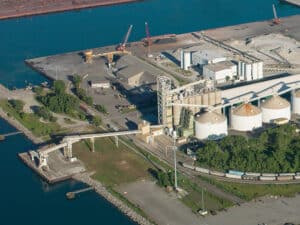
Q&A: How ship-to-shore power decarbonization technology is changing the maritime industry
Written by Heather Ervin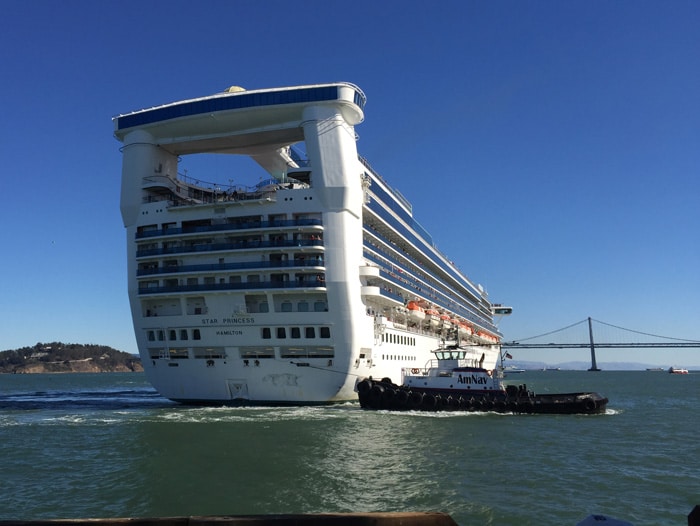
Princess Cruises partnered with Watts Marine to build a shore power system at the Port of Seattle.
Marine technical managers and engineers are tasked with reducing the industry’s greenhouse gas emissions by half or more by 2050 to meet a UN International Maritime Organization goal. To examine the latest progress in ship-to-shore power systems that is helping to expedite decarbonization, we discuss the topic with Conrad Oakley, CEO, NovaTech Automation, a provider of automation and engineering solutions serving the electric utilities, process manufacturing, and marine industries for 40 years.
Marine Log (ML): What is cold ironing, and how can it accelerate maritime decarbonization?
Conrad Oakley (CO): With cold ironing, a vessel shuts down all on-board power generation from diesel engines and connects to shore power supplied by the local utility. In this way, the industry can lower CO₂ and other pollutant emissions up to 98% almost overnight. As a result, custom shore power systems are increasingly popping up at ports throughout North America.
ML: What is required to implement cold ironing?
CO: For an ocean-going vessel, converting to shore power requires proprietary equipment and the ability to accommodate a variety of ship conditions. Ships operate on either 6.6 or 11 KV and have power requirements anywhere from 4 to 16 megawatts with unique load profiles specific to each ship. As a result, the substation in this environment must be able to protect both the vessel and the utility providing the power.
ML: What role do SCADA systems play in implementing cold ironing?
CO: The SCADA systems used in electrical utility substations can be found monitoring and controlling power in cold-ironing systems shore-side as well. As in the case of traditional substations, protection relays and redundant safety systems ensure reliable and safe power transmission while monitoring and control equipment provide real-time management and remote access with in-depth reporting. For ship-to-shore systems, only a few minor customizations are required to provide a full range of power quality and usage reports for the ship and operator billing requirements.
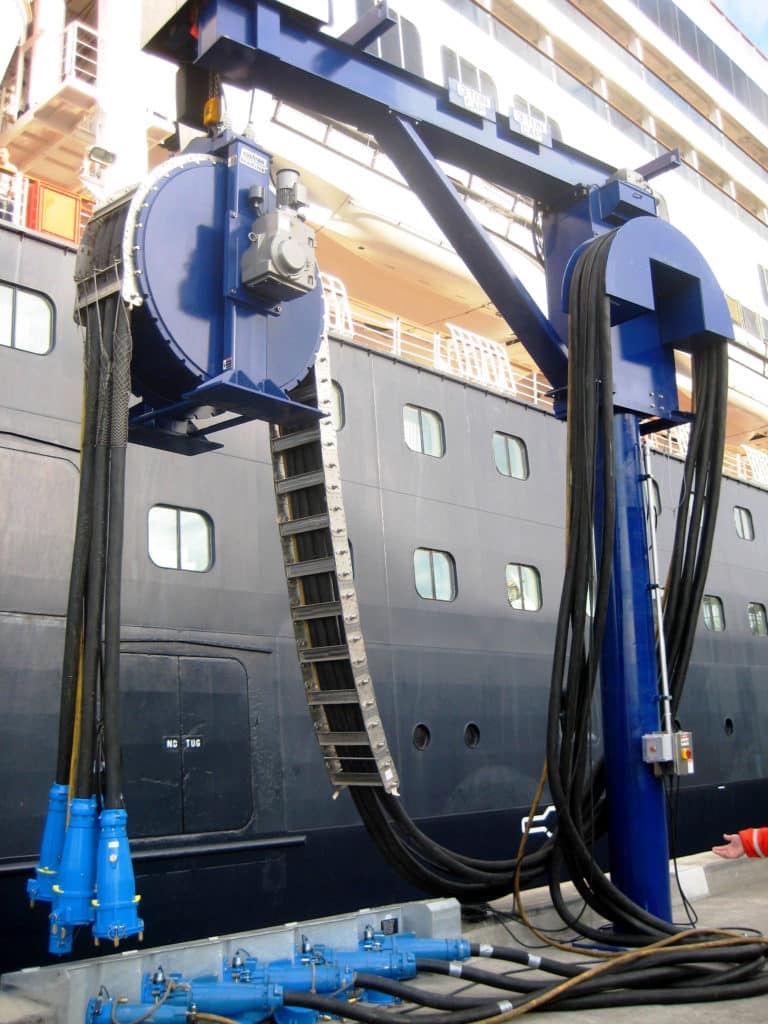
ML: Where was cold ironing first used in the marine industry?
CO: The technology originated with the cruise line industry adapting substations to facilitate connecting an ocean-going ship to shore power while in port. In 2005, Princess Cruises was looking for a partner to build a shore power system at the Port of Seattle. The company reached out to a large electrical contractor with deep experience in commercial high-voltage projects. Design, engineering, manufacturing, installation, and commissioning of the first project was completed in under six months.
ML: How has cold ironing developed in the industry? What equipment is utilized today?
CO: The development of the custom solution eventually led to the formation of a shore power division for the contractor which has now become a stand-alone shore power contractor for ports. Today, Watts Marine supports 10 installations in seven ports across Canada and the U.S.
The patented custom shore power system consists of proprietary equipment designed specifically for the cruise ship industry. It includes dual-voltage electrical service equipment, custom-developed electrical cable handling equipment, and customized electronic monitoring and control equipment.
ML: How is the cold ironing process generally carried out?
CO: Once a cruise ship or ocean transport vessel is equipped to receive shore power docks in port, an operator selects the ship to be connected from a database that is integrated into the customized automation system which determines the proper operating parameters.
The Watts Marine Shore Power System does the rest. In this process, five flexible power and control cables are lifted by a specially designed cable positioning device and connected to the ship’s electrical system through marine standard plugs and sockets. A shore-side operator then closes the breaker and power is supplied to the vessel.
Protection relays and redundant safety systems are used to protect both the ship and shore electrical systems; all the ship’s systems then convert to the shore power. The operator constantly communicates with the ship to ensure a safe transition. Everything is monitored locally, and all systems are also monitored remotely from the main office.
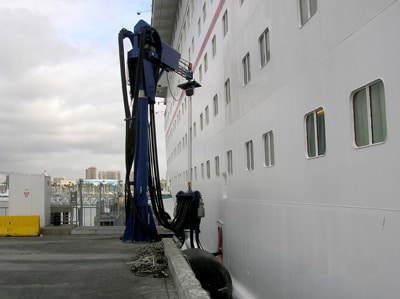
ML: Are there any challenges in cold ironing monitoring and control implementation? Can you give a specific marine industry example of how this is overcome?
CO: Yes. Mike Watts, principal of Kingston, Wash.-based Watts Marine located in greater Seattle and designers of the shore-to-ship power solution, was looking for a partner that would understand their needs and provide monitoring assistance.
“Within the footprint of our system, there is a lot of high-voltage equipment that you would find in a traditional substation, and so the monitoring and protection side is very similar to what utilities install,” says Watts.
Because ships have varying loads, the substation must adjust and change its monitoring points to match each ship’s power needs. Customized solutions are required to address key variables such as voltage, loads and secondary voltage.
“With cruise ships, we are plugging into different power requirements that can be anywhere from four to 12 megawatts,” said Watts. “In addition, the ships operate on either 6.6 KV or 11 KV voltage classes. We needed a solution that would work with different load profiles.
After initially meeting at a trade show in 2008, the company selected NovaTech Automation, a Pennsylvania-based provider of the industry-leading Orion automation systems, to provide the remote monitoring and reporting capabilities required for their shore-to-ship power solution.
“At the time, we only had two systems installed but it was still important for us to monitor everything at each location remotely,” says Watts, adding that at the home office there is the ability to see all their systems’ status in a single line item.
The Orion automation system collects data from Bitronics panel meters which provide electrical measurements such as voltage, amp and currents, fault and event records, as well as trend logs.
An operator uses custom HMI frames that are fed by customized Orion web pages for local and remote visualization. Alarms are triggered automatically when things fall outside of range operating like a traditional SCADA system.
The Orion also provides detailed reporting of key metrics of the shore power connection including (KWH) of energy consumed and connection start and stop times.
ML: What do you see as the future of cold ironing in the industry?
CO: With the ability to condition, manage and remotely monitor the use of shore power to meet a ship’s electrical needs while in port by adapting traditional substation automation solutions, there is an opportunity to use this technology with other ocean-going vessels in the future as well. This is sure to have significant environmental benefits by reducing harmful emissions in residential, commercial, and industrial areas near busy ports.