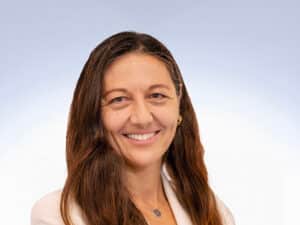
Op-Ed: Reducing emissions is job one for maritime
Written by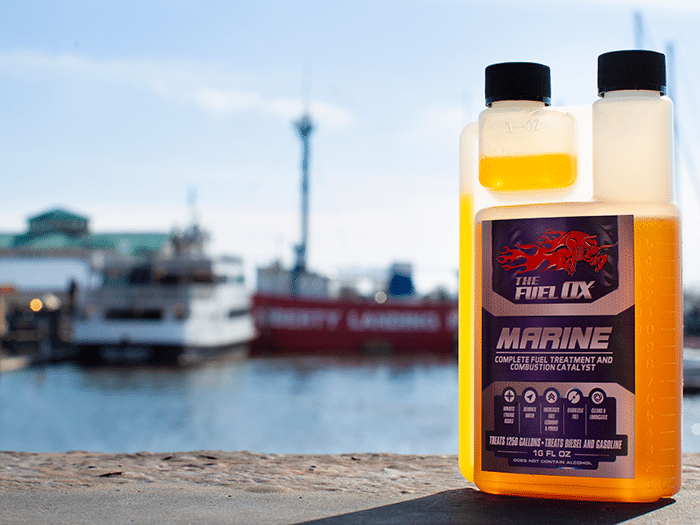
Credit: The Fuel Ox
By Rand Taylor, CEO of The Fuel Ox
In April 2018, the International Maritime Organization agreed on its first ambitious strategy to reduce greenhouse gas emissions in the international shipping sector to meet the Paris Agreement goals.
The strategy included a target to reduce carbon emission by at least 50% compared with 2008 levels by 2050. But, experts agree that can be a difficult goal to achieve for two reasons: 1. The maritime sector is notorious for imposing significant barriers to innovation, and 2. The “green energy” needed to operate ships and ports at net-zero levels is still far from within our grasp.
However, despite the resistance to new technologies, there are a few lights on the horizon.
In March 2022, the U.S. Department of Energy and the Bioenergy Technologies Office (BETO) hosted an informational webinar that ran through some of the progress that had been made to that point in the development of sustainable marine fuels and fuel additives. In the webinar, they highlighted the following pros and cons:
- While there have been positive advancements in the development and availability of biodiesels and renewable diesels that could significantly reduce carbon impact, they are only part of the solution. What remains are land-use, cost and availability risks that remain for the category, resulting in slow industry buy-in.
- Smaller vessels can chip away at emissions by switching to hydrogen or electric power, but we are years away from optimizing those technologies.
So, while we wait (years or maybe decades) for the think-tanks of the world to come up with a new way to power our ships more sustainably, the industry will continue to use diesel. We all know diesel has a bad reputation for being pollutive—ultra-fine particulates create unsightly and unhealthy soot when it burns. So, what can we do TODAY to manage emissions on ships running on diesel fuel? The introduction of diesel particulate filters (DFPs) in the 1980s helped alleviate some of the issues, but it far from solved the problem. The fuel still burned “dirty” and the filters have a hefty, costly maintenance schedule.
About 40 years ago, around the time when DPFs were introduced, Bell Labs was developing a fuel additive to combat issues with fuel breaking down in arctic radar stations. By 1990, the additive was transformed into a “super formula” that effectively combated all issues with fuel and the U.S. military began using it extensively. Just five years later, in 1995, it began to be used to treat heavy fuel oil in large vessels. Today, that additive, now known as “The Fuel Ox,” is commercially available and is used by hundreds of maritime, mining, manufacturing and trucking companies.
A fuel additive with a combustion catalyst like Fuel Ox increases lubricity and promotes a more thorough burn of fuel, resulting in better efficiency, reduced emissions (by 50%) and longer-lasting engines and components. Carbon dioxide emissions have also been proven to be reduced by 20% or more and nitrous oxide by as much as 10% or more.
In a recent self-directed study, McAllister Towing & Transportation—one of the oldest and largest family-owned marine towing companies in the U.S.—conducted a month-long A/B test comparing fuel consumption of its twin engine, 4000 horsepower Z-Drive tractor tug. The engine using Fuel Ox Marine with Combustion Catalyst burned 42.85 gallons of fuel per hour, a 5.97% improvement over the untreated engine, which burned 45.57 gallons per hour.
In addition to the fuel efficiency, there is the matter of sustainable lubrication. Standard lubricants on the market rely on heavy, toxic ingredients—specifically petroleum soaps and ultra fine metals like molybdenum. There are two sustainability issues at play here: First, not only are toxins released during use, but they remain in the product upon disposal. A single quart of used engine oil can contaminate 1,000,000 quarts of ground water. The second issue is the lack of efficiency of these lubricants. Most of these greases and oils claim to achieve sustainability rates of just 10-20%, resulting in a 90% rate of mechanical failure attributable to improper lubrication.
While we may be stuck with diesel for an indefinite amount of time, we can “green up” existing technology by better managing the fuel we use and providing our heavy machinery with a toxin-free, friction-free environment.