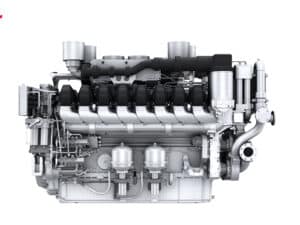
Op-Ed: Hydraulic fluids and the future of compliance
Written by Heather Ervin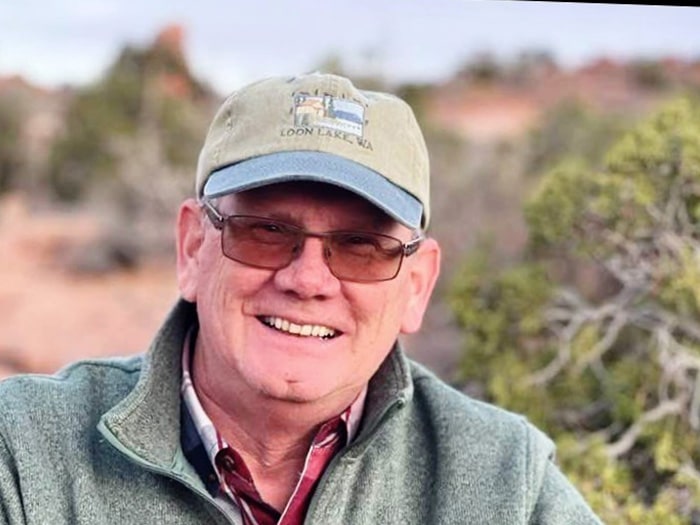
By Joe Weinand, industrial lubrication specialist, Chevron
Behind every successful marine operation lies an increasingly complex challenge: meeting increasingly stringent environmental standards for hydraulic fluids without sacrificing performance. Operators are under pressure to address fluid toxicity, biodegradability, and bioaccumulation potential while maintaining the operational demands of their equipment.
Hydraulic fluids have long played a central role in keeping maritime operations running, and the next generation of these fluids is being shaped as much by environmental policy as by performance benchmarks. Understanding how today’s advanced fluids are changing can offer a look into the future of regulatory compliance and operational resilience.
Environmental Impact Is No Longer an Afterthought
Historically, environmental considerations in hydraulic fluid selection often took a backseat to performance and cost. That’s no longer viable. Regulations like the U.S. EPA’s Vessel General Permit (VGP) and Europe’s Ecolabel standards now require fluids in specific applications, such as propulsion systems and hydraulic deck equipment, to meet stringent criteria for biodegradability, low toxicity, and limited bioaccumulation.
Environmental Acceptable Lubricants (EALs) are categorized based on their biodegradation rates: readily biodegradable fluids break down by 60% or more within 28 days, while inherently biodegradable fluids degrade by 20% or more in the same timeframe, according to testing methods established by standards organizations. These metrics are increasingly viewed as environmental indicators and compliance thresholds that maritime operators must proactively manage.
This shift is driven by more than policy. Operators are also recognizing that non-compliant fluids can pose substantial business risks. Leaks or spills of traditional mineral-based lubricants can lead to costly cleanups, regulatory fines, and reputational damage. In contrast, using EALs that meet the latest compliance standards helps mitigate these liabilities.
The Rise of Next-Generation EALs
One of the most common critiques of early EALs derived from vegetable oils was their poor oxidative stability, limited lifespan, and tendency to degrade seals and polymers in hydraulic systems. These drawbacks made many operators reluctant to switch, even when facing compliance mandates.
Today, synthetic EALs formulated with renewable base stock and advanced additive technologies have largely closed that performance gap. Some formulations meet or exceed conventional fluids in key areas such as wear protection, thermal stability, and fluid longevity. Importantly, modern EALs are designed with broader seal compatibility, minimizing the risk of degradation or equipment failure during fluid transitions. These advancements not only support long-term performance but also reduce the total cost of ownership by extending service intervals and minimizing maintenance disruptions.
Best Practices for Transitioning to EALs
While fluid technology has advanced, successful adoption still relies on a careful evaluation process. Before switching to a new EAL, operators should:
- Review seal compatibility: Ensure the fluid’s chemical composition aligns with existing equipment materials to prevent leaks or premature wear.
- Conduct fleet surveys: Document current fluid types, change intervals, and equipment usage profiles to guide the transition plan.
- Monitor condition data: Implement fluid analysis before and after the switch to track degradation, contamination, or performance loss.
- Partner with technical advisors: Collaborate with Original Equipment Manufacturers (OEMs) or lubricant specialists who can provide application-specific guidance and help fine-tune maintenance schedules post-transition.
Education is also key. Teams should be trained on the technical properties of new fluids and the rationale behind the switch, from reducing ecological risk to future-proofing operations against tightening regulations.
The Future of Hydraulic Fluids
As responsible companies work to meet or exceed all environmental requirements. The role of hydraulic fluids is shifting from a routine consumable to a critical component of ecological compliance strategy. In the coming years, operators can expect more emphasis on lifecycle performance and transparency in fluid sourcing and formulation.
The good news is that modern fluid technologies are rising to meet these demands. By embracing advanced, compliant hydraulic fluids today, operators can position themselves for regulatory readiness and long-term operational and environmental durability.