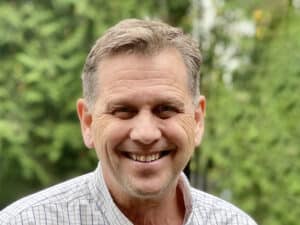
Kobe Steel in crank throw strength breakthrough
Written by Nick Blenkey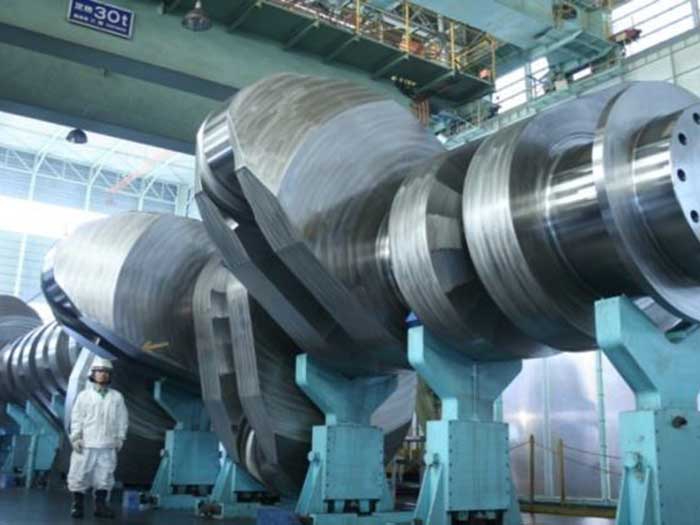
OCTOBER 13, 2016 — With ships being being equipped with larger propellers that rotate at lower speeds, engine strokes have become longer and therefore crank throws — a key component in marine crankshafts — are becoming longer and heavier.
To lighten crank throws and improve reliability, Kobe Steel has been working to improve fatigue strength and has now been given special approval by classification society ClassNK to use a K factor of 1.05 in calculating the design fatigue strength of crank throws, in comparison to a standard value of 1.0, providing a margin that can contribute to lighter and more compact forgings..
Kobe Steel has succeeded in applying a die-forging method that increases fatigue strength by 20 percent, compared with conventional forging, to manufacture ultra-large crank throws with cylinder diameters of 80 cm or more, used with engines for the world’s largest class of containerships and tankers.
The die-forging method enables Kobe Steel to supply high-strength, lighter weight components with an approved 5-percent margin in fatigue strength in the design phase. Having already received the same Class NK approval for small and medium-sized throws, Kobe Steel is now the only company in the world to receive certification for the full range of throws, ranging from small to large, for use with two-stroke engines.
Leave a Reply
You must be logged in to post a comment.