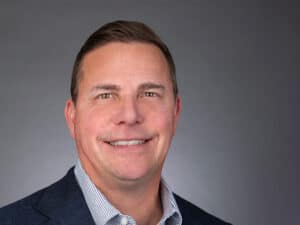
Op-Ed: Engineering insights when building a trawler
Written by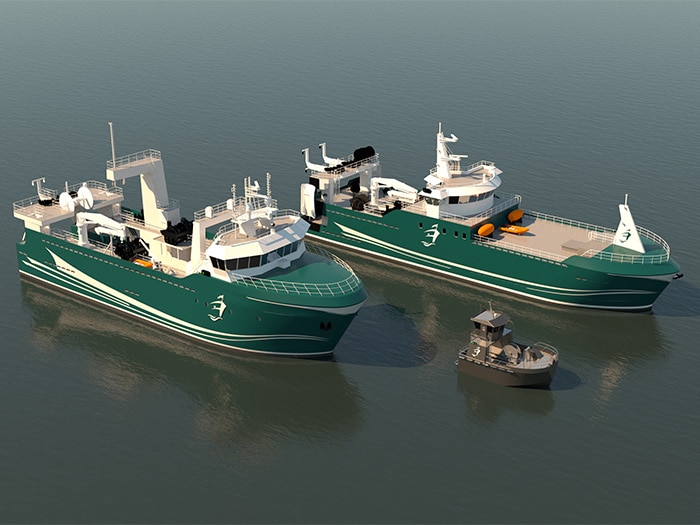
While naval architects, shipyards and equipment suppliers saw a boom in their immediate future, the renewal of the fishing fleet has barely begun. (Credit: EBDG)
By Jim Towers, PE Principal in Charge, Elliott Bay Design Group
Constructing a new factory trawler fishing vessel in the United States is not an undertaking for the faint of heart. Thinking back to an article written about 10 years ago, industry scholars predicted a boom in shipbuilding to replace the Alaskan fishing fleet. While naval architects, shipyards and equipment suppliers saw a boom in their immediate future, the renewal of the fishing fleet has barely begun. In fact, less than 5% of the fishing trawlers in the Alaskan fishery have been replaced.
Only four significant new vessel construction projects have been completed over this time frame:
- The refrigerated seawater (RSW) catcher fleet has seen one large conversion join the ranks.
- The Amendment 80 fleet has seen three new construction vessels, along with one sponsoning and one conversion project.
- The American Fisheries Act (AFA) fleet has seen one new-build project completed.
Vessels in all three fleets have seen significant upgrades in this time, but the underlying hulls still date from the 1980s and 90s with some going back as far as the 1960s and ’70s.
Seattle-headquartered Elliott Bay Design Group (EBDG) is committed to supporting the fishing fleet, diligently assessing the optimal path ahead—whether it involves fleet replacement or ongoing investments in aging hulls.
One thing is true, EBDG is noticing operators across the Alaskan fishery continue to struggle with vessels that require escalating financial resources, and lack of capacity to integrate modern technology, advanced machinery, and cutting-edge operational equipment.
These challenges are impacting profits in crucial areas such as crew costs, catch quantities, and overall vessel performance. Finding design solutions for operators has been promising over the last decade; however, owners are hesitant to embark on the risky and expensive uncharted journey of building a new fishing vessel. This predicament raises a pivotal question: How can the fishing fleet surmount these financial obstacles and make a new-build fishing vessel a reality?
Owning and operating a Jones Act-compliant fishing trawler in the U.S. fishery is a challenge. Foreign competition can build in low-cost countries allowing competitor fleets to be replaced on a 15-to-25-year cycle. In the U.S., the CapEx/OpEx equation is completely different. The cost of new construction skews the financial picture significantly across the entire U.S. commercial marine industry. Hulls built in the U.S. often have operating lives of up to 50 or 60 years and go through one or more midlife refits. This is well illustrated by the age of the various ferry fleets in the U.S. European trawlers, however, are designed and built for much shorter operating lives, and usually sold in countries with much different economies before reaching 20 years old.
The U.S. fishing fleet is forced to upgrade or maintain their fleet differently. Many of the original trawl fleet took the conversion route to reduce costs in the 1980s and ’90s. These hulls came from many sectors of the marine industry including tankers and cargo ships, primarily from the oil fields in the Gulf of Mexico. Some were conversions using very little of the original ship to allow the work to be done overseas. While the oil patch continues its cycles of boom and bust, the vessels have changed radically in the last 30 years.
The recent downturn in the oil business has not resulted in cheap hulls for the fishing fleet. The current crop of offshore supply vessels are technologically advanced boats which are not well suited for easy conversion to fishing vessels. Numerous fishing companies have looked at the offshore supply vessel fleet as candidate hulls but have not moved forward with conversion. This time around conversion does not appear to be a likely avenue to reduce cost.
Given that the current fishing fleet is around 35 years old for the catcher processors and even older for the RSW fleet, it is likely that many vessels will be repowered and refit to extend their lives to the 50-60 age. However, many of the smaller Amendment 80 boats are reaching the end of their economic life. In part because they have been overtaken by technological changes in the fishery, but also the cost of refurbishment is becoming prohibitive. The size of today’s trawlers make it difficult to accommodate technology changes such as automated plate freezers and palletization. The older Amendment 80 fleet has the most to gain from earlier new construction.
There is also the need to embrace alternative fuels. If decarbonization is to occur by 2050, vessels built today will need to be capable of dealing with the storage of different fuels. While there are clear routes forward in many sectors of the marine industry this is not the case for the fishing industry. Hybridization and peak shaving will have limited applicability in the fishing fleet. Alternative fuel engines such as methanol or ammonia show considerable promise but are not yet mature technologies for the types of engines typically used in the trawler fleet.
Methanol-fueled engines are seeing wide acceptance in container ship fleets and owners are working to develop a worldwide green methanol supply chain. The challenge of both ammonia and methanol is the energy density is less than half that of diesel fuel, requiring much greater tank space. Storage tanks must be designed differently from current double bottoms and wing tanks. Presently there is no clear way forward for the fishing fleet to adopt decarbonization. New construction is a solution, given operators and designers are open to non-traditional space and weight options to allow for alternative fuels.
So far, there has been a lot of doom and gloom about the practicality of modernizing the U.S. fishing fleet. Nonetheless, by embracing creative solutions and exploring unconventional ideas there are possible ways to reduce the cost of new construction. Designing a trawler is a complex task especially when one considers many systems that go into the catcher processor. One common issue revolves around the amount of detail available at the time a contract is signed. The shipyard can only be expected to price work based on the information they have.
Often there are only a few details available from the factory installation or fishing deck when the shipyard contract is executed. The more detail that can be provided to the yard during the bidding process the better the chance of the outcome not running over budget. Dealing with the meticulous details upfront adds substantially to the design phase of the project. Time must be allowed to sufficiently mature the design to reduce the yard’s risk. Realistically, a newbuild schedule spans over five plus years for the complete design build cycle. A trawler project starting in 2024 is not going to be ready for service until at least 2029, if all goes according to plan. Significant upfront engineering can result in more accurate pricing and less change orders resulting in a cheaper boat.
There are currently only a small number of yards in the U.S. with experience building catcher processors in the last 25 years. This limited pool of experience (yards with prior construction) limits competition. It is a challenging task for new yards to enter the market and there is a risk for the owner who contracts with an inexperienced company.
One unconventional option recently explored was the idea of a group of companies using a common hull, with only the factory being customized to the individual owners’ requirements. This had the potential to substantially reduce construction costs. Both the RSW trawler and the longliner faced setbacks in achieving success, partly because of sticker price and variations in equipment and machinery preferences. Nevertheless, this could reduce costs by as much as 10% for a run of five vessels: making a revisit to this concept worthwhile. However, it’s important to note that collaboration between partnering owners would require a willingness by each to make compromises.
Lastly, crewing continues to be challenging. As with most marine sectors, the fishing industry has experienced difficulty finding trained and qualified crew members. New construction can lead to reduced crew numbers from both fleet rationalization, new technologies and automation.
As you consider your future fleet options, here are a few final engineering insights to keep in mind:
- While fleet renewal for the AFA and RSW fleets may still be in the future, there are good, solid reasons for the Amendment 80 fleet to look at new construction sooner.
- Ensure that the design is mature when the contract is signed. Change orders are expensive.
- Have an owners’ team in the yard that has the necessary skills to manage the project on both a technical and commercial basis.
- Consider the use of a multi-vessel contract with other owners. The use of identical hulls can save significantly on production engineering costs and shipyard learning curve.
- Keep an open mind about options and possibilities.
- Remember the old adage “Quality, Price, Delivery- select any two.”