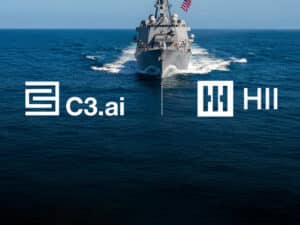
NSRP funding for five more shipbuilding cost reduction projects
Written by Nick BlenkeyThe Executive Control Board of the National Shipbuilding Research Program (NSRP) has awarded funding for five new research and development projects to continue the program’s mission to reduce the costs associated with U.S. shipbuilding and ship repair.
These new projects, valued at approximately $17.1 million in Navy funding and industry cost share, were among those proposed in response to a May 2011 Research Announcement. The NSRP collaboration periodically funds R&D projects to advance technologies and improve processes to reduce shipbuilding and repair costs for the Navy and the shipbuilding industry. The current project portfolio reflects the program’s strategic focus on:
- Reduction in Total Ownership Cost of ships.
- Improved quality in ship construction and/or repair.
- Improved energy efficiency and environmental impact in shipyards and ships.
A brief description of each of the new projects, with a list of participants and funding information, follows:
SHIP CABLE MANAGEMENT
Project Lead: Newport News Shipbuilding
Team Members: TechnoSoft Inc.
Objective: To adapt, enhance and customize wiring application software applicable to all ship programs in order to reduce cost and time for validation of cable layout design, creation of wiring and signal schematics, generation of production work packages, progressing the installation of hangers and cables, and the generation of test procedures.
Program Funding: $2,562K Industry Cost Share: $2,562K
PRODUCTION PLANNING INTEGRATION WITH CAD
Project Lead: Bollinger Shipyards
Team Members: VT Halter Marine, Marinette Marine, BAE Systems Southeast Shipyards, ShipConstructor Software USA, Genoa Design International, Praeses
Objective: To decrease man-hours and eliminate errors by automating the data exchange from a Product Data Model or Computer-Assisted Design (CAD) model into a Production Planning System. The project will leverage work done on the previously funded “Enterprise Resource Planning (ERP) Integration with CAD” project.
Program Funding: $701K Industry Cost Share: $730K
EXPANDING THE MOBILE ROBOTIC WELDING SYSTEM INTO A MECHANIZED
MANUFACTURING SYSTEM
Project Lead: Robotic Technologies of Tennessee
Team Members: Ingalls Shipbuilding, Bath Iron Works, Electric Boat, Tennessee Technological
University
Objective: To develop the existing Mobile Robotic Welding System platform to become a broad- functioning Mobile Robotic Manufacturing System capable of performing multiple manufacturing tasks.
Program Funding: $223K Cost Share: $235K
PRODUCT MODEL DRIVEN WELD MANAGEMENT
Project Lead: Newport News Shipbuilding
Team Members: Ingalls Shipbuilding, Electric Boat, Northrop Grumman Technical Services, Siemens Product Lifecycle Management Software
Objective: To develop and manage structural weld information within a commercially available product model environment. Savings will be realized from man-hour reductions, process cycle time reductions, and quality improvements.
Program Funding: $3,364K Industry Cost Share: $4,772K
DISTORTION CONTROL “TOOL BOX” FOR LIGHTWEIGHT SHIP STRUCTURES
Project Lead: Bollinger Shipyards
Team Members: Vigor Shipyards, BAE Systems Southeast Shipyards, Ingalls Shipbuilding,
Edison Welding Institute, Hepinstall Consulting Group, V. Dlugokecki, Gatekey Engineering
Objective: To compile the physics and principles associated with distortion control derived from previous research and convert that information into a sequenced set of tangible, “shipyard friendly” implementation solutions designed to optimize several shipyard models.
Program Funding: $1,006K Industry Cost Share: $966K
December 16, 2011
Leave a Reply
You must be logged in to post a comment.