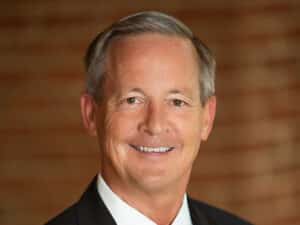
Op-Ed: Digitalization alleviates drydocking delays
Written by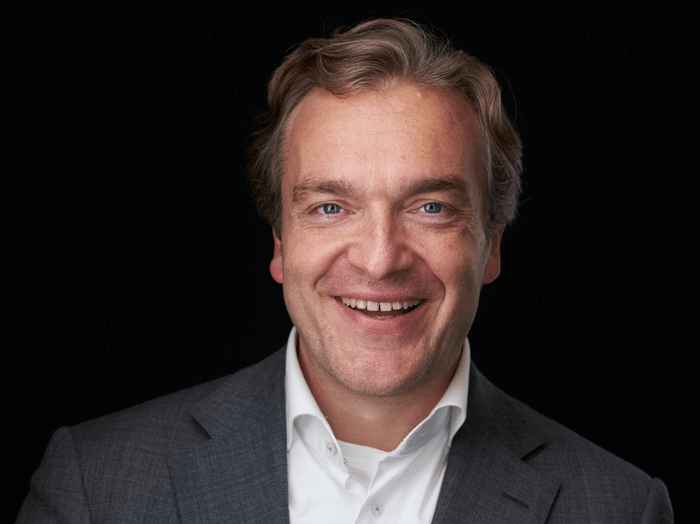
Kristof Adam, General Manager Europe, W&O
By Kristof Adam, General Manager Europe, W&O
Drydocking is one of the most important maintenance activities in a vessel’s lifecycle, and a failure to plan for it properly can cost owners a lot of time and money. This op-ed highlights how digitalization is being applied to valve management and replacement to transform the dry-docking process.
Every vessel is required to dry dock at least once every five years and requires a lot of preparation and planning. Insufficient planning will lead to more urgency work and will escalate costs. Speed is a crucial factor, with operators and owners wanting to get in and out as quickly as possible to minimize operational losses. When it comes to the replacement of overboard valves planning needs to be spot on. Often, the valves conditions are unknown, or the vessel is unaware of the exact specifications ahead of the vessel going into drydock. This increases the challenge for the dry-dock management team to have the ship refitted and back in operation as soon as possible.
Ship surveying during dry-docking to determine valve condition has its risks and often leads to valves being ordered and sourced in a hurry. In these circumstances, and without expert knowledge, project teams will buy valves based on what is available, rather than what is most suited to the job. Rushed surveying, ordering increases the risk of sourcing incorrect valves, invalidates quality control measures and increases transportation costs as parts may need to be flown to the dry-dock location.
The industry is already responding to significant changes, from digitalization and data analytics assisting in voyage optimization and energy efficiency retrofit decisions. This is also reflected in the valve supply sector, which can use digital technologies to ensure replacement valves are delivered and installed on time and avoid the need for last-minute valve testing, which can cause delivery or installation delays.
INFORMED DATA DRIVEN INSIGHTS
The adoption of digital technology is helping owners and operators to optimize their operations and reduce costs. For replacing and repairing valves and fittings, digitalization is helping to put asset health and condition data in the hands of vessel managers, allowing them to make better decisions about procurement and supply chain management.
FOCUS ON THE DETAIL
Many ship owners and operators know very little about the valves on their ships, often the only available list of valves is the one from when the vessel was originally constructed. If valves have been replaced in the past, even basic information about a valve, size, internals, dimensions or materials of construction, maybe difficult to find without a laborious search of paperwork. Without accurate and accessible documentation, the risks of ordering incorrect valves, which can lead to breakdown and equipment damage, are greatly increased.
PREPARATION IS KEY
A pre-dry dock survey of the valves on a vessel can mitigate these risks. Using a list supplied by the vessel owner as a starting point, an expert technical team can go onboard to identify and check the valves. Surveys typically require about a day, and can be completed anytime the vessel is in port. Once the survey is completed, the dry-docking team can work to source the necessary valves at a competitive price, and ensure they are fit for purpose ahead of the dry-docking.
RFID TAGGING
Having a clear inventory of the valves on-board and a documented history is essential to good valve management across a fleet. As part of its pre-dry dock valve survey, W&O applies RFID tags to valves, digitizing the valve record and making future surveys simpler. RFID tags contain data on valve size, brand, materials, information on the actuator, testing certificates, its shipping and installation dates, and its inspection history, along with photos taken during its service lifetime. All this data is available to the technical surveyor and the vessel representatives through a smartphone app ensuring consistency, accuracy and ease of management.
Through the innovative use of technology, and the development of new approaches to service delivery, shipowners can save time and money spent on surveys by using smart data insights. Digitising valve data using RFID tagging allows owners to track valve condition over time and incorporate the information into their digital platforms and integrate information into resource planning software, helping to clean up the data on installed valves.
Shipowners need to be able to make the right decisions at the right time and reducing room for error or inaccuracy can smooth the process of valve identification and ordering to make a real commercial difference to owners. Accessing digital technologies and technical expertise can ensure that the right replacement valves for the job are delivered on time, and at a competitive price for successful dry-docking.