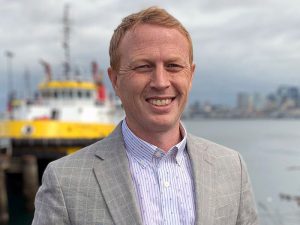
Bryan Nichols joins Crowley marine services team
Crowley Shipping reports that Bryan Nichols is moving over to the company’s marine services team as manager, business development. With 30 years of experience, Nichols has built a career helping develop industry-leading