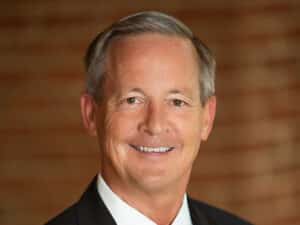
Op-Ed: What to look for when inspecting flexible couplings
Written by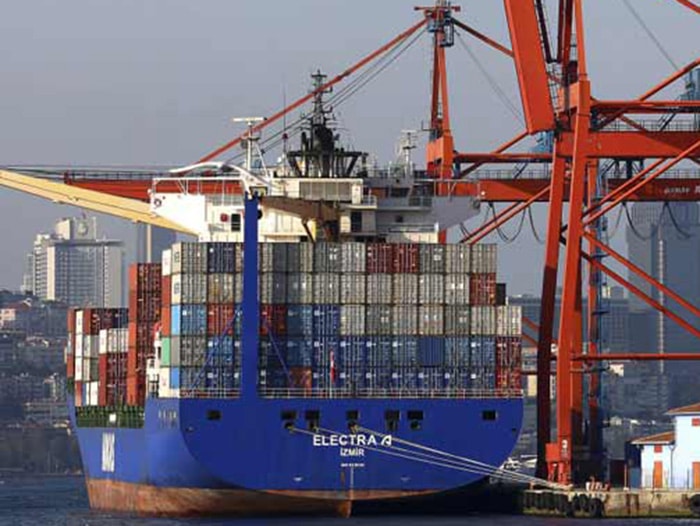
Credit: Regal Rexnord
By Bob Lennon, Regal Rexnord
Of the many components that comprise the essential equipment used in the marine industry, flexible couplings are often overlooked during regular inspection and maintenance. This can be a costly mistake, as flexible couplings are vital to the overall performance and reliability of marine powertrains. Understanding the importance of couplings, their proper working conditions and their required maintenance can optimize the life of these critical components and reduce unplanned downtime.
Why is it important to inspect flexible couplings?
Couplings transfer rotational torque between the driver (e.g. the motor) and the driven (e.g. the propeller). They dampen shock loads and accommodate for any misalignment. In the case of a reciprocating system, couplings also protect against torsional vibration, which can lead to expensive repairs and lengthy downtime. Performing these tasks can cause a great deal of strain to this essential powertrain component.
In addition, flexible couplings used in marine propulsion are typically constructed from natural and synthetic rubber, and have a life expectancy before they require replacement. These materials harden over time, slowly losing the torsional characteristics that make them useful. In the best-case scenario, flexible couplings will typically last for 10 years or 50,000 hours before material hardening makes a significant impact. However, other external factors such as exposure to oil, solvent, UV and ozone, ambient temperatures, equipment misalignment and operational factors can also come into play when determining the lifespan of flexible couplings.
How to establish the proper maintenance procedures
Maintaining flexible couplings begins at the initial assembly. Alignment, bolt tightening methods and torque values are important to ensure proper function. Installers should take care to follow all relevant manufacturers’ recommendations while also cross-referencing documentation from the engine manufacturer for suggested tolerances. When performing alignments, assume the vessel is loaded (in the water and properly bunkered) and the engine temperature is elevated (to accommodate for thermal growth corrections). If any of the equipment is on soft mounts, confirm the mount conditions according to the supplier’s recommendations. After initial test runs or sea trials, operators should perform a careful visual inspection and confirm that bolt torques are still within the appropriate range.
Following the initial startup, operators should perform their first inspection after two or three months, followed by a second inspection at the six-month mark, to confirm that alignment and bolt torque values remain within specifications. Following this, operators can scale back to thorough annual inspections.
Tips for maintenance and inspections
It’s always possible that routine maintenance and inspections may reveal healthy couplings. However, to minimize the chance of downtime, it is always best to plan to perform any coupling element exchanges during this time. Planning for the exchange and maintaining an inventory of required spare parts will ease any necessary exchanges while avoiding undue interruptions in the operation of the vessel. It is also a more cost effective alternative than placing an emergency rush order for replacement parts for an unexpected replacement. In place of maintaining a replacement parts inventory, marine operators can coordinate with a local supplier or distributor to avoid unexpected delays, unplanned equipment downtime and lost revenue.
Natural and synthetic rubber will show signs over time of twisting and potential cracking. When conducting maintenance and inspections, operators should follow a documented process for lifetime periodic inspections, using them as an opportunity to record coupling conditions and compare against manufacturer-recommended twist and crack limits. By measuring, marking and documenting any cracks found, the inspector can track the increase in severity during subsequent inspections and plan to replace the coupling at a future maintenance date.