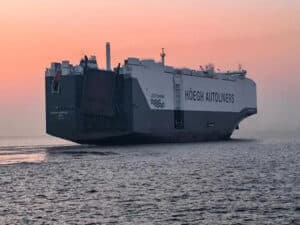
MEPC 75 is expected to fix ballast water commissioning testing, but operational risks remain
Written by Marine Log Staff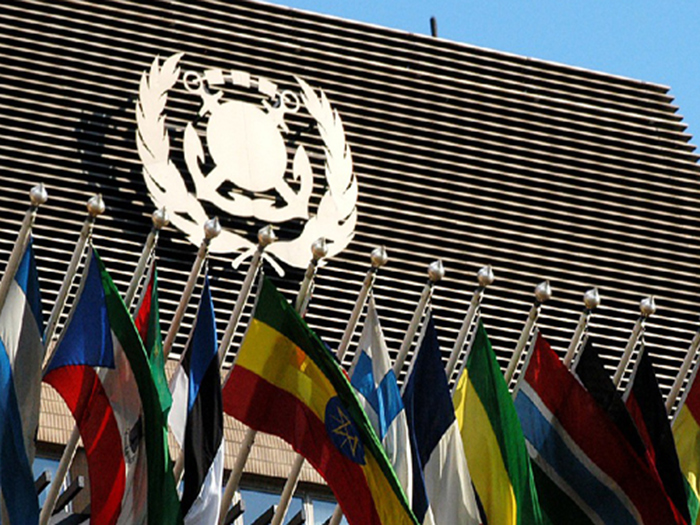
Image: IMO
Shipowners rightly expect that any IMO or USCG certified Ballast Water Management System (BWMS) will make legal compliance straightforward, but that is currently not the case, (writes Adam Jolliffe, Senior Sales Manager – Maritime, Chelsea Technologies). Under current regulations, these systems could be malfunctioning upon delivery, or could later develop an undetected fault. Motions tabled at the 75th session of the IMO Marine Environment Protection Committee (MEPC 75), being held virtually November 16-20, are expected lead to a step forward, but some risk is expected to persist.
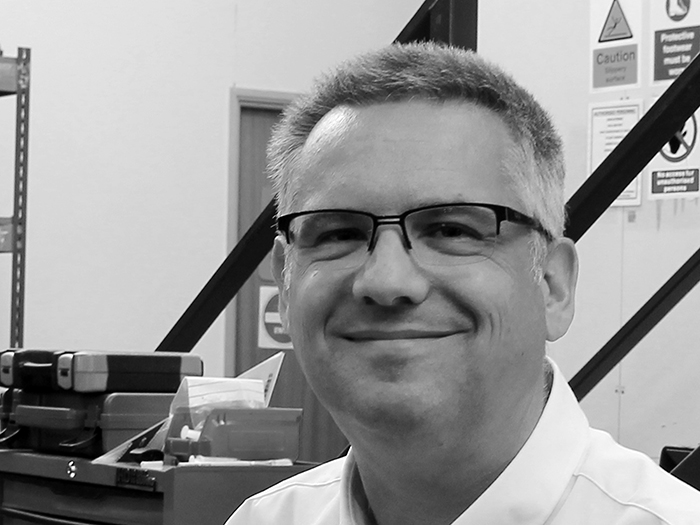
A BWMS does not currently need to be tested upon installation, and research in May 2020 from SGS, one of the world’s leading inspection, verification, testing and certification companies, suggests that 21% of systems installed would not treat water to a compliant standard upon commissioning.
In its white paper, SGS noted that these systems are likely to represent a continued compliance risk for shipowners – as the issues that have caused problems will not have been rectified. In some cases, a shipowner may not know about these issues until port state control takes enforcement action.
Shipowners are entitled to believe that their BWMS will be compliant upon installation, and identifying that there is an issue goes a long way to ensuring that it will be rectified. Indeed, many issues occur during the installation process, and could be corrected simply – if they’re identified quickly.
Staying compliant
In February, the 7th session of the IMO’s Sub-Committee on Pollution Prevention and Response (PPR 7) recommended a new standard for commissioning testing that will ensure BWMS work as intended upon delivery. This standard would see indicative testing employed to confirm that a BWMS is functioning properly when it is installed, so that any issues can be spotted and resolved. This standard is expected to be adopted by MEPC 75, and is a vital step to ensuring that shipowners have the right tools to comply with the regulations.
However, this will not solve all of the operational issues that shipowners have reported. The scale of these operational challenges was recently laid bare by Carsten Ostenfeldt, Anglo-Eastern’s managing director, when he outlined the issues that his company had faced. Every one of the approximately 210 BWMS, from nineteen different models, fitted to ships managed by Anglo-Eastern exhibited some issues during the first year of use.
Mechanical failures after delivery will always represent an operational risk for shipowners. Faulty filters, electrodes, and other sensitive pieces of equipment can cause non-compliance, while the risk of unexpected mechanical issues causing non-compliant discharges will only increase as systems age.
A relatively minor issue may cause a non-complaint discharge, even if a system appears to be working as it should. A damaged system may not provide any data that shows that it is not treating water to a compliant standard, depending on the fault. Known issues with electrodes and filters can cause a BWMS to treat ballast water to a non-compliant standard without no outward signs of a fault.
Increasingly, it is being recognised that human error represents a similar threat. Shipowners and regulators cannot expect crew to be microbiologists, while each of the 100 BWMS on the market is operated differently. Should a crew genuinely believe that it is following the correct operational processes, the data produced by a BWMS is not likely to alert it to failures.
Ongoing monitoring is key
This burdens shipowners with a huge amount of hidden risk. Despite spending significant amounts of money on BWMS systems and following current best practice to the letter, an owner could face significant fines and other costs. An example of this was reported by law firm Reed Smith, as “the relevant U.S. law, 33 CFR section 151.2080, imposes a civil penalty of US$35,000 per day for non-compliance, and criminal liability for those who “knowingly” violate the law”.
The best way to manage this risk is through investing in ongoing indicative monitoring processes. This should be ingrained in shipowners’ approaches to ballast water management, as well as in regulation.
Unlike laboratory based testing, indicative testing takes a negligible amount of time and resource. An ongoing process using this technology could either entail regular testing with portable devices, or continual shipboard testing.
Of course, shipowners and regulators would have to be certain that indicative tests are reliable, practical and accurate enough to provide useable data. These core concerns drove the development of Chelsea Technologies’ FastBallast system; integrating a sophisticated measurement technique with a convenient, portable, and user-friendly instrument, the system provides a lab-equivalent degree of accuracy with little to no additional training.
Chelsea Technologies designs, manufactures, and supplies environmental monitoring technology across the maritime, marine science, water quality, defence and industrial process control industries, including the FastBallast ballast water testing system and Sea Sentry scrubber washwater monitor for the maritime industry.
MEPC 75 is expected to implement changes that will have a real impact, and new commissioning testing standards represent a real positive change for shipowners, manufacturers, and other stakeholders. However, concerns about operational compliance will persist until shipowners have a reliable, accurate way to collect and measure data on an ongoing basis. Regular, ongoing indicative testing is the key to de-risking ballast water management.