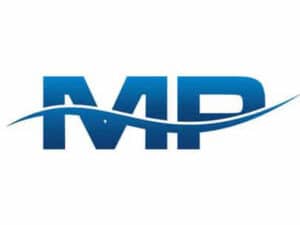
Op-Ed: Electrostatic spray reduces overspray in shipyards
Written by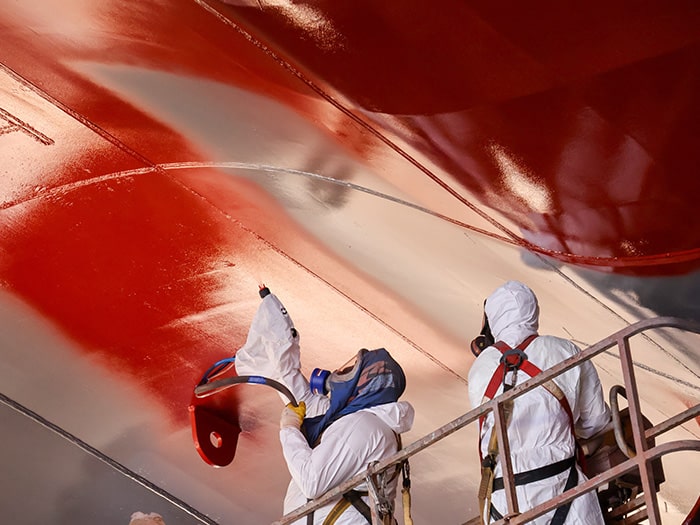
By Joanna van Helmond, PPG product development director, marine fouling control, marine and protective coatings
Increasing pressure for more sustainable operations and tighter margins in the maritime industry encourages shipowners and yards to explore ways to improve efficiency and reduce waste. One technique gaining attention is electrostatic coating application.
This method offers a more controlled and precise way to apply hull coatings compared to traditional airless spraying.
How Electrostatic Spray Works
Electrostatic spraying relies on a simple concept: opposites attract. Applicators use an electrostatic spray gun to charge paint particles, which are drawn to the grounded steel hull like a magnet. Electrostatic spraying requires lower paint pressure when compared to traditional airless spraying. This improves transfer efficiency as particles pass more slowly through the charging field at the gun tip. The process also introduces air at the gun tip, enabling finer atomization, creating smaller droplets which are easier to charge and therefore move efficiently toward the substrate.
This results in a more uniform paint layer and an ultra-smooth surface finish. That level of consistency is especially valuable for low-friction coatings, where surface smoothness proves critical to reducing underwater drag.
Where It Works Best
Not every hull coating can be applied using electrostatic spraying. Conventional fouling control coatings often lack the properties needed to hold a charge or flow evenly under electrostatic conditions. In contrast, formulations developed specifically for this method can distribute evenly across grounded steel and build a smooth, durable film.
For instance, both PPG NEXEON antifouling and PPG SIGMAGLIDE fouling release coatings can be sprayed electrostatically. These coatings allow applicators to achieve uniform thickness, strong adhesion and consistent performance with less material and effort.
Performance in the Field
In a recent drydocking, EDR shipyard in Antwerp, Belgium, used electrostatic spraying to apply a fouling release coating to a Stena Line RoRo passenger vessel. During this job, the yard reported a 40% reduction in overspray compared to conventional airless spray methods. This improvement came from the controlled spray pattern and the precision of the coating’s attraction to the grounded hull.
Result? Fewer stray particles reduced cleanup time, cut material waste and improved safety conditions for the applicators. The team also spent less time masking the ship’s surfaces before spraying, streamlining the overall workflow in the dry dock.
Environmental and Workplace Impact
Electrostatic coating application offers benefits for shipyards seeking to enhance both environmental performance and operational efficiency. By increasing transfer efficiency and minimizing overspray, the technique significantly reduces airborne paint particulates to create a cleaner workspace and improve safety for application crews.
It also shortens the time and resources needed for ventilation and cleanup after spraying. In the cruise segment, for example, its precision reduces overspray near accommodation areas, cutting down the need for masking and minimizing cleanup. These efficiencies can translate into shorter turnaround times and a cleaner worksite. Shipyards benefit from safer conditions for workers, reduced environmental impact and smoother operations without needing to invest in new infrastructure.
Adoption and Training
Electrostatic application of marine coatings is being adopted by shipyards across Europe, Asia and the Middle East, particularly for routine hull maintenance. Application crews, especially those with experience in airless spraying, typically transition smoothly with targeted training. Recent investments by paint and coatings companies in equipment and technical support have helped more yards integrate electrostatic spraying into their workflows.
While shipyards handle the application, shipowners and operators often drive adoption. They include electrostatic-compatible hull coatings in their drydock specifications and align those choices with sustainability goals.
What Comes Next
Techniques like electrostatic application stand out as the marine industry works toward more sustainable operations. The method provides measurable gains without disrupting yard operations or requiring major infrastructure changes.
Shipyards and operators who want to control waste, improve coating quality and support sustainability goals should consider electrostatic application as part of their broader strategy. When applied correctly with compatible coatings, it offers immediate returns in performance, labor efficiency and environmental impact.
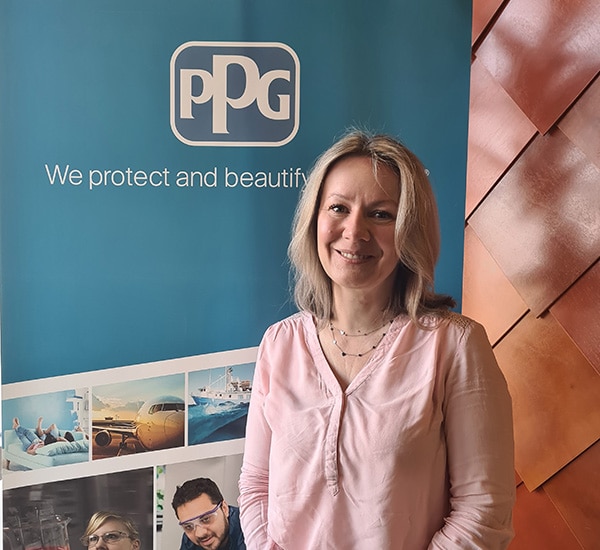
About the Author
Joanna van Helmond is PPG Product Development Director for Marine and Protective Coatings. She brings more than 20 years of experience in fouling control development and strategy and sustainable coating technologies within the maritime industry. She focuses on solutions that support vessel efficiency, regulatory compliance and environmental performance.