyd’s Register, the ferry is fitted with an ultra compliant, low-emission, dual-fuel system from Wärtsilä.
Powered by four Wärtsilä 12v34D dual-fuel generating sets, meaning the ship can run on either Liquefied Natural Gas (LNG) or Marine Diesel Oil (MDO), the 133 m x 22 m ferry can reach a maximum speed of 20 knots on its Matane-Baie-Coreneau-Godbout route.
The ship is also equipped with Wärtsilä’s LNGPac system comprised of LNG bunkering, storage tanks, and handling equipment. Its fitted with two contra-rotating propellers, making the ferry exceptionally maneuverable.
The F.A. Gauthier’s hull is certified as Ice Class 1 and Propulsion Class 1, enabling the ship to break sea ice and handle adverse weather conditions on the Gulf of St. Lawrence. The ferry can carry 900 passengers and 180 vehicles on each trip, and is expected to transport more that 205,000 passengers and 118,000+ vehicles a year.
Viking Star, 48,000 grt cruise ship
Viking Ocean Cruises made its debut into the ocean going cruise market last year with the delivery of its highly anticipated 930 passenger Viking Star. The ship is the first of three cruise ships under construction at Fincantieri Marghera, Italy shipyard for the brand—which is a spin off of Viking River Cruises.
The goal for Viking Ocean Cruises was to bring the focus of cruising back to the destination. With that in mind, the brand decided to build a smaller passenger cruise ship, with a smarter design and providing guests with an enriching trip.
What makes the “small” cruise ship unique is that its engineered at a scale that enables the ship to have direct access into most ports, making embarkation and debarkation effectively easier and more efficient for guests. This lets passengers spend more time at each destination along the ship’s route.
The Viking Star’s design pays homage to the brand’s Nordic heritage, effectively immersing the passenger into local surroundings. Clean lines, woven textiles and light-wood help evoke the Viking spirit of discovery, according to the brand, and helps connect the passenger with nature.
The 228m long ship, which features 465 state room—each with its own veranda—has two pools, a main pool with a retractable roof, and a glass-backed infinity pool cantilevered off the stern; the ship also includes indoor-outdoor spaces for al fresco dining, large windows and skylights that further blur the light between inside and out, and a wrap-around promenade deck that pays homage to classic ocean liners.
Viking Star was also designed with the environment in mind. The ship is powered by energy-efficient hybrid engines, hydro-dynamically optimized streamlined hulls and bows for maximum fuel efficiency, onboard solar panels and equipment that minimizes exhaust pollution and meets the strictest environmental regulations.
Oscar B. 115 ft ferry, Wakiakum CountyWahkiakum County, Washington State is paying homage to one of the greatest skippers the country has ever had by naming the county’s newest ferry, the Oscar B, after him. Oscar Bergseng skippered the ferry, Wahkaikum, which was built in 1961, for 17 years.
Built by Nichols Brothers Boatbuilders, Freeland, WA, the 115 x 47 ft Oscar B is double the size of its predecessors, offering an expanded vehicle capacity.
The new ferry can carry 100 passengers and 23 cars between the Cathlamet, WA and Westport, OR terminals.
The ferry, designed by Seattle’s Elliott Bay Design Group, features a steel-hull, aluminum super-structure. Its power is provided by two state-of-the-art Cummins QLS diesel engines, each delivering 285 hp at 1,800 rev/min and couple to ZF Marine reversing reduction gears with two fixed-pitch propellers.
Oscar B meets all current U.S. Coast Guard requirements. Additionally, it features a hydraulic steering system, up-to-date electronics, a passenger lounge and ADA-accessible restrooms.