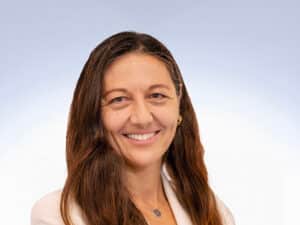
Q&A: 10 Minutes with Siemens Energy’s Luke Briant
Written by Heather Ervin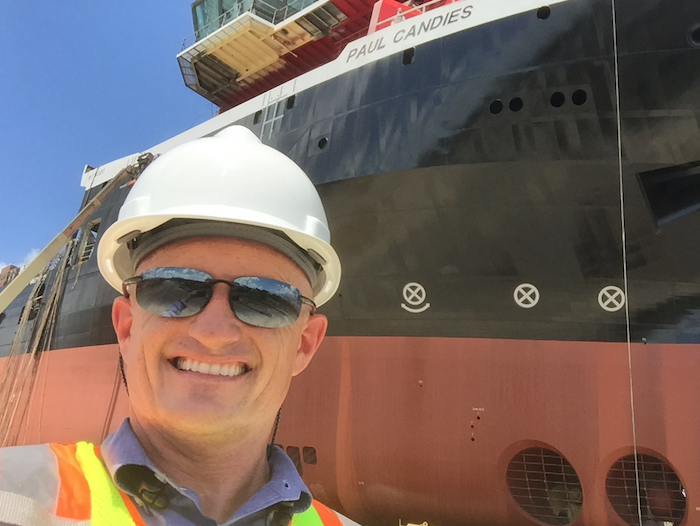
Luke Briant of Siemens Energy gives us the scoop on what the company has going on in maritime.
[Sponsored Content]: Siemens Energy Inc. is one of the world’s leading energy technology companies. The company works with its customers and partners on energy systems for the future, thus supporting the transition to a more sustainable world.
As a gold sponsor of Marine Log’s FERRIES 2021 conference, which took place November 9 – 10, we talked to Luke Briant, the head of Marine Solutions Americas for Siemens Energy Inc. about diesel electric propulsion systems, batteries, crew training, and more.
Marine Log (ML): Can you go into some detail on DEP? First, what is it and why is it important?
Luke Briant (LB): Diesel electric propulsion (DEP) is a versatile, redundant power and propulsion system which incorporates diesel-electric technology adaptable to vessels of many sizes. A diesel-electric propulsion system has multiple diesel engines, which each drive an electric generator, providing the electric power that energizes Variable Frequency Drives (VFD’s), which drive variable speed electric motors connected to the ships propellers, as well as auxiliary electrical systems which support the hotel and auxiliary electrical loads on the ship.
Depending on electrical power demand, not all diesel generators have to be operating at all times. This enables overall less fuel consumption compared to a direct drive diesel mechanical propulsion system.
However, conventional diesel electric propulsion systems which run diesel engines at constant speed with variable load, require 6 to 10% more primary power than diesel-mechanical systems.
The losses are due to the additional system components, i.e. generators, switchboards, transformers, cables, converters (VFD) and motors etc.
Diesel electric propulsion systems have higher weight compared to diesel-mechanical systems and the overall system has a higher investment cost (CAPEX) compared to diesel mechanical systems. Diesel electric propulsion is only normally viable if the engines are used at their most effective operating point, and there is less total installed power through cross utilization. Mechanical drives are most efficient when the engine is at its most efficient operating point, which is normally between 70 to 85% MCR (Maximum Continues Rating).
As we move through the 21st century the design of ships continues to change and evolve as do the increasing needs for vessel operators. As a result, DEP and hybrid DEP systems are becoming more important in the marine vessel market. Vessels with propulsion systems which have higher fuel efficiency in all operational stages will be favored and have more potential for growth.
Requirements for reliability, redundancy, maneuverability, less maintenance with reduced cost, vibration and noise reduction are becoming more rigorous. As a result, operators and owners are consequently focusing more and more on ships that provide a smaller environment risk as well as offering creature comforts. The reduction in fuel consumption and environmental emission from diesel electric propulsion compared to conventional mechanical propulsion is significant for vessels with a diversified operational profile. Savings of 30-40% in fuel consumption annually has been reported from ship owners.
In 2012, Siemens Energy, Marine Solutions was the first company in the world to introduce the next generation of DEP technology, called SiShip BlueDrive PLUSC™.
Siemens Energy has over many years created a wide portfolio and extensive competence within the field of power electronics and propulsion systems. By changing the conventional DEP propulsion system configuration and implementing a total new control philosophy, the ultracompact SiShip BlueDrive PLUSC™ system was created. With this system a whole new set of possibilities and advantages are now available compared to conventional DEP systems.
Main Benefits
• Low emission of greenhouse gases. (NOX, SOX and Methane);
• Low fuel consumption (20-35% less than a conventional DEP system);
• Low investment cost compared to gas/dual fuel systems;
• Makes full utilization of SCR systems and reduced NOX emissions possible;
• Reduced maintenance cost on diesel engines;
• Increased service life of diesel engines, especially for high speed engines;
• Reduced space, volume and weight of the electrical system (30- 40% less space and Weight compared to conventional DEP systems;
• Increased overall efficiency of the electric system;
• Clean power supply to all auxiliary consumers; and
• No rectifier transformers.
The Siemens Energy Technology utilizes variable speed (VS) operated diesel engines with variable load. With the SiShip BlueDrive PLUSC™ electric propulsion system individual speed control of each engine over the whole engine speed range is possible, providing power for full diesel electric vessels independent of synchronous speed. The control system dynamically sets the speed according to optimal operational point of the engine.
In addition to Variable Speed DEP, like Siemen Energy’s SiShip BlueDrive PLUSC™ technology, Siemen Energy has also developed safe reliable ESS technology called the SiShip Blue Vault™ which adds additional fuel savings through added peak shaving, generator bridging and all electric operation. This in turn increases overall fault ride through capability and safety, all whilst reducing the vessels overall carbon footprint.
ML: What issues of onboard space are there for things that get added in, such as batteries?
LB: Energy Storage Systems (ESS) add significant advantages to vessel systems based on a number of factors including but not limited to reliability, redundancy, efficiency and availability. With these advantages comes additional requirements to support the technology. Depending on the ESS being implemented, auxiliary power, sub systems, cooling systems, monitoring and fire suppression all have to be taken into account. Classification societies and USCG requirements also drive the additional support systems and safety measures required.
ML: What crew training will be needed?
LB: Crew Training is required for both DEP vessels, hybrid or all electric vessel systems. From a vessel operations perspective the ships crew will need additional marine operations and System technical training to be able to operate the vessel safely and efficiently.
Siemens Energy provides both hands on (on the job), classroom and remote training programs as needed and preferred by our customers.
ML: What hurdles did you overcome on the WSF project specifically, and how did Siemens Energy overcome those challenges?
LB: The main challengers Siemens Energy had to overcome with our WSF Jumbo Mark II Hybridization project was mainly developing the first of its kind charging arm and integrated system. This required additional engineering challengers and classification approvals with the USCG and WSF.
Combined with a new charging arm and integrated system, additional vessel structural and operational changes needed to be incorporated with both the vessel and shoreside charging system. The project is coming to the final stages of the detailed engineering phase.
What has been imperative to the success of this project, is the professionalism, collaboration and experience all parties including WSF, Glosten, Stemmann – Technik and Siemens Energy have brought to this uniquely challenging project.
ML: Are you seeing other customers who are interested in a hybrid solution in maritime?
LB: Yes, many including but not limited to clients who own and operate, ferries, offshore vessels for renewables, oil & gas, along with workboats and research vessels. The list is endless for Marine hybrid applications that ultimately provide safer, more efficient, and reliable solutions which can significantly impact on their OPEX and overall carbon footprint.