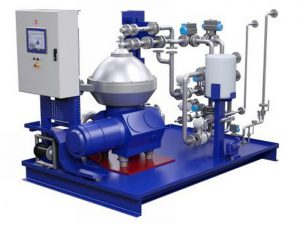
Alfa Laval gives EGR water treatment a smaller footprint
NOVEMBER 2, 2015 — For many shipowners, Exhaust Gas Recirculation (EGR) is emerging as an attractive option for compliance with the Tier III NOx emission limits that will soon apply in the
NOVEMBER 2, 2015 — For many shipowners, Exhaust Gas Recirculation (EGR) is emerging as an attractive option for compliance with the Tier III NOx emission limits that will soon apply in the
The project involved retrofitting two MAN B&W S70ME-C HFO-burning engines in the chartered Q-Max vessel Rasheeda with gas-burning M-Type Electronically Controlled – Gas Injection (ME-GI) Systems, which have now been successfully commissioned.
The retrofit modification meets all current and foreseen global emissions regulations.
Nakilat-Keppel Offshore & Marine (N-KOM) carried out the conversion at its Erhama bin Jaber Al Jalahma Shipyard facilities in the major Qatari port of Ras Laffan Industrial City.
The project collaborators, including MAN PrimeServ, installed the ME-GI system on the vessel at the shipyard in June 2015. The partner for the ME-GI fuel supply system is TGE Marine Gas Engineering GmbH,
Christian Ludwig, Head of Retrofit and Upgrades, MAN PrimeServ, said: “This is a fantastic milestone in our company’s history. It is a lighthouse project, and there has been a remarkable partnership and cooperation through this historic conversion. Our ME-GI order book now stands at 140 orders – for different vessel sizes and applications, which we see as a compelling case for our technology to be designated the industry standard.”
Nakilat Managing Director Eng. Abdullah Al-Sulaiti, said, “The success of the ME-GI project is the culmination of years of cooperation with Qatargas, RasGas and MAN Diesel & Turbo as turnkey project manager. In late 2013, Nakilat worked with our charterers to implement a pilot conversion on Q-Max Rasheeda, the first retrofit ME-GI project ever to be implemented in the marine industry. This is a milestone moment for all involved parties.”
MAN Diesel & Turbo reports that the vessel’s ME-GI units have displayed a seamless change between fuel-oil and gas operation – a key characteristic of the ME-GI technology.
The Qatar fleet comprises 14 Q-Max and 31 Q-Flex LNG carriers, all using dual MAN Diesel Turbo’s S70-ME low-speed diesel engines for propulsion.
THE ME-GI ENGINE
The ME-GI engine gives shipowners and operators the option of utilizing oil or gas fuel depending on relative price and availability, as well as environmental considerations.
The ME-GI uses high-pressure gas injection, allowing it to maintain the attributes of MAN B&W low speed engines that have made them the default choice of the maritime community.
The ME-GI is not affected by the derating, fuel-quality adjustment or methane-slip issues that have been seen with other dual-fuel solutions.
MAN Diesel & Turbo sees significant opportunities for gas-fueled tonnage as fuel prices rise and exhaust-emission limits tighten. Research indicates that the ME-GI engine delivers significant reductions in CO2, NOx and SOx emissions, with its negligible methane slip makes it the most environmentally friendly technology available.
An ME-LGI counterpart that uses LPG, methanol and other liquid gases is also available and has already been ordered.
AEG’s Advanced Maritime Emission Control System (AMECS), essentially, takes a barge-mounted scrubber system to the ship. Unlike existing shore power options, it does not require retrofits to each vessel.
“AMECS is a game-changer in the fields of emission control and air quality. Multiple AMECS units can remove thousands of tons of pollutants each year,” said Ruben Garcia, President of AEG. “These mobile barge-mounted systems use patented technology to attach to the auxiliary exhaust stacks of nearly any vessel entering port – at-berth or at-anchor – eliminating the need for expensive ship retrofits, and providing the public with cleaner air.”
AMECS is approved for simultaneous emission capture from two exhaust stacks of a single ship, with independently verified test results proving 90% to 99% reduction of the particulate matter (PM), nitrous oxides (NOx), and sulfur dioxides (SO2) found in diesel exhaust.
“CARB’s approval of AMECS as an alternative to the at-berth emissions reductions rule provides the flexibility our shipping lines need while protecting our environment and creating new jobs for our communities,” said representatives from the Port of Long Beach, a strong supporter of AMECS throughout its development.
In 2013, the Port of Long Beach provided about $2 million in seed money to help test the AMECS system.
“We’re thrilled any time we can find more tools to reduce emissions and continue to improve community health. That’s why we fund projects like the demonstration and testing of these new technologies, through our Technology Advancement Program,” said Board of Harbor Commissioners President Lori Ann Guzmán. “We’ve made a lot of progress in reducing air pollution, and we are nurturing new technologies like these to help us do even more.”
Called “Project Forward,” it aims to to develop a commercially feasible LNG-fueled dry bulk carrier design capable of complying with IMO’s Energy Efficiency Design Index 2025 standards, NOx Tier III and Marpol Annex VI SOx emission levels.
The project, which is led by Athens-based bulk carrier owner Arista Shipping, began officially in May this year.
“Project Forward aims to become a milestone for the shipping industry and in particular for owners and operators of cargo ships,” says Arista Shipping Principal Alexander P. Panagopulos. “Owners must decide within the next 5-10 years whether gas as fuel is a practical means of compliance with lower emissions standards and this project will enable all of us to understand its feasibility.”
The concept design will be based on the highly-optimized Deltamarin B.Delta design suitable for ships between 82,000 and 210,000 dwt. It will employ GTT’s membrane-type LNG tanks for fuel containment.
“Compliance with stricter environmental regulations has led owners to consider the potential of using LNG as fuel for cargo vessel newbuildings,” states Deltamarin Managing Director Mika Laurilehto. “There is a clear need to turn this potential into a proven solution for the dry bulk carriers that make up such a large proportion of the world fleet.”
The project will also address the existing dry bulk fleet by developing a modularized LNG fuel retrofit solution for bulk carriers of various sizes.
ABS will conduct concept and detail design approvals according to its rules for bulk carriers and gas-powered ships.
“ABS has gained valuable insights from real-world experience classing the world’s first deepsea ships powered by LNG,” says ABS Vice President of Global Gas Solutions Patrick Janssens. “Our work with owners, designers and shipyards on LNG as fuel and LNG-ready projects brings unique value to Project Forward in enabling the safe adoption of this new fuel type.”
Project Forward will include a number of stages, with a first time horizon of two years’ applied research and development work.
Initial research indicates that the expected emission reductions from Project Forward could be 40% for CO2, 80% for NOx and 98% for SOx.
“It is time for the shipping industry to move forward and embrace the potential of gas-fueled merchant ships,” says GTT Vice President LNG as Fuel division Jacques Danton. “At this time, we can recognize market leaders launching LNG projects now in order to be the first on the learning curve. During the ramp up phase of LNG as fuel, autonomy will be a key feature for integrated solutions as provided by membrane technology.”
For many shipowners, it could make EGR —rather than SCR (selective catalytic reduction) — the optimum means of meeting the NOX reduction requirements set by EPA Tier 4 and IMO Tier III requirements.
Developed by Alfa Laval in close cooperation with MAN Diesel & Turbo, the Aalborg EGR-HPE is a revolutionary new economizer enclosed in a pressure casing. Placed in-line ahead of the pre-scrubber sprayers in the EGR circuit, it can be used to gain a number of advantages. If connected to a conventional waste heat recovery system, for example, waste heat recovery becomes substantially more efficient – and is possible at significantly lower engine loads.
“EGR provides Tier III NOx compliance with a very compact footprint, but compliance itself is only part of the full potential,” says John Pedersen, Business Manager, Boilers, Combustion & Heaters at Alfa Laval. “Working closely with MAN Diesel & Turbo to optimize the EGR technology, we saw additional opportunities through our expertise in marine boilers. The result is the Alfa Laval Aalborg EGR-HPE economizer, which paves the way for extraordinary energy and fuel savings.”
“By moving the break point for waste heat recovery from a medium engine load down to a low load, the Aalborg EGR-HPE enables even slower steaming,” says Mr. Pedersen. “That means fuel savings that quickly pay back the economizer, offset the EGR investment and lower CO2 emissions on top of the NOx reduction.”
The source of all these benefits: the heat that would otherwise be lost during EGR. In the EGR process, around 30% of the exhaust gas is directed back into the engine, reducing the combustion temperature and thus the production of NOx. However, as only the 70% of the gas now reaches the traditional exhaust gas boiler after the turbocharger, waste heat recovery is reduced by 30%.
However, the Aalborg EGR-HPE is placed in-line before the EGR pre-scrubber spray jets that cool the exhaust gas. The economizer thus has access to much higher temperatures than traditional exhaust gas boilers. So, while the installation is light, compact and self-cleaning due to the high speed of gas flow, its application potential is enormous. This can be seen in the way it increases the efficiency of a conventional waste heat recovery system.
The Aalborg EGR-HPE is integrated with conventional waste heat recovery after the turbocharger by means of its steam drum, which is shared by the traditional exhaust gas boiler. With the output of the traditional economizer feeding into the shared drum, the Aalborg EGR-HPE produces extremely high-quality steam with a temperature of just above 400°C, bringing the waste heat recovery system to a much higher level of efficiency.
“The difference in steam quality has a direct effect on the performance of the steam turbine,” says Mr. Pedersen. “Installation factors play a role, but a substantial increase in power generation can be expected.”
Fuel savings through even slower steaming
Even more importantly, using the Aalborg EGR-HPE in an integrated system allows waste heat recovery to occur at lower main engine loads than possible with a traditional waste heat recovery system in Tier III operation. In other words, it creates the possibility for even slower steaming.
“The EGR economizer makes waste heat recovery beneficial at far lower engine loads, down to around 30%” says Mr. Pedersen. “This means that vessels can steam even slower, with huge fuel savings as a result. A vessel performing EGR and using the Aalborg EGR-HPE will be not only compliant with Tier III, but also substantially more fuel efficient.”
Proven results at sea
The savings with the Aalborg EGR-HPE are not merely theoretical.
In a project supported by the Danish Energy-Technological Development and Demonstration Program (EUDP) and developed in cooperation with Aalborg University, the EGR boiler has been rigorously tested aboard the Maersk Cardiff, a 4,500 TEU containership delivered to Maersk Line in 2013.
“As a front-runner in the pursuit of green technologies, we were keen to see what the Aalborg EGR-HPE could do,” says Ole Christensen, Senior Machinery Specialist at A.P. Moller-Maersk. “But while we were enthusiastic about the boiler’s potential, we were also somewhat uncertain as how it would handle the physical realities of EGR. The temperatures are twice as high as those of traditional waste heat recovery, and the gas pressures are far greater.”
Those concerns disappeared when the boiler was brought online with the Maersk Cardiff’s two-stroke MAN B&W 6S80ME-C9 engine in November 2014. “Not only did the boiler survive,” says Mr. Christensen, “the results we have seen during testing are very promising.”
“By introducing the EGR boiler into the NOx equation, we’ve truly changed the balance,” says Alfa Laval’s Pedersen. “Suddenly EGR is not only a means of Tier III compliance, but also a means of radically improving the vessel’s energy efficiency. And that makes it a very different sort of investment.”
The engine is the first of two 8S70ME-C8.2-GI units for delivery to VT Halter Marine, Pascagoula, MS, for installation in the two 2,400 TEU ConRo ships it is building for Crowley Maritime Corporation.
The vessels will be two of the world’s first LNG-powered ConRo ships, with container Lift-on/Lift-off (LO/LO) and vehicle Roll-on/Roll-off (RO/RO) loading. Designed to travel at speeds up to 22 knots, they will be 219.5 m long, 32.3 m wide and have a deep draft of 10 m. In addition to carrying 2,400 TEU of containers they will be able to carry nearly 400 vehicles in an enclosed Roll-on/Roll-off garage.
Crowley ordered the ME-GI engines, along with three MAN 9L28/32DF auxiliary engines for each vessel, in early-2014. The company selected the high-pressure, Diesel-cycle ME-GI engines because of their high efficiency and power concentration. The ME-GI’s ability to avoid derating, and its negligible methane slip, also contributed to its selection.
Crowley reports that the newbuildings will reduce the amount of CO2 emissions attributable to each container by approximately 38%.
The ships will meet or exceed all regulatory requirements and will have the CLEAN notation, which requires limitation of operational emissions and discharges, as well as the Green Passport, both issued by DNV GL.
The ME-GI engine
The ME-GI engine is the culmination of many years’ work, and gives shipowners and operators the option of utilizing fuel or gas depending on relative price and availability, as well as environmental considerations.
The ME-GI uses high-pressure gas injection that allows it to maintain the numerous positive attributes of MAN B&W low-speed engines that have made them the default choice of the maritime community. The ME-GI is not affected by the multiple de-ratings, fuel-quality adjustments or large methane-slip issues that have been seen with other dual-fuel solutions.
MAN Diesel & Turbo sees significant opportunities ahead for gas-fueled tonnage as fuel prices rise and exhaust emission limits tighten. Research indicates that the ME-GI engine delivers significant reductions in CO2, NOx and SOx emissions. Its negligible methane slip makes it even more environmentally friendly
An ME-LGI counterpart that uses LPG, methanol and other liquid gases is also available, and has already been ordered.
Factory Acceptance Test attendees pictured in front of the ME-GI engine at MES’s Tamano Works
Chuck Griffith, Sales Manager, MAN Diesel & Turbo, North America, said: “This certification is a significant step in our four-stroke, marine-engine strategy for the U.S. market. The engine family has been certified US EPA Tier 2 for Category 3 engines and builds the foundation for us to introduce our US EPA Tier 3 for Category 3 product in 2016. This will allow U.S. customers to benefit from the high power output and low fuel-consumption of our medium-speed, common-rail engines.”
EPA Tier 3 is currently the final emissions tier for Category 3 (≥ 30L/cyl displacement) engines, and is similar to EPA Tier 4 for Category 1 and 2 (< 30 L/cyl displacement) engines.
MAN Diesel & Turbo initiated the EPA certification process in response to demand from the American fishing industry. The company has already received several U.S. orders for the engine, including one for an MAN 8L32/44CR engine to power a newbuilding trawler for Fishermen’s Finest. The order was a breakthrough for the CR engine in the important, U.S. domestic-fishing segment (see earlier story).
Since being introduced in Europe eight years ago, the CR engines have consistently proven their reliability and durability within the fishing industry and are known for their excellent fuel efficiency and low operating costs. They are among the most technologically advanced in MAN Diesel & Turbo’s common-rail engines are its portfolio with a segment-leading SFOC that significantly lowers emissions of soot and NOx over the complete operating range.
The MAN 32/44CR is characterized by:
MAN 32/44CR engines are suitable for a variety of applications including fishing, ATBs (Articulated Tug Barges), anchor handlers, offshore construction vessels, dredges and drill ships.
The EPA certification: (top) 2015 Model Year, Certificate of Conformity with the Clean Air Act; (bottom) Office of Transportation and Air Quality, Engine International Air Pollution Prevention Certificate
AUGUST 11, 2015—Keppel Offshore & Marine Ltd (Keppel O&M)’s wholly owned subsidiary Keppel Shipyard Ltd has secured a Floating Production Storage and Offloading (FPSO) conversion contract as well as three repair, upgrade
AUGUST 5, 2015 – Totem Ocean Trailer Express has signed a contract with Keppel Offshore & Marine Ltd’s Keppel Shipyard to carry out the conversion of the Midnight Sun to dual fuel
AUGUST 4, 2015 — The start of production of Estonian operator Tallink’s new generation LNG fueled fast ferry for the Tallinn, Estonia-Helsinki, Finland, route began today at the Meyer Turku shipyard in