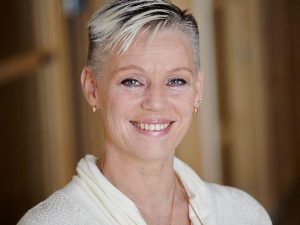
Alfa Laval to offer open training courses
“To ensure safety and optimal use – but also economy in maintenance and operation – it’s important that customers understand the equipment they work with and the many factors that impact its operation,” says Caroline Carlstedt, Training Manager, Alfa Laval Service.
Alfa Laval’s emphasis on training is evidenced, for example, byt the recently built Alfa Laval Test & Training Centre in Aalborg, Denmark, which comprises cutting-edge training facilities in addition to its 250 sq.m testing space.
Customer-focused courses are regularly conducted on Alfa Laval’s premises in Tumba, Sweden and worldwide in locations like the
Philippine capital of Manilla, where around 500 customers are trained each year.
Now Alfa Laval will also offer a range of open coursesl, allowing individual operators and small groups to participate together with industry peers.
Why open training courses?
“Training is in everyone’s interest, but not all shipowners and operators are in a position to fill a dedicated Alfa Laval course,” says Ms. Carlstedt. “Alfa Laval’s open training courses, which will primarily be held at our facilities in Tumba, Sweden, will make our specialist expertise more broadly available to the marine industry.”
“A customer-specific course has the benefit of being 100% focused on that customer’s unique challenges,” she says. “On the other hand, an open course means opportunities to exchange experience with industry peers in similar positions, facilitated by Alfa Laval experts who can provide deeper insights and lead the way to best practices for all present.”
Open training courses will focus on key areas of concern for all shipowners and operators. The first, which will deal with separators, will be a three-day course aimed at equipment operators, technical crew and superintendents. This course will take place February 23-25, 2016.
By relating in-depth knowledge through the courses, and by teaching proper operational, maintenance and service procedures, Alfa Laval experts will help participants to optimize safety and ensure the correct handling that prevents unnecessary wear and stops.
“When customers have attended, they will understand their equipment and be familiar with the issues that affect its operation, which means they will be able use that equipment in the best possible way,” says Ms. Carlstedt. “That will contribute not only to lower maintenance costs, but also to lower operating costs. And when it comes time to refurbish, upgrade or replace the equipment, knowledgeable and competent personnel will be able to provide qualified feedback and support that will lead to a competitive long-term solution.”