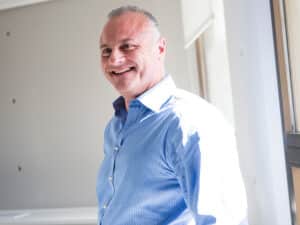
Marine battery maker AYK talks innovation, safety and cost
Written by Marine Log Staff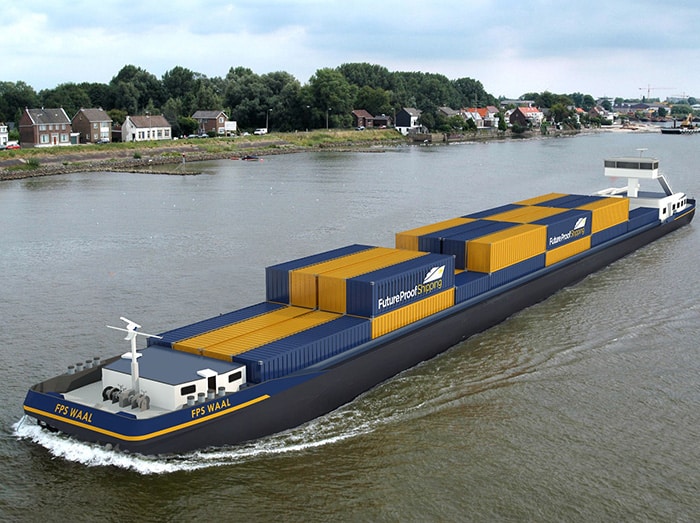
AYK's batteries are being deployed on the high profile zero-emission machinery retrofit of the container vessel, FPS Waal.
Andorra headquartered AYK Marine batteries has seen success in the marine battery industry due in part to innovation in design, safety and driving down production costs.
AYK, established by marine battery pioneer and electrical engineer Chris Kruger in 2018, is seeing a surge in demand since opening a new state-of-the-art automated manufacturing plant in Zhuhai, China, in July this year. The 5,000-square-meter factory ramps up AYK’s production capacity to 300MWH a year, with ability to expand to 1GWH. Its opening was seen as a significant moment in the evolution of the marine battery industry and saw speeches from Wärtsilä, Fjord Maritime Norway, Vulkan Group, Green Energies E-Ship and the Maritime Battery Forum.
Inventor, pioneer, innovator
Speaking with the Marine Log, Kruger said the company is reporting an immediate return on the investment with a 400% increase in quotations in the second half of 2023.
“All manner of vessels are coming to us looking for battery solutions,” he said. “We’re winning work to supply container vessels, car and passenger ferries, tugs and barges. There’s also increasing demand from the superyacht sector which wants green solutions that are safe and affordable. With the drive to decarbonize inland waterways and short sea shipping, we are planning for 10 years of rising demand, underpinned by our commitment to safety and affordability.”
And here is the rub for AYK. Drawing on Kruger’s extensive 15 years of experience, the AYK team has seen firsthand how battery technology has evolved from expensive and hazardous NMC—nickel, manganese, cobalt—to the much less volatile LFP—lithium-iron-phosphate cells. As a result Kruger, has been witness to much trial and error. He says he wants to bust myths around LFP, including its energy density. He says LFP can go toe to toe with NMC on energy density and critically be safer, especially using AYK’s battery design. NMC on the other hand has already been responsible for fires with one battery bank catching fire on a passenger ferry in Norway due to overheating and thermal runaway. Luckily no-one was injured.
“Safe” LFP bests “volatile” NMC
“NMC batteries are becoming more and more hazardous and an accident waiting to happen in my view,” said Kruger. “Density demands are increasing which runs a higher risk of fire due to the violent reaction of NMC. The greater the demand put on the system the greater the risk of cell runaway creating highly flammable chemical compounds. LFP, on the other hand, is a fundamentally safe chemistry. LFP does not create oxygen so the risk of fire is massively reduced.”
Kruger has honed the AYK’s method and approach through multiple roles in both the automotive industry and marine. He believes, given the complexity of the technology, it is difficult for new businesses, without at least 10 years of experience, to break into the marine battery market.
In the automotive sector, he led the team that developed the battery for the Fisker Karma, one of the world’s first production plug-in hybrid electric vehicles that sold mostly in the U.S. But in 2010, even before that car went on sale in 2011-12, he had moved on to be director of engineering at Corvus, where he developed and installed the battery for the first NMC hybrid propulsion ferry, Princess Benedikte, and the first fully-electric ferry, Ampere. He says NMC was used at the time as it was the only real chemistry available, but innovation in LFP is proving a game changer.
Chasing innovation dream
With the conviction that LFP batteries are the future Kruger decided to chase his dream and strike out on his own entrepreneurial venture with AYK Energy. With his team of close advisers and engineers the company has a clear view on the future of the marine battery market. Inspired by Edison’s wizards of Menlo Park the AYK team is pushing the boundaries of what is possible in LFP marine battery technology.
“In a conservative industry like maritime you have to prove you are safe and you are affordable,” he said. “This is why we set up in China. China is the best place in the world for the battery industry. It has the experience, skills, supply chain and infrastructure. Critically it understands safety. For me a lot also came down to price. Some of the pricing around batteries is crazy. I want to change that, hence coming to China where we can drive down costs for our customers. We believe we can drive decarbonization by encouraging faster adoption of battery technology by offering a much more competitive price. This is the excitement of innovation – bringing an invention to a mass commercial market.”

Kruger says the AYK team started by designing the battery management system (BMS) from the ground up. Backed by venture capital funding, the team set out to design a battery—both its hardware and software—that would benefit from his experience of both design and installation work during his previous appointments.
“It was not easy going,” he said, but in 2020 “I had a piece of luck”. That came from making contact with battery cell maker EVE, which was keen to design a battery that could secure marine type-approval from class society DNV and had already devoted two years to the attempt.
After many conversations between the two organizations, Kruger’s counterpart at EVE laid down a challenge: “You say you can develop a type-approved battery, now prove it.”
Kruger set out to do just that: In exchange for space in EVE’s certified lab and the use of its test equipment, AYK would do the rest. Using EVE’s cells alongside AYK’s BMS, Kruger and his team designed, built and tested a marine type-approved battery in just six months, which was “quite a feat,” Kruger said. AYK paid for and sourced all the hardware and retained intellectual property in the final design.
The art of design
That design now forms the basis of AYK’s range of eight battery variants, all of them using the same battery technology and safety features. He says the simplicity of the AYK design enables them to innovate at speed with nine new batteries already designed and a further nine in development which could be launched within months.
Part of AYK’s design secret and safety is the choice of cell chemistry. All its batteries use LFP cells supplied by EVE, making the company unique in using that cell structure in all its products. It is cheaper than NMC which is the most common battery chemistry, and LFP will eventually be “the bridge chemistry to take us to the next generation of solid state batteries,” Kruger believes.
The Chinese battery industry also shares Kruger’s conviction that LFP is safer. China will not allow NMC cells to be used for any application that involves transporting people.
Since LFP is safer the battery design does not have to include structures to improve the safety at a system level. NMC cells have a greater energy density but once they are installed into batteries along with their cooling arrangements, their modular energy density is less than that of an LFP battery, Kruger pointed out. “We can fill most of the module with actual battery”, he said.
They are also less prone to thermal runaway and, should it happen, “it’s not a violent reaction that escalates very fast,” he said. In case that happens, AYK’s battery modules have an automatic water-based response system installed.
Water is used because it has a large phase-change energy value and in the event of a battery overheating, a sprinkler inside the module is activated. This will flood the affected module—not the entire bank of batteries—and because they operate at a low voltage of about 40V, electrical conduction through the water is not a hazard.
AYK has patented this arrangement in China, and Kruger said that it exceeds class requirements for battery fire protection, which call only for detectors in the battery compartment. In addition, AYK’s batteries have three smoke detectors within each module—two must activate before a response is initiated—and the modules are IP67-rated enclosures, each with a blow-out port to release any gasses that build up inside.
This is connected to an extraction duct with a fan to remove any flammable gasses from the battery to be vented outside while any water can be drained via a fitting on the duct piping.
Deals drive decarbonization
AYK’s has recently made deals with the industry’s prime integrators, including Wärtsilä and Siemens. Meanwhile, shipyard clients include Holland Shipyards Group, where its batteries are being deployed on the high profile zero-emission machinery retrofit of the container vessel, FPS Waal, operated by Future Proof Shipping. At time of going to press the successful integration of the battery system on the FPS Waal has led to new orders with Holland Shipyard Group.
“Here, the FPS Waal’s diesel engines will be replaced with PEM fuel cells, storage for their hydrogen fuel, two AYK high density DNV-approved Aries lithium batteries and an electric drive train. The order is the first time that AYK batteries will be used alongside fuel cells, making it a landmark contract for the company,” Kruger said.
Another deal is seeing AYK supply Norwegian aquaculture technology supplier, Fjord Maritime, to convert an oil platform supply vessel (PSV) to a containerized battery powered live fish carrier (LFC). In this instance, AYK worked with Fjord to developed a special containerized battery solution for the vessel which is owned by the Firda Seafood Group, which is also based in Norway.
The DNV Class approved 1MWh Energy Storage Solution (ESS) will be fitted into a container along with Fjord Maritime’s Fjord Hybrid solution. The container is further equipped with all necessary safety and auxiliary systems.
“Containerized batteries are set to be one of the biggest innovations in the maritime industry in the next five to 10 years,” says Kruger. “Containerized batteries have multiple benefits. They can be installed easily on deck without taking space below deck and incurring complex battery room safety requirements. Furthermore, the retrofit process is simple and does not require the vessel to be out of service for very long. When operational the batteries can also then be swapped around with fully charged replacements quickly at shore side charging centers. In addition, the containerized power solution is future proof. When a new more powerful battery technology is developed, or a different form of power is introduced, the container can be adapted for that purpose.”
U.S. and European factory expansion
Looking to the big picture, AYK says its automated manufacturing model can be replicated elsewhere in the world. In the U.S., where AYK’s sales director Ed Carney, is based, for example, the Jones Act encourages domestic sourcing for U.S.-built ships, so if that market opens up, an automated production facility could be built to meet it.
In Europe, too, a similar plant could be built quickly. A site has already been identified and an automated production line could be operational just six months after construction begins, Kruger said.
Kruger is proud of what he and his team at AYK have achieved in just a few years. “We have built the safest battery system with one of the highest energy densities in the industry”, he reflected. And its cost—already one of the lowest—will keep going down because of manufacturing capabilities.”
But he also stressed his batteries’ ease of installation and commissioning. “From the ground up, we designed our battery to allow remote access,” which enables remote support during commissioning and remote software updates. Once installed, bugs and faults can be fixed remotely and data can be easily uploaded to The Cloud for storage and processing. “We believe we are the best and we will work very hard to remain the best,” he said.