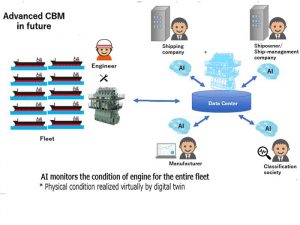
NYK starts research aimed at manned autonomous vessels
Japan’s NYK Group has reached joint research agreements aimed at developing advanced condition-based maintenance (CBM) management processes for ship machinery, and has started verification of data during actual ship operations. Machinery plant