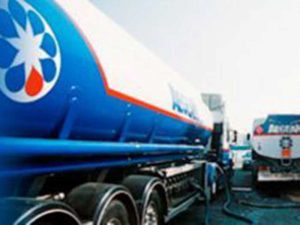
Aegean Marine Petroleum launches Savannah service center
JUNE 26, 2017 — Aegean Marine Petroleum Network Inc. (NYSE: ANW) has launched a new service center in Savannah, GA, the third largest container port in the United States. The operations in
JUNE 26, 2017 — Aegean Marine Petroleum Network Inc. (NYSE: ANW) has launched a new service center in Savannah, GA, the third largest container port in the United States. The operations in
MARCH 28, 2017—With the the IMO Global Sulfur Cap of 0.5% looming on the horizon in 2020, Jack Jordan, Editorial Lead, S&P Global Platts, writes about whether shipowners will embrace burning Liquefied
MARCH 9, 2017 — The Port of New York and New Jersey is getting set to receive the new generation of higher ultra-large container vessels (ULCV). The controlling depth of the major
JANUARY 10, 2017 — More crew were kidnapped at sea in 2016 than in any of the previous 10 years, despite global piracy reaching its lowest levels since 1998, according to the
DECEMBER 29, 2016 — Shipbroker Marcon International, Inc., Coupeville, WA, has passed a notable milestone. Over the last 35 years it has brokered 322 tugs for sales or charter, totaling 1,005,657 HP.
NOVEMBER 7, 2016 — Federal Maritime Commissioner William P. Doyle has issued a follow-up statement on the Ocean Alliance Vessel Sharing Agreement. On October 21, 2016, the Federal Maritime Commission voted to
It was a nasty winter, even by Alaskan standards. The city of Nome, Alaska was in trouble. A late November storm blocked a scheduled shipment and the city was running out of fuel. In an Arctic winter, fuel is as precious as blood. It powers more than cars and trucks, it runs generators to light up the 24 hours of darkness and it burns in boilers for heat when the outside temperatures regularly hit -50 degrees. Without fuel, all human life stops; and Nome’s tanks were running dry. The solution to the crisis lay in the belly of a Russian ice-strengthened tanker sailing just offshore. The problem was that her cargo of life-sustaining gas and diesel was loaded in Dutch Harbor Alaska, and a U.S. law designed to protect domestic shipbuilding was preventing her from completing the mission. Recognizing the urgency, Secretary of Homeland Security, Janet Napolitano, issued a one-time waiver of the Jones Act and the Renda steamed into Nome Harbor to deliver the fuel.
As changes in Arctic continue to unfold, incidents such as the one in Nome will become more common. In addition, the pace of change in Arctic has found the U.S. unprepared to assert her claims and to defend fragile ecosystems and populations. The Nome incident illustrates a stark choice for the U.S.: change how the country protects its domestic shipbuilding, or cede the Arctic to its geopolitical rivals.
The Jones Act requires that any ship carrying passengers or cargo between two U.S. ports must be built in the U.S., crewed by U.S. nationals, and owned by a U.S. company. The Act dates back to the 1920’s but the idea of protecting a domestic shipbuilding industry from foreign competition is as old as the country itself. The First Congress of the United States levied heavy tariffs on goods delivered on foreign ships. The Act serves that important role today; however, the economic reality is that Jones Act compliant ships are expensive to build and expensive to operate. So to maximize profits, large ships in the international trade are flagged in countries with favorable laws and tax treatment. Such “flags of convenience” create strange outcomes as cruise ships that pick up vacationers in Miami must first stop somewhere outside of the U.S. before discharging their passengers. Foreign flagged tankers, loading crude in Valdez may take that crude to a foreign port where it is pumped ashore, modified slightly, then reloaded on to the same ship before that ship sets sail for a U.S. refinery.
Opponents of the Jones Act point out the inefficiencies created when non-compliant vessels seek to skirt the law. They argue that the trade protection measure makes coastwise shipping prohibitively expensive as shipbuilders in the U.S. must operate under more expensive environmental and labor regulations. Similarly, the U.S. ownership requirement cuts off sources of capital to build those ships. Without the Jones Act, the argument goes, we could use international competition and realize benefits and efficiencies of moving freight over water. For example, we could put containers on barges that service coastal cities, thereby removing thousands of trucks from the already choked and crumbling interstate highways.
Proponents of the Act cite jobs and national security interests. During World War II the U.S. shipbuilding industry saved the world from fascism by building Liberty Ships faster than German submarines could sink them. Today, the market for Jones Act compliant vessels supports thousands of good paying jobs and preserves skills that would desperately be needed should the world face a similar crisis. The decline in domestic manufacturing under the auspices of free trade serve as a warning to those looking to open U.S. shipbuilding to foreign competition.
The Arctic presents a different problem. As the ice recedes, human demands in the Arctic will increase. Just this year, 1,000 passengers aboard the cruise ship Crystal Serenity sambaed and bunny hopped their way through the once impassable Northwest Passage. As a result of increased economic activity, settlements in the Arctic will grow. More people in the Arctic means more demand for ice class ships to resupply villages and outposts. More shipping also means increased demand for search and rescue and spill response. As demand for icebreakers and ice class ships increases, there are few Jones-Act certified ships to fill the need. In contrast, countries such as Finland have an excess of icebreaker capacity. Those ships, however, cannot operate between U.S. ports in the absence of a Jones Act waiver from the Department of Homeland Security.
In addition to support for economic activity, presence in the Arctic is critical for political reasons. Conditions in the Arctic are changing faster than most expected and wherever the ice recedes, it leaves behind a geopolitical vacuum. As the ice pulls back from the shore, it will expose trillions of dollars in natural resources. More importantly, it will uncover fragile and delicate ecosystems and leave indigenous populations exposed to potential exploitation. Russia has already staked its claim to a vast undersea territory stretching almost to the North Pole. In the last few years, Russia has been quietly rebuilding its fleet of Soviet era icebreakers. Today, Russia has scores of ice class ships, six nuclear powered icebreakers, and three more heavy crushers on their way. China, with no territory in the arctic, has two icebreakers with a third on the way. The United States, a country with the world’s most powerful and well equipped military, has one heavy icebreaker, and it is 40 years old. Congress has allocated funds for a second ship, but construction will not start until 2020 and the ship will not see ice until 2025. Protection of the environment and native people in the Arctic will require a U.S. presence and a U.S. presence will require icebreakers now.
Typical Jones Act problems involve competition between foreign and U.S. flagged ships. But with little or no U.S. ships to fill the need, the Jones Act forces a choice between using a foreign flagged vessel or nothing at all. As the situation in Nome demonstrated, that is not a choice when lives, the environment, or a critical national interest is at stake. The current administration can fix this. The Secretary of Homeland Security, using executive authority, can and should grant a temporary waiver for all ice class vessels operating from the Aleutian Islands in the south to the Canadian border in the north and in all U.S. points above the Arctic Circle, until such time as an equivalent Jones Act compliant vessel becomes available. Such a rule would allow the U.S. to immediately defend her geopolitical interests by freeing up the one available icebreaker. While the waiver is in place, existing foreign vessels could develop and test markets for commercial shipping with ice breaking capabilities. If it appears the market will bear the increased cost of a U.S. flagged ship providing those services, U.S. shipbuilders will build a ship and enter the market. When the U.S. ships move in, the waiver is lifted and the U.S. will protect that market under existing law. In this way, the rule would actually promote domestic shipbuilding by allowing other countries to highlight areas for growth while minimizing risks. Such a rule would also encourage efficiency and innovation without compromising or threatening existing jobs.
As President Lincoln said in his 1862 address to Congress “the dogmas of the past are inadequate to the stormy present.” The Arctic presents opportunities and challenges not seen by western countries since the days of Columbus. In times of crisis, we can, and should, look critically upon institutions fostered in a different time and for a different reason. The Secretary of Homeland Security recognized this crisis and granted a waiver for Nome. The Secretary should now do the same for the rest of the Arctic.
Independent commodity trader Trafigura Group, through its subsidiary Impala, is investing $1 billion in creating the infrastructure for a new multimodal supply chain in Colombia that can transport crude, naphtha, break-bulk cargo, containers, and oversized cargo up and down the country’s main waterway, the Magdalena River.
Impala Colombia currently operates a terminal in the seaport of Barranquilla, where the Caribbean Sea meets the Magdalena River. Some 630 kilometers south of Barranquilla on the Magdalena River, Impala is investing some $450 million in developing a new state-of-the-art inland river port in Barrancabermeja. The inland river port will have an oil terminal with six tanks that can store 120,000 bbls each and a general cargo and container terminal. The port will serve as an intermodal connection between river transport and truck transport. Impala’s fleet of barges will ship product to and from major crude oil production sites as well as major cities such as Bogotá or Medellin.
In addition, Barrancabermeja will also serve as a seaport with bills of lading possible to connect directly with international ports such as Rotterdam or Shanghai.
Part of Impala’s investment includes a fleet of new towboats and barges. Impala’s growing Colombian fleet includes at least 15 new towboats and 68 liquid barges and 45 dry cargo barges. The tank barges are double hulled, with vapor recovery systems for environmental responsibility and safety and can carry up to 10,000 barrels of oil.
This past summer, Eastern Shipbuilding, Panama City, FL, launched the Impala Soledad and Impala Puerto Salgar, the first two in a series of four inland river towboats for IWL River Inc., an affiliate of Impala Terminals Colombia.
Designed by CT Marine, the towboats are are being built to ABS Class Inland River Service. Eastern Shipbuilding expects to finish delivering the boats in 2017.
Impala Soledad and Impala Puerto Salgar along with the other sister vessels in the series, the Impala Mompox and Impala Catagallo, will each be 134 feet long, 42 feet wide, with a depth of 9 feet and minimal operational draft of 6 feet.
Each towboat will be triple screwed, with three Caterpillar 3512C main diesel engines, certified to IMO Tier II. Each will produce 1,280 hp at 1,600 rev/min for a total of 3,840 hp. Karl Senner, Kenner, LA, supplied the three Reinjtes WAF665 reduction gears.
The towboat’s auxiliary power is supplied by two Caterpillar C6.6 125 kW, 220-volt, 3-phase main generators.
The Panama flag vessel will be classed ABS +A1, Towing Vessel, River Service, +AMS, ABCU.
CT Marine also designed the towboats to have a retractable pilothouse. When fully raised, the pilothouse will have a 37 foot 6 inch eyelevel above the waterline. Towboats designed with retractable pilot houses can pass under low fixed bridges along their route. The deckhouse is confined to a single level and only the pilothouse is extended atop a hydraulic ram. When raised, the pilothouse provides excellent visibility for the master to see over top his tow.
NEW TOWBOAT FOR FMT
Another new towboat built with a retractable pilothouse was Florida Marine Transporters’ M/V Marty Cullinan. Built by Horizon Shipbuilding, Bayou La Batre, AL, the M/V Marty Cullinan has an ABS Load Line Certificate to operate in the waters between Chicago to Burns Harbor for fair weather voyages.
The 387 gt towboat is outfitted for service in areas with restricted overhead clearances and draft limitations. With the pilothouse fully retracted, the maximum air draft is 17 ft 8 in.
The 120 ft x 35 ft x 11 ft 6 in vessel is of all steel construction and powered by two Caterpillar 3512 engines, each rated at 2,011 hp at 1,600 rev/min with Twin Disc gears. The boat is outfitted with two 175 kV Tier 3 John Deer 6090 460 V gensets.
Sleeping accommodations and facilities are provided for eight persons and sound dampening systems have been implemented throughout the main deck house.
The towboat was built in 14 months. Project Manager Terry Freeman, who managed the construction of the vessel, said, “Our team exceeded all expectations with regard to the timely production and quality work on this build especially given the new design, ABS requirements and technical expertise required for the retractable pilot house.”
Jeff Brumfield, Senior Manager of Boat Construction and Engineering for FMT said, “We are thoroughly pleased with the boat, and when I talk to the Marty Cullinan crew they are quick to note that she is smooth and very quiet. The sound dampening package has exceeded our expectations.”
“We have worked hard to build one of the best boats on the river and we consider ourselves fortunate to have teamed with FMT and John J. Gilbert to do this,” said Travis Short, President of Horizon Shipbuilding. “Horizon has been building FMT boats for almost a decade and in that time we have been able to assemble a team of master craftsmen that produce a superior product. All the praise goes to those men and women in the yard, taking care to do the job right the first time while working safe, working hard and working together.”
Horizon has two more 120 ft FMT towboats, one standard and the other with a retractable pilothouse, in production with deliveries scheduled for this fall and the spring of 2017.
“LADY” KEEPS ON KEEPING ON
The M/V Lady Loren doesn’t have a retractable pilothouse, but does have a raised one that provides an eyelevel of 35 feet above the waterline. Back in 2008, LA Carriers built the pusher tug Lady Loren at Lockport Fabrication. At the launch, LA Carriers President Russell Plaisance explained that the boat was the result of five years of planning and a lifetime of maritime experience in the Gulf of Mexico. The 82 ft x 28 ft Lady Loren was the seventh boat in the LA Carriers fleet.
For Plaisance at the time, a key element of his business was diversification. “We do $10 million to $11 million [in gross revenue] per year including some business with the oil industry,” he said, “but we do a little of everything else as well. We barge pipe and we once even towed baseball dirt from Houston to Tampa Bay for spring training. This new boat has a contract to tow corn syrup from Memphis to Tampa Bay.”
Now eight years later, the corn syrup contract has dried up—the plant has been converted to other products. But LA Carriers’ diversity has kept the company healthy even during the current slump in the oil industry.
The Lady Loren, with both towing and pushing capabilities, is currently engaged moving a pair of hopper barges on a run between New Orleans and Tampa.
The Lady Loren is a triple-screw tug powered by three Cummins QSK19-M3 diesels rated at 660 hp each to give a total of 1,980 hp. The engines turn three 63 by 67-inch propellers in kort nozzles.
“The engines had 36,000 hours on them so I decided to rebuild the middle engine,” says Plaisance. “Without removing the engine, my crew, together with Cummins mechanics replaced the shaft bearings, pistons and rods, heads and injectors. When we looked at the wear on the parts that came out of the engine we realized that they could easily have given us another 4,000 hours with no risk of down time.”
As a result, he feels confident in leaving the rebuild of the two outside engines for another year by which time they will have a remarkable 40,000 hours each. Crediting Cummins quality, Plaisance also has a very proactive service and maintenance program on the engines. Oil is changed regularly, and injectors adjusted every 10,000 hours.
LA Carriers has changed some of the fleet in the eight years since the Lady Loren was first launched and they have several different engine makes among its seven boats. Plaisance is unreserved in his praise for the Cummins engines. “In future, if I have to replace an engine in one of my other tugs, it will be with Cummins,” he says.
SEPTEMBER 7, 2016 — Becker Marine Systems’ two managing directors, Dirk Lehmann and Henning Kuhlmann, had some good news to report at this year’s SMM event. “The Shanghai Waigaoqiao Shipbuilding shipyard in
Leading shipowners and operators, gas suppliers, ports, class societies, and technologists gathered last month in London to announce a new cross-industry initiative aimed at accelerating the adoption of Liquefied Natural Gas (LNG) as a marine fuel. The initiative hopes to address the issues of LNG bunkering infrastructure, regulatory concerns, and the higher initial capital investment costs in building LNG-fueled vessels.
Called SEA/LNG, the initiative brings together participants from Carnival Corporation & plc, DNV GL, ENGIE, ENN, GE, GTT, Lloyd’s Register, Mitsubishi Corporation, NYK Line, Port of Rotterdam, Qatargas, Shell, TOTE Inc. and Wärtsilä.
The goal of the initiative explains TOTE Inc. Executive Vice President Peter Keller, who is serving as SEA\LNG’s Chairman, is to address “market barriers and help transform the use of LNG as a marine fuel into a global reality.”
When it comes to using LNG as a marine fuel, TOTE is all in. It’s committed about $500 million in capital investments to have its entire fleet to burn LNG. The U.S.-flag operator has built two 3,100 TEU LNG-fuelled containerships now in operation between the Port of Jacksonville, FL, and San Juan, PR, and is converting the two ORCA Class Roll-on/Roll-Off ships in its fleet to burn LNG. The first of those two is being converted at Singapore’s Keppel Shipyard this fall.
TOTE is not alone in adding dual-fuel and LNG-Ready tonnage to its oceangoing fleet in the U.S. Harvey Gulf International Marine, Crowley Maritime Corp., Matson Navigation, Kinder Morgan, and SEA VISTA/SEACOR all have vessels in operation or under construction that burn or could eventually burn LNG as a marine fuel. In all, there are 29 vessels that are designed or could be converted to burn LNG as shown in the accompanying table. This does not include inland and coastal vessels such as towboats or ferries.
The U.S. Maritime Administration, for example, is supporting the conversion of a towboat to burn LNG as fuel.
The use of LNG as a marine fuel has increased with Emission Control Areas (ECAs) coming into force in Northern Europe and North America under MARPOL Annex VI. LNG is relatively clean burning, containing virtually no sulfur content and it produces lower NOx and particulate matter in the combustion process than fuel oil and marine diesel oil.
A long-time, well-known proponent of LNG as a marine fuel, John Hatley, PE, Gas Initiatives Wärtsilä North America, sees gas as a compelling solution for box feeders, RO/RO vessels, ferries and cruise ships, product tankers, Great Lakes vessels, and ATBs on short coastal voyages that enter into ECAs.
LNG is therefore able to offer a fuel solution compliant with both current and anticipated future regulations.
The larger effect from Annex VI will come when the requirement to reduce sulfur content of marine fuels to 0.5% on a global basis effective 2020 or 2025 depending on the outcome of an IMO low sulfur fuel availability study to be completed in 2018. The issue for ship owners and operators is how to find alternatives to economically meet the low sulfur fuel mandate about to be imposed by MARPOL Annex VI.
However, while LNG is a competitive fuel relative to current alternatives, LNG infrastructure is needed in ports around the world to enable quick, safe and cost effective bunkering. In the U.S., the first LNG bunker transport barge with GTT Mark III Flex tank technology is under construction at Conrad Orange shipyard in Orange, TX, and expected to be delivered in early 2017. LNG bunkering infrastructure is far more advanced in Europe.
“Everybody is calling for alternatives to reduce environmental impacts says Philip Olivier, CEO of ENGIE Global LNG. “That’s why we have joined forces to actively promote LNG as a key fuel in maritime transport. LNG has the potential to take a 10% market share of global bunker demand by 2030. ENGIE will contribute to achieving this target.”
Tom Strang, Senior Vice President, Maritime Affairs, Carnival Corporation & plc, says, “By working together proactively across the whole marine LNG value chain we can make the transition to a lower emission marine sector a reality.”
Lauran Wetemans Shell’s general manager downstream LNG agrees. “To make the transition to LNG as a fuel happen it needs close collaboration with key players across the full value chain,” says, Wetemans. “SEA/LNG aims to promote the benefits and potential of LNG fuel, and create a level playing field for LNG with other fuels. It will complement the work being done by other organizations like the Society for Gas as a Marine Fuel.”
Leo Karistios, Gas Technology Lead, Lloyd’s Register, points out, “LNG fuelled shipping has mainly been for the visionaries and, until now, concentrated in specialist ship sectors: short sea shipping and ferries, mainly sailing between two fixed ports. We want to help drive the expansion of LNG as a marine fuel of choice, with not just more short sea and local ships burning gas, but also the deep sea trades.”
Timo Koponen, Vice President, Flow & Gas Solutions, Wärtsilä Marine Solutions, says his company will contribute “its vast experience and know-how in gas driven propulsion systems and the entire gas value chain” to the initiative. “By working together, we plan to overcome the challenges and speed the general acceptance of LNG. Having been a pioneer in the use of LNG as a marine fuel, and a developer of major technologies facilitating the adoption of LNG fuel, it is natural that Wärtsilä supports wholeheartedly the aims of the SEA/LNG coalition.”
Developing bulk carrier concept
Wärtsilä is also involved with an effort with class society ABS, Arista Shipping, Deltamarin, and GTT in the Project Forward joint development project (JDP) to develop a dry bulk carrier concept that employs LNG as fuel.
The goal is to develop a Kamsarmax bulk carrier design to be the first of this type suitable for worldwide services powered by LNG in compliance with the IMO’s Energy Efficiency Design Index 2025 standards, NOx Tier III and MARPOL Annex VI SOx emission levels. This landmark design will be the first LNG-fueled cargo ship capable of full-range operations.
“The long-term potential for LNG as a marine fuel is tremendous,” says ABS Vice President of Global Gas Solutions Patrick Janssens. “We see the near-term opportunities for larger vessels on fixed and known trade routes, but more opportunities will emerge as concepts mature and bunkering infrastructure expands. Environmental stewardship will continue to be a concern, and owners will be evaluating alternative fuel choices.”
“Project Forward represents a milestone for the shipping industry in bringing to the market a practical, achievable design for what are the workhorses of the shipping fleet,” says Arista Shipping Principal Alexander P. Panagopulos. “Our mission is to develop the next generation of energy efficient and environmentally friendly dry bulk cargo ships to be sustainable worldwide beyond 2030. It marks a number of ‘firsts’ and draws together the experience of a team of leaders in their field to make LNG powered shipping a reality on the high seas.”
Technical challenges in developing this design were considerable, as there is a need to carry a large volume of LNG (2,500 m3) – which corresponds to full-range operation and 40 days – in a type of ship where available space is limited and cargo space is at a premium.
ABS will provide Approval in Principle (AIP) for the concept, which is based on the highly optimized Deltamarin B.Delta 82 design, utilizing a GTT membrane LNG fuel tank. This design also could be applied to other bulk carrier sizes and serve as the basis for an LNG-fueled tanker. The concept features a Wärtsilä four-stroke, medium-speed engine without auxiliary generators, the first time this configuration has been applied to a vessel of this type, significantly simplifying the vessel’s engine room arrangement and contributing to lower capital expenditure.
Read more from our Green Technology & Sustainable Shipping section in our Digital Edition.