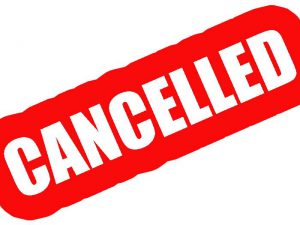
PPL Shipyard terminates three jack-up contracts
OCTOBER 4, 2017 — Sembcorp Marine reports that wholly-owned subsidiary, PPL Shipyard Pte Ltd has terminated three contracts with Mexico’s Integradora de Servicios Petroleros Oro Negro, S.A.P.I. de C.V. and its subsidiary Oro