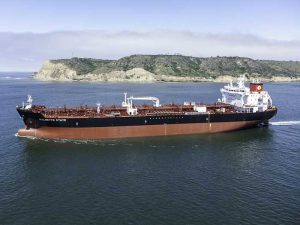
VIDEO: NASSCO completes eight ship ECO tanker series
JUNE 7, 2017 — General Dynamics NASSCO today delivered the final ECO Class tanker constructed as part of an eight-tanker, two-customer program. The ship, Palmetto State, was delivered to Kinder Morgan subsidiary