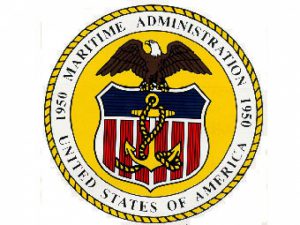
MARAD awards $20 million in Small Shipyard Grants
JULY 24, 2018 — The U.S. Department of Transportation’s Maritime Administration (MARAD) today awarded more than $20 million in grants to support capital improvements at 29 U.S. small shipyards as a part