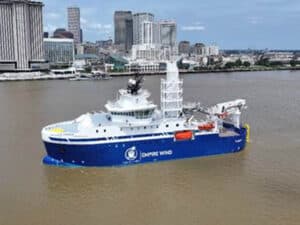
Op-Ed: Three things to watch as floating offshore wind heads into full commercialization
Written by Marine Log Staff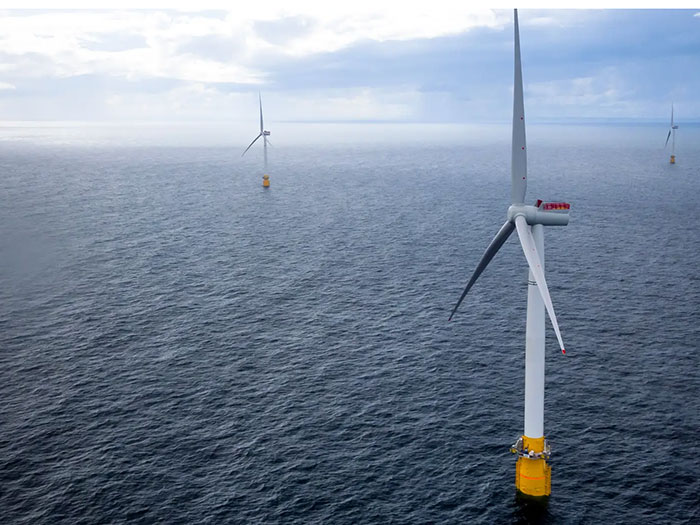
Equinor's HyWind Tampen floating offshore wind farm [Image: Equinor]
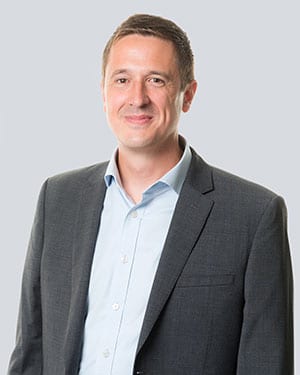
Director, offshore engineering,
Houlder Ltd
by Mark Goalen. Director, offshore engineering, Houlder Ltd
As the floating offshore wind market shifts from its current demonstration stage into full commercialization, there are three factors driving the outcome.
The offshore wind market enjoyed its best-ever year in 2021, with 21 GW commissioned, of which 57 MW was floating wind capacity. Yet the industry remains in its infancy. By 2030 we expect 5 GW in the U.K. and for continued growth from there. Although there is commitment and confidence that full commercialization will be achieved, there is much to do, and significant challenges to overcome.
Three factors will be instrumental in defining how the market matures this decade: geography, technology, and project management.
Geography – who dares, wins…
Beyond the U.K., there are several countries to watch as the market develops: the U.S. West Coast, France, Ireland, Italy, Morocco, Korea, and the Philippines. While not part of the small group of pioneers already installing the first commercial-scale floating wind projects, they are expected to follow closely behind, according to Global Wind Energy Council report “Floating Offshore Wind – A Global Opportunity” released earlier this year.
For the U.S/, the incentive to “go deep” is there because almost two-thirds of its offshore wind resources are found in waters that would require floating platforms. Yet, while there is a clear direction, with clear intention for investment, there is a noticeable lack of commitment from developers on which technical solutions they plan to install for any given floating site.
Technology – no silver bullet
What is emerging is that there is not going to be one definitive foundation type. Rather, developers will need to identify the most suitable type of foundation for each location, and not just the offshore site. Consideration must be given to the port that will support the development: water depth, available space for fabrication and storage of parts during the assembly process.
There are multiple solution providers developing various models in each of the four main structure types:
The first structure type is a spar buoy. These are very stable given their deep draft with ballast creating a low centre of gravity and they are conventionally catenary moored. They require a deep-water area for fabrication and maintenance (if towed to shore). They have been used for Hywind Scotland and Tampen.
The second structure type is a tension leg platform (TLP). It is less stable than other options until moored. The biggest advantage is that, by having taut mooring lines, the length of line required is significantly reduced for deep water locations in comparison to a catenary moored structure. TLPs have recently been out of favor due to some difficulties at the test stage, but BEIS’ SENSEWind development will make use of a TLP, and other developers are interested in their feasibility.
Semi-submersible platforms are typically three-legged floating structures. They are considered the front runner for most U.K. locations given that relatively shallow water is required at fabrication site, stable for tow during installation and operations and maintenance. However, they are prone to heave motion, which is difficult to prevent without increased fabrication complexity.
Finally, there are damping pool structures. These are square barge structures which contains a damping pool to reduce or tune the foundation motion. They can be made from concrete or steel, which could be advantageous for some fabrication locations.
This is not a static list. Foundation designs continues to evolve as new innovations resolve earlier technical difficulties, and new technologies continue to open up possibilities for reducing commercial and technical risk. Advances in fabrication, such as robotic welding, complete with machine learning, will have a significant impact on project cost due to increased production efficiency.
Project management: risks and costs
Project cost is the key driving factor for the success of the industry. It’s one thing to categorize the technology. What is more challenging is determining the suitability of each option for a given location in terms of operability, reliability, practicality, cost, potential longevity, and risk.
The industry is still learning. The Hywind Scotland project became the first commercial-scale offshore floating wind farm in 2017, with five 6-megawatt turbines supported by spar buoys designed by Equinor. But Equinor has now publicly stated that is technology-agnostic and looks at the site to decide which foundation type is the most preferable.
There are a lot of influencing factors – fabrication, moorings, installation, maintenance, motion response, operability etc. Defining the O&M strategy upfront is also critical: Are turbines in need of repair or maintenance towed back to port? Or will planned maintenance take place on location? The most economical, and lowest risk option will prevail, but if the work is to be done on location, thought needs to be given now to the maintenance and repair vessels as they don’t currently exist.
It is essential to have the right expertise at the initial phase of the project to ensure that developers gain a holistic understanding of the processes, equipment, vessels, and crews involved from the outset. This is where objective advice from independent naval architects can be so valuable. Only this will minimize risk and preserve the overall best cost advantage for the project and drive the industry as a whole forward to full commercialization and a smooth energy transition.