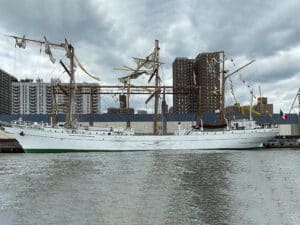
BEATING COVID-19: GOING REMOTE
Written by Nick Blenkey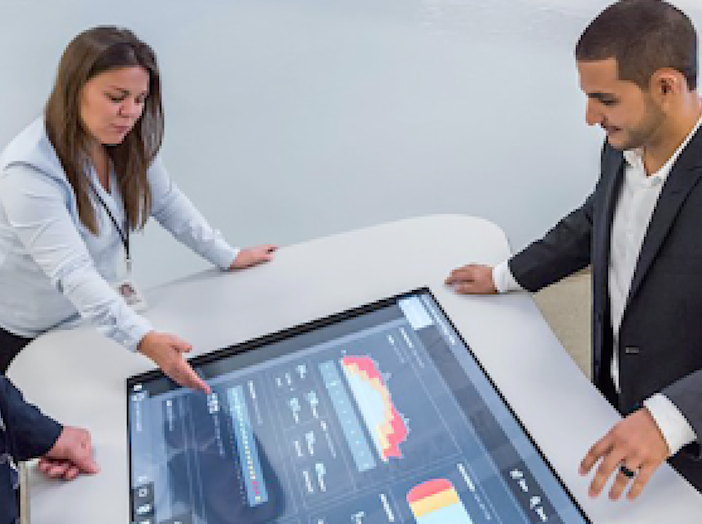
ABB speciaists offer maintenance services 24-7 from eight ABB Ability Collaborative Operations Centers.
When the De Hoop Shipyard in Lobith, Netherlands, took its latest newbuild on sea trials off Rotterdam in May, it notched up an unintended “world’s first.” The ship that the yard was putting through its paces was Silverseas Cruises’ ultra luxurious 100-passenger, all-suite expedition ship Silver Origin, which will operate in the Galapagos.
Because of COVID-19 restrictions, the sea trials were very different from normal. One challenge in particular, says Fre Drenth, the director of De Hoop Shipyard, was a potentially project-halting issue.
“Navis, a St. Petersburg-based company who produced the computer software for Silver Origin’s propulsion and steering installation, could not reach the ship,” says Drenth. “Navis’ engineers were required for the commission and tuning of the software, which is a time-consuming job and can take between four and eight hours. Nevertheless, we managed to devise a solution, which, to my knowledge, had never been tested during a sea trial and would push the boundaries of engineering.”
It was decided that Navis would tune the ship’s dynamic positioning system remotely from the company’s office in St. Petersburg, Russia—over 1,800 kilometers away. A fast internet connection was established on the vessel and communications were tested before the sea trial and all went well. Using just a headset and a built-in camera, contact with the vessel was made.
“Silver Origin’s dynamic positioning system controls the ship’s bow thrusters and azimuth thrusters. As borders with Finland were closed and a required engineer couldn’t attend the sea trial, a stand-in engineer was appointed to commission the thrusters, working closely with the engineer in St. Petersburg,” says Fre Drenth. “After testing of the propulsion installation, we gave the vessel to the control of the engineer in St. Petersburg. This went very well, in part due to the fact that this engineer had a great deal of experience.
“The tuning was successful and took no longer than normal. Our sea trial demonstrated, for the first time ever, that it is possible to tune dynamic positioning systems remotely. It could save companies time and money in the future.”
Though the remote operation of Silversea Origins’ DP system is a dramatic example of how the need to live within the constraints imposed by coronavirus restrictions is giving an added impetus to a marine industry trend that had already been gathering pace.
Connectivity is Key
Maritime VSAT connectivity reached an all-time high of 28,200 connected vessels at the end of 2019, according to the latest data from Euroconsult, with number of terminals increasing by 17.5% year over year, and VSAT services revenue growing by 11% to approach $1.3 billion. Helping push that growth have been factors, such as the cruise industry’s need to satisfy passenger expectations and crew welfare benefits, but equally important has been the industry’s growing awareness that a more connected ship is a more efficient ship in a myriad of ways. As it happens, Euroconsult thinks that the growth in maritime VSAT adoption will slow as a result of the pandemic, notably because of its impact on cruising. Nonetheless, Pacôme Révillon, CEO of Euroconsult, says, “in light of technology advances and the appetite for applications and bandwidth, we expect the industry to return to growth in two years’ time.”
The sophisticated technology now coming on board ship requires equally sophisticated back up. Even before the pandemic, we have seen companies developing approaches that use technologies such as “smart glasses” to, essentially, virtually put a factory technician aboard a ship when needed. And an increasing number of ship operators have been signing up with companies such as MAN Energy Solutions, Wärtsilä, Kongsberg, and ABB for advanced maintenance contracts that put a heavy emphasis on remote monitoring of shipboard systems from shoreside centers.
These remote maintenance capabilities are proving particularly valuable in the current situation, and ABB has increased the remote availability of technical service teams to help crews from shore. With a network of 800 service engineers in 40 locations worldwide, ABB is assisting customers on site from units closest to the vessel’s operation. When onsite support is not feasible due to travel restrictions, ABB’s pool of experienced local service engineers has been made available to help crews remotely, with additional technical guidance from its eight ABB Ability Collaborative Operations Centers situated around the globe.
Remote Compliance
A major issue that has put operators to the test during the pandemic has been the need for ships to comply with statutory survey requirements by given due dates. While flag states and classification societies operating on their behalf can give operators some leeway here, obviously simply extending due dates is not a desirable long-term answer.
The U.S. Coast Guard issued a Marine Safety Information Bulletin (MSIB 09-20) in March explaining the measures it is adopting during the COVID-19 outbreak with regard to vessel inspections, exams and documentation.
The bulletin notes that “the uninterrupted flow of commerce on our Marine Transportation System (MTS) is critical to both National Security and National economic well-being” and says that, during the national emergency for COVID-19, it is paramount that the Coast Guard safeguard the continued operation of the MTS to ensure our domestic supply chain continues uninterrupted.
“Commercial vessel compliance activities should, to the extent possible, continue so as to safeguard the MTS and prevent an undue backlog from causing future delays,” says the bulletin. “To facilitate the safe flow of commerce, the Coast Guard will liberally use remote inspection techniques to verify vessel compliance and, if needed, defer inspections.”
Coast Guard Rear Adm. Richard Timme, Assistant Commandant for Prevention Policy, referenced that same MSIB in responding to a request from the American Waterways Operators asking that in-person Subchapter M inspection activities be suspended for a minimum of 30 days, for the mutual protection of both towing vessel crewmembers and Coast Guard inspectors during the COVID-19 outbreak.
One example of the use of innovative inspection techniques in the offshore services sector came when ABS used Edison Chouest Offshore’s Remote Monitoring Center (RMC), to perform the first-ever remote Failure Mode Effect Analysis (FMEA) as part of completing the special survey of the machinery of Chouest’s Cat Island platform supply vessel.
ABS conducts special surveys every five years. During the special survey, a full FMEA trial is carried out to evaluate processes and identify how they may fail and to assess the relative impact of different failures in order to identify the parts of the process that are most in need of change.
Located at Chouest’s corporate headquarters in Cut Off, La., the RMC gives the company the ability to remotely monitor vessel and cargo movement throughout the fleet. The RMC was created through collaboration between several Chouest affiliates and allows for real-time monitoring of vessel systems. Chouest’s 312 series of platform supply vessels and newer vessels within its fleet are remotely monitored 24/7, with over 4,000 data points per vessel. The entire Chouest fleet as a whole monitors around 300,000 data points every 10 seconds. This information is used to highlight concerns, prevent failures and eliminate downtime.
Chouest has one of the most advanced PSV fleets in the world, capable of providing remote troubleshooting and inspections. This reduces the need for technicians to travel to vessels. In today’s situation, this enables the social distancing crucial to limiting the spread of COVID-19.
International Operations
The U.S. Coast Guard is not the only flag state authority looking to use innovative techniques to ensure that statutory inspections continue to be performed during the pandemic.
The Liberian Registry, for example, is adjusting to the disruptions caused by COVID-19 by leveraging its use of technology and modern communication and has implemented remote Annual Safety Inspections (ASI) aboard its ships.
It successfully completed its first remote ASI back in March. Liberia’s qualified inspection team was able to liaise with the ship’s crew remotely via web-based video communication and review the ASI checklist, check documents, check safety equipment, review drills, and inspect the condition of the vessels and functionality of the safety equipment; all without putting the health of crew and inspector at risk due to possible coronavirus exposure.
While allowing the flexibility to extend surveys, drydockings, credentials, and other certificates, the registry says that it understands the important need, and duty of the flag state, to maintain effective oversight over its fleet and ensure the seaworthiness and safety of its vessels and seafarers, and compliance with international conventions.
Accordingly, much effort was put into coming up with a comprehensive remote inspection checklist and procedure.
“I have to applaud our very experienced and knowledgeable Inspections team for their very practical and real-world solution, which ensures that the flag state is able to carry out its obligation of safety oversight of its fleet in a way that is not burdensome to the vessels, nor puts the health of the crew and inspectors in jeopardy,” says Alfonso Castillero, chief operating officer of the Liberian International Ship and Corporate Registry.
Class Accelerates Push to Remote Surveys
Even before the outbreak of COVID-19, leading classification societies were promoting the use of remote surveys.
ABS says it is now able to conduct almost all classification annual surveys remotely on eligible vessels. Back in April, the society launched 10 additional remote survey options, bringing to 28 the total of surveys and audits that it can deliver remotely.
“The industry is telling us they want our services delivered remotely, particularly in the current challenging environment, and I am proud that we are providing the most comprehensive remote services portfolio in the industry,” said Joe Riva, ABS vice president and chief surveyor. “We are delivering the next generation of classification today through surveys conducted anywhere in the world at any time, without interrupting operations for surveyor attendance.”
ABS is not alone in seeing a surge in demand for these services. Back in March, DNV GL reported that it had undertaken some 15,000 remote surveys and inspections since their launch in October 2018.
“In these challenging times we are seeing the benefits of the full scope of digitalization initiatives that we have been building up over the past few years,” said Knut Ørbeck-Nilssen, CEO, DNV GL – Maritime. “The use of remote surveys has meant that we have been able to limit disruptions to customer operations resulting from travel bans or quarantines involving our surveyors. Ship operators are able to receive immediately updated and verified electronic certificates, which make their business dealing with class, authorities and vendors much more efficient.”
Customers are able to request remote DNV GL surveys around the clock, independent of port calls, location, and time zone. Remote surveys are being offered both through DNV GL’s global DATE (Direct Access to Technical Experts) service, delivered through expert teams from Høvik, Singapore, Hamburg, Houston and Piraeus, and via regional offices.
Lloyd’s Register (LR) says it has been utilizing remote techniques “for years,” with one in five of the 30,000 surveys it completes around the world each year already being done without attending the vessel or asset, and with the proportion growing,
“The restrictions on movement caused by COVID-19 turned remote surveys from possibility to necessity for many of our clients,” says LR, noting that In March 2020, the number of complex remote surveys it performed increased by 25%.
ClassNK says that in response to the spread of COVID-19, it has been making every effort to provide support to all those who may miss due dates for surveys/audits due to force majeure. “Specifically,” says the society, “we are offering applicable alternative measures such as the application of remote surveys and postponement of surveys etc., subject to approval of the flag state administration.”
No Going Back?
Training, too, is one area where remote connectivity is paying dividends. One recent example comes from the world of superyachts. When the 93.25-meter Mayan Queen IV was confined to port in Antibes, plans for the crew to receive classroom-based training on Konsberg’s K-Chief 700 automation system were thwarted. However, Kongsberg was able to conduct the training online—with one of the students even further away in Thailand. During the course, each student was given access to a virtual machine emulating a K-Chief 700 operator station, giving hands-on experience and allowing them to carry out practical exercises, while a Kongsberg instructor delivered presentations and targeted advice via the Zoom videoconferencing platform.
“I was slightly skeptical about how successful a remote course would be, but the outcome was excellent and had several advantages over a classroom course,” said Chief Engineer Tim Webster. “Firstly, we have been trying to book the course for over a year now, but as our staff live in different global locations and have varying leave patterns it has been difficult to arrange for all of us to attend a course at Kongsberg. By doing it onboard during this lockdown period, we could have the full team involved whilst also bringing in Colin our other ETO remotely who was on leave in Thailand.
“The other benefit of running the course remotely and onboard,” he continued, “was that after every session the onboard team could go directly to our live system to try out our new knowledge and provide feedback to the instructors on various parameters on our system.”
One takeaway from this is that, in a number of regards, the remote, virtual way of doing things is likely to prove more effective than the traditional one. Likely, in several key areas of maritime operations, there will be no going back.