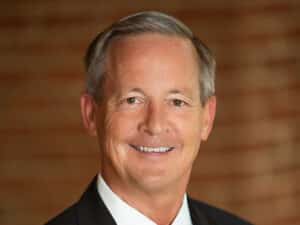
Op-Ed: Marine coatings systems explained
Written by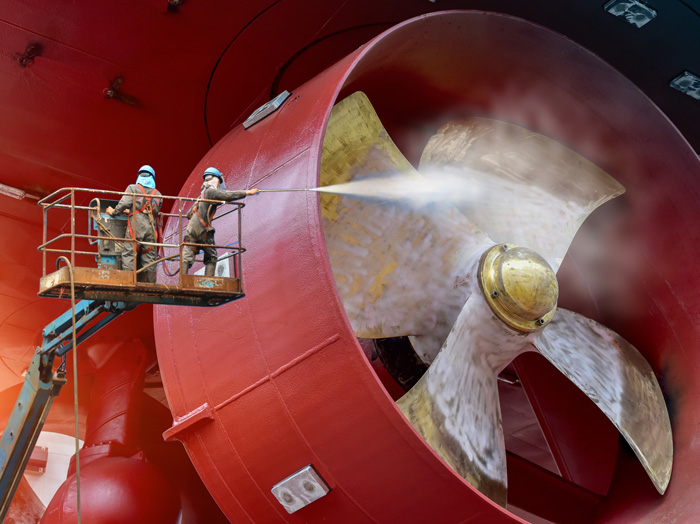
Credit: Shutterstock
By Thomas O’Shaughnessy, owner of Industrial Paint and Protection magazine
It may sound dramatic, but it’s true: corrosion is attacking your ship from the first second it goes into service, to the day it’s retired.
What causes corrosion on a ship? That’s a long list, and it includes everything from hazardous cargoes like hydrochloric acid, to wicked sewage-borne microbes, to simple morning dew.
Luckily, there’s a simple way to protect your ship. Marine coatings can radically extend the lifespan of your vessel, and it’s big business—the marine coating industry was a $4 billion market in 2020, and is expected to grow nearly 6% by 2027.
The only catch? There are thousands of coatings to choose from. Read on to find out what marine coating works best for each part of a ship, and why.
THE DECK
The deck takes a ton of punishment from routine traffic. On top of that, it’s exposed to seawater and salty air, both of which are corrosive. And at night, salt-laden dew condenses on every exposed surface; when this is heated by the sun, corrosion kicks into overdrive.
For a problem like this, you need a multi-step solution. We suggest using a high-grade coatings system that includes a primer, an epoxy midcoat, and a recoatable topcoat.
The three coatings work together: the primer helps the coatings system adhere to the metal deck, the high solids epoxy midcoat gives great corrosion protection, and the polyurethane topcoat protects the epoxy midcoat from UV light, which can cause epoxies to fade or chalk.
For additional protection, you could also consider a glass-fiber reinforced epoxy, which can stand up to the heaviest impacts. And since epoxies can be slippery when wet decks that see a lot of traffic should always include a non-skid coating additive.
CARGO AREAS
The best coating for your cargo area is going to depend on what cargo you’re transporting, and your turnaround time.
Bimodal epoxy is extremely versatile and offers very low absorption—however, it requires a long curing period after application. Phenolic epoxy is a little quicker to apply, and is one of the most versatile epoxies, but is very sensitive to air temperature at the time of application, and can fail if conditions aren’t right. For petroleum products, a pure 100% solids epoxy coating is the best option.
The best way to select the right coating for your cargo area is to consult with a coatings expert before you make your choice.
THE HULL
While the other coatings on this list are merely protective, hull coatings have a dual purpose; to protect the hull and to keep it smooth and frictionless.
For the part of the ship that’s underwater, you’ll want a good antifouling coating to keep friction to a minimum. Increased friction from marine organisms on the hull may not seem like much, but one study found that if the world’s cargo ships could reduce drag by only 10%, they’d save $4.7 billion a year in fuel costs.
There are two main types of antifouling coatings. Biocidal coatings poison marine organisms, and foul release coatings create a slippery surface that organisms can’t attach to.
Which is better for your situation? Well, foul release coatings increase drag, so they’re best used on stationary assets. For a mobile ship, biocidal coatings make more sense.
For the part of the hull above the water, you’ll want a nice, tough boot-topping. Ships can take a bit of punishment during docking, so you need an extremely durable high-performance coating like a multiple-layer high solids epoxy.
A zinc-rich primer with two epoxy coatings on top is a good starting point; if you know your hull is going to take a ton of dings and scuffs, you could increase the epoxy layers.
SUPERSTRUCTURE
The superstructure has a lot of area, as well as a lot of nooks and crannies. A standard multi-layer high solids coating system can give you great protection, but it’s expensive, and laborious to apply (and reapply).
Many people prefer alkyd or acrylic coating systems here, since they’re so much easier to apply. They do fade much faster than a high solids coating, so your decision here is going to depend on your budget and schedule. You’ll probably also want to opt for an anti-rust finish.
TANK COATINGS
The ballast tanks take a ton of punishment because they’re constantly being filled with and emptied of corrosive seawater.
Any coating you use in your ballast tanks have to be compliant with Safety of Life at Sea (SOLA) convention provisions; the industry standard is a coal-tar or surface-tolerant epoxy, both of which meet SOLA standards. Additional epoxy coatings can extend your protection.