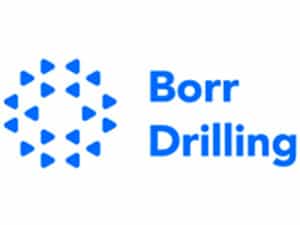
Schulte Group unveils next gen LNG bunkering vessel design
Written by Nick Blenkey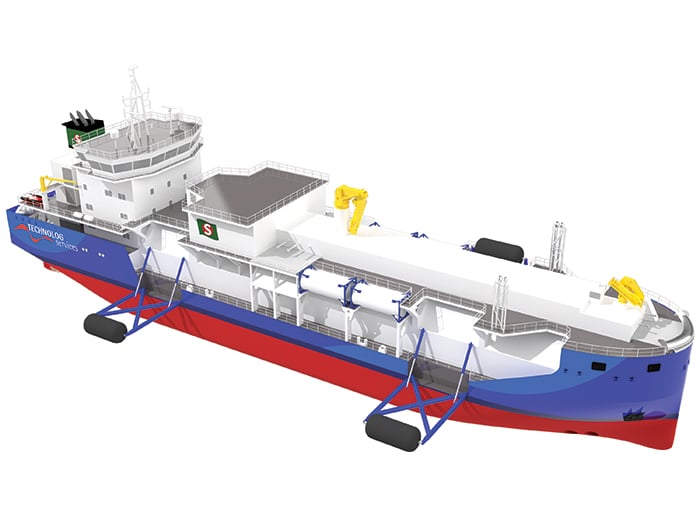
Schulte Group’s new LNG bunkering vessel design includes a patented outrigger fendering system that is compatible with any type of LNG-fueled client vessels and terminals. [Image: ©Schulte Group]
The Hamburg-headquartered Schulte Group has used the Gastech event in Milan to unveil a next generation design for an LNG bunkering vessel (LBV).
The group has used its experience as an LNG bunker vessel owner and operator to develop an LBV designed to be easy-to-use and to fulfill present and known future requirements for at-sea LNG bunker deliveries while reducing last-mile costs.
The design does away with the need for fenders and spacer pontoons, which take time and manpower to manually deploy, replacing them with an integrated outrigging system that’s compatible with any vessel type and can be operational in five minutes with the push of a button. The vessel’s telescopic crane extends over 40 meters over the water and can be adjusted to any required reach. The vessel fits with all known and soon-to-come LNG-fueled vessels.
The Schulte LBV also features warming-up, gas freeing and aeration equipment to prepare LNG-fueled vessels for drydock. Flexible design options mean that the LBV can be tailored to specific requirements. It can also be operated by a smaller crew while still maintaining high safety standards.
Schulte says that all of these components are geared towards reducing the CAPEX (capital) and OPEX (operating) costs for owners and operators, and ultimately will achieve low last-mile costs for the LNG-fuel industry, including the LNG-fuelled client vessels.
“We examined the market’s current requirements and recognised the need for a straightforward LNG fuel vessel that reduces the cost of last-mile delivery for vessel operators,” said Johan Lillieskold, gas solutions specialist, LNG Competence center, at Schulte Group in a Gastech presentation. “We have gone back to the drawing board and defined the operational specifications of what the ideal LNG bunker vessel should offer, doing away with any additional or unnecessary gear and cumbersome operations.”
The LNG bunkering vessel has been designed to maximize operational compatibility, including with vessels with structures protruding from the hull, such as cruise liners with protruding lifeboats, deck structure and balconies; vessels with short bodies such as high-speed, slender container vessels; those with high freeboards, including large crude oil and bulk carriers.
LNG is an increasingly popular choice of fuel as owners and operators seek to reduce emissions from their ships’ operations. Some of LNG bunkers are currently delivered from shore-based trucks to ships berthed alongside, and whilst these activities will still be available going forward, sea-based LNG bunkeringwill eventually dominate supply to merchant and cruise LNG-fueled vessels.
“The number of LNG-fueled vessels planned to enter into operation in the next few years is significant as operators increasingly turn to LNG to reduce environmentally and climate harmful emissions,” said Lillieskold. “The current arrangements for LNG bunkers, both land based and sea based, will not be sufficient or suitable for the increasing volume of LNG-fueled tonnage planned for future years. This new flexible vessel design will serve both today’s tonnage and future newbuilds.”
Schulte Group’s LBV has been developed in accordance with the International Code for Safety for Ships Using Gases or other Low-Flashpoint Fuels (IGC) Code and other IMO regulations. It also complies with and is prepared for new and future decarbonzation rules and regulations such IMO’s Carbon Intensity Index (CII) and the EU’s Fit-For-55 programs.
Measures that are either built into the design or available for future upgrade include a battery hybrid solution or a retrofit for hydrogen power. In combination with a battery hybrid solution and “green” shore power, depending on the operation profile, the vessel could operate largely carbon-emissions free, says Schulte.