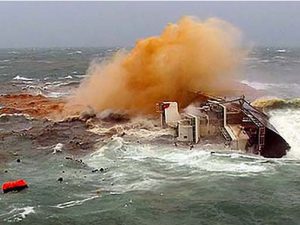
DNV GL releases new guideline on cargo liquefaction
Many common bulk cargoes, such as iron ore fines, nickel ore and various mineral concentrates, may be subject to the phenomenon, in which a soil-like material is abruptly transformed from a solid dry state to an almost fluid state.
If liquefaction occurs on board a vessel, the stability will be reduced due to the free surface effect and cargo shift, possibly resulting in capsizing of the vessel. The ship structure may also be damaged due to increased cargo pressures.
DNV GL says there are some distinct and disturbing features of accidents caused by cargo liquefaction.
First, the accidents happen very fast. The period of time from when liquefaction is detected, if it is detected at all, until the vessel has capsized could in some cases be only a few minutes. This leaves very little time for remedial measures. It also leaves very little time for safe evacuation of the ship, and such accidents are often associated with tragic losses of crew members.
Second, an accident on one vessel is often followed by a new accident, or near-accident, on other vessels that have loaded similar cargo at terminals in the same area.
DNV GL’s new guideline aims to raise the awareness of the risks of liquefaction and describes mitigating actions to reduce these risks.
“Cargo liquefaction is probably now the most significant factor in lives lost at sea for bulk carriers,” says Morten Løvstad, Business Director of Bulk Carriers at DNV GL. “While the general safety level of modern bulk carriers has been significantly improved over the last decades, recent incidents have shown that cargo liquefaction remains a major safety issue. Since 2009, at least six ships of more than 40,000 dwt have been lost to suspected liquefaction of cargo. These incidents have shown that cargo liquefaction is an issue that has not been sufficiently dealt with, and concerned owners and operators have contacted us for support and advice.
“With this guideline we wanted to help our customers by not only increasing awareness and building competence around the phenomenon, but also to offer some strategies, both in design and operation, to reduce these risks.”
The guideline focuses on both the operational and design aspects of cargo liquefaction.
In daily operation, recommendations to reduce the risk of liquefaction include:
- making sure that cargo is correctly identified and properly documented
- ensuring the time interval between testing for moisture content and loading is no more than seven days and that retesting is done in the event of rain
- appointing an independent surveyor and performing a can test or similar to verify the moisture contentloading in a non-homogeneous pattern
- raising the center of gravity by ballasting the top wing tanks (provided loading condition and structural strength allows for it), and trimming as necessary to ensure cargoes are reasonably level
The design guidelines look at the potential of carrying cargoes with high moisture content onboard specially constructed or fitted ships, in compliance with the IMSBC Code. Such vessels can remain safe both from a stability and strength point of view even if the cargo liquefies or shifts.
“Under the IMSBC code such vessels must have permanent structural boundaries or specially designed portable divisions to confine any shift or liquefaction of cargo, but detailed requirements are lacking,” says Mr. Løvstad. “It is clear, however, that stability and structural strength have to be specially considered, and our guideline sets out criteria for them, based on DNV GL procedures and rules.”
The guideline also examines how and why liquefaction can occur, which bulk cargoes are subject to liquefaction risks, explains the Transportable Moisture Limit (TML) and presents the effect of liquefaction on a vessel. The aim of the guideline is to provide ship designers, shipyards, shipowners and other stakeholders in the shipping industry a basis to assess the risks and begin the process of making their vessels and their operational processes safer when it comes to the risks of liquefaction.
Access the guideline HERE