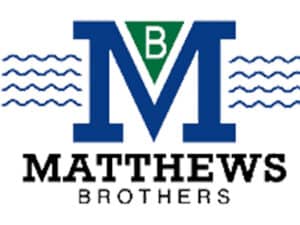
Stevens Towing shipyard keeps busy
Written by Marine Log Staff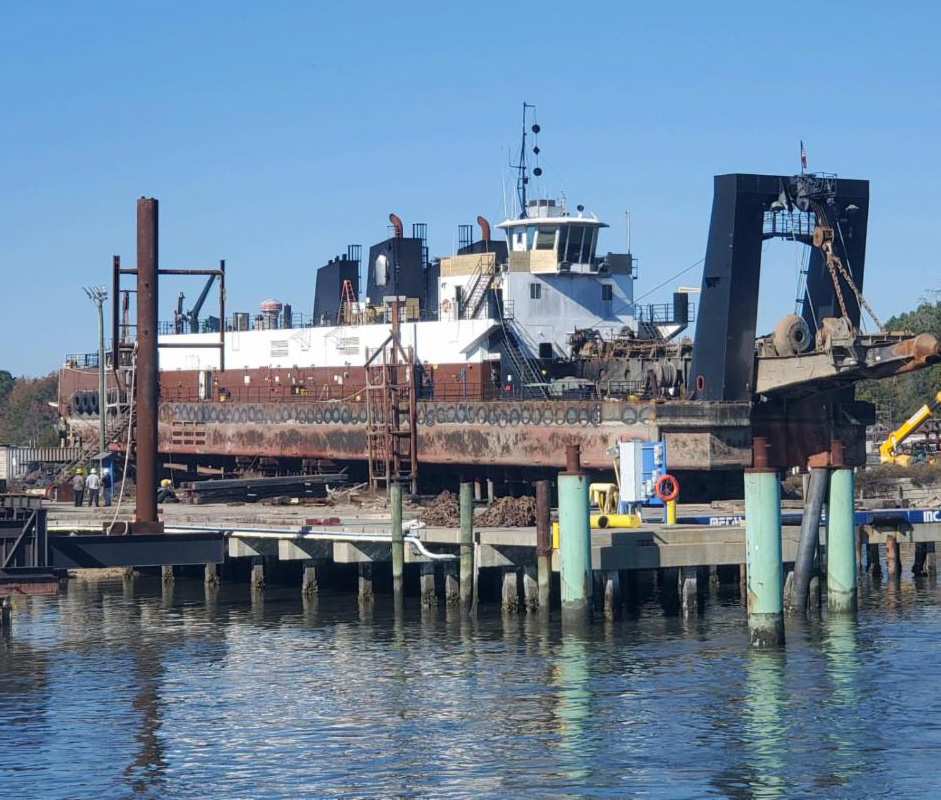
Drydocking of 1,745 ton cutter suction dredge has been major project underway at Stevens Towing’s Yonges Island shipyard,
Yonges Island, S.C.-based Stevens Towing reports that the fourth quarter of last year was a very busy period for its shipyard, with work split between between topside repairs and several drydockings.
Top side work ranged from ABS steel repairs on dump scow barges, installing a lube oil tote and discharge system on the deck of a fuel barge, electrical overhauls on drag barges, hydro testing, and repairing fuel lines on a fuel barge being used for the Charleston Harbor deepening project.
Drydocking projects in the quarter included hauling and repairing two 120- by 35-foot rock barges, a 200- by 72- by 10-foot crane barge, a 70-foot aluminum hulled Charleston Harbor tour boat, a 140- by 39- by 9-foot deck barge, an aluminum crew boat, a 260-foot hopper barge, a 74-foot Sub Chapter M tug boat, and a 293- by 49- by 11-foot cutter suction dredge.
DREDGE DRYDOCKING
The most extensive project of the quarter has been the drydocking of the 1,745 ton cutter suction dredge. A project of this scale required the majority of our workforce in the shipyard to work two12-hour shifts with roughly 70 personnel onboard the dredge. Trades collaborating include ABS ships fitters, welders, pipe fitters, pipe welders, electricians, UHP water blasters, sand blasters, crane operators, riggers, tank cleaners, scaffolding personnel, mechanics, outside machinists, and safety mangers.
On arrival, the initial focus was to remove the walking spud carriage which was picked up by the shipyard’s Clyde 32, 150-ton floating crane. The spud carriage was placed in Stevens Towing’s North Yard, and the structure was blasted for inspection.
After inspection, the scope of the project was defined to include rebuilding the trunnion assembly, bogie assembly, spud clamp assembly, spud carrier longitudinal operating cylinder and respective clevis plates, spud carrier vertical cylinder, sheave pendant and containment well.
With the spud carriage removed, the dredge was drydocked on the yard’s 1,800-ton railway.
BLASTING AND PIPE REPLACEMENT
“At this point in the project,” reports the company, “we have blasted from bottom shell to the top of the second deck using a combination of both UHP waterjet blasting and sand/slurry blasting. The house and ladder have been sweep blasted and the main deck and hull of the dredge were blasted to a commercial blast standard.
“In conjunction with the blasting department, our pipe shop has tackled some major pipe replacement projects which include over 420 feet of pipe ranging from 2 inches to 26 inches.
“The hull shop has removed all of the fendering from the perimeter of the barge and begun to tackle ABS and USCG call outs. Call outs include replacing portions of side shell plate, internal structural angle, brackets, channel, and some vent containment throughout the vessel. In addition, the customer has requested major steel overhaul repairs and improvements on the dredge house. We will replace huge portions of the main machinery space and engine room structure in way of the 26 inch discharge piping, where the heavy vibration has deteriorated the existing steel.
“The electrical shop is in the process of replacing roughly 30 outdated deck lights with Phoenix LED flood lights. This includes replacing the majority of the existing junction boxes and existing cabling. In addition to replacing light fixtures, Stevens Towing has been hired to test all alarms throughout the dredge. Once testing of the alarms is complete, we will update some of the outdated alarm panel with new Murphy panels.”