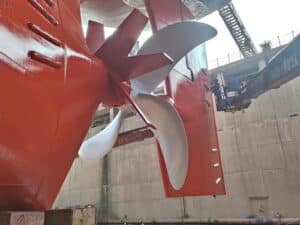
Coping With the Present, Looking to the Future
Written by Nick Blenkey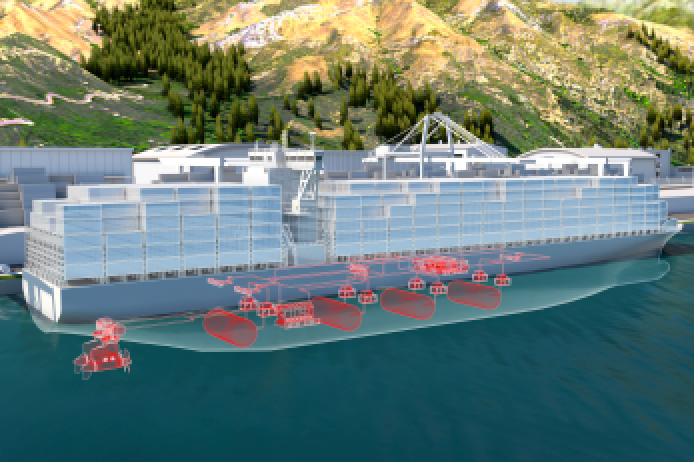
Fuel cells could play a key role in helping large ships meet decarbonization goals.
Buying Time With LNG
While LNG may not be zero carbon, it is arguably the cleanest currently available fuel delivering a significant reduction in GHG emissions. At the start of this year, according to SEA\LNG, there were 175 LNG-fueled ships in operation worldwide, excluding the 600 strong LNG carrier fleet, the majority of which are LNG-fueled, and over 200 ships on order. This is still a relatively small proportion of the world fleet, but a rapidly growing proportion of new ships on order is LNG fueled, with ever larger vessels such as containerships and bulk carriers being ordered as either LNG fueled or LNG ready.
This growth is likely to be beneficial to a specialist European suppliers, including Paris-headquartered GTT, hands down the world’s leading designer of LNG containment systems, which now offers a broad range of services related to LNG as fuel as well as cargo. Meantime, Wärtsilä has also carved out a significant niche in this area with its LNGPac, a complete LNG fuel gas handling system that includes the bunkering station, LNG tank and related process equipment as well as the control and monitoring system.
MAN Cryo, a Swedish-based subsidiary MAN Energy Solutions, has also been winning an increasing number of orders, including one booked earlier this year for the fuel gas supply system for two LNG-fueled icebreaking RO/ROs on order at China’s Yantai CIMC Raffles shipyard for Sweden’s Wallenius SOL.
Hydrogen
What about that other zero-carbon fuel, hydrogen? For the most part attention has focused on its application in fuel cells. However, it can also be burned in internal combustion engines and since 2017 Belgian shipping giant Compagnie Maritime Belge (CMB) has been operating a 16-passenger catamaran ferry powered by a liquid hydrogen fueled combustion engine. CMB has since partnered with ABC Engines to created BeHydro, a joint venture that focuses on the development, design and marketing of medium speed hydrogen combustion engines (monofuel hydrogen and dual fuel hydrogen-diesel). Commercial launch of BeHydro’s first hydrogen medium speed engine was planned to be in the course of 2020.
Most people, though, still see fuel cells as the most practical path to hydrogen application—and generally in smaller vessels. ABB, though, has its eyes set on larger vessels. It has signed a Memorandum of Understanding (MOU) with Hydrogène de France (HDF) to jointly manufacture megawatt-scale fuel cell systems capable of powering ocean-going vessels.
The MOU builds on an existing collaboration between ABB and Ballard Power Systems, a leading global provider of proton exchange membrane (PEM) fuel cell solutions and will be based on a megawatt-scale fuel cell power plant jointly developed by ABB and Ballard.
What’s Next After Zero-Emission Ferries
In the ferries sector in particular, with the help of clean, wind generated shoreside power, several Scandinavian operators have been moving on from battery-hybrid solutions to zero emissions, fully battery powered vessels. The next logical step is autonomous operation.
With the help of about $12.8 million in government funding, ASKO Maritime a subsidiary group of Norges Gruppen ASA, one of the largest players in the Norwegian retail segment, has signed contracts for construction and supply of two autonomous electric freight ferries, with an option for two more.
The vessels have been designed by Naval Dynamics Norway and incorporate Kongsberg Maritime systems. The 67 meter long vessels will initially be delivered as fully-electric transport ferries, powered by an 1,846 kWh capacity battery. After commissioning of autonomous equipment and field trials, they will operate as fully autonomous ferries able transport 16 fully loaded Standard EU trailers in one trip across the Oslo Fjord. They will be built to DNV GL classification and will be flagged in Norway. However, they will be built in India’s Cochin Shipyard.
Propulsion Solutions Go Electric
Whatever the source, power to push ships through water has to be delivered to a propulsion system—and European specialists in this area continue to refine their products. That means putting a lot of emphasis on R&D.
“As we’re concentrating on creating more efficient propulsors, we plan to lower mechanical losses and improve propulsion efficiency with high-quality propeller designs and by optimizing the shapes of underwater parts,” writes Jari Vanhatalo R&D Design Team Manager at Finnish propulsion specialist Steerprop in a recent blog post. “Our gear design specialists, technical analysts and hydrodynamists are working hard toward this end. As we create more efficient propulsion units, we are creating more environmentally friendly solutions, while also providing better returns through lower fuel consumption.”
The reliability of our propulsors is essential, says Vanhatalo. They are used in critical operations, where any interruption can cause huge losses.
“Our technical department makes lots of calculations, taking into account challenging conditions in both open and icy waters,” he writes. “For example, our gear designers look at different kinds of load cases so that the propulsor tooth contact patterns are ideal for every condition and situation.”
Like other propulsion specialists, Steerprop is responding to the increasing demand for electric drive systems and leveraging the advantage of in integrated permanent magnet (PM) motors that offers much better efficiency compared to a traditional induction electric motor.
The Voith Schneider Propeller: 90 Years Young
With growing demand for electric propulsion solutions, the Voith Group is pushing ahead with the continuous electrification of its proven drive technologies and has now launched an electric version of its well-known Voith Schneider Propeller (VSP).
The core principle of the VSP, the combination of drive and control in one unit, has been continuously developed and perfected over the last 90 years.
Among the advantages claimed for the new eVSP are high efficiency and the reduction of complexity. It uses a PM synchronous motor that is integrated in the propeller. The complete omission of gears reduces noise to a minimum and frees up critical space on the ship.
The drive system combines the technology of the VSP with over a decade of electrical know-how of the Voith Inline Thruster (VIT).
“With the electric Voith Schneider Propeller, we are making an important contribution to the electrification of the driveline in marine applications and thus to even more resource-saving shipping,” says Dr. Dirk Juergens, vice president of research and development for marine applications at Voith. “The new eVSP was developed for this purpose for all applications involved in the mobility revolution, such as offshore supply vessels, tugs and ferries.”
In addition, the eVSP offers ship operators future security through a high degree of flexibility in the choice of power generation (energy source) as well as low maintenance requirements thanks to its robust design.
The follow-up costs in operation and maintenance are thus significantly reduced, says Voith.
Schottel Retractable Rim Thruster
One of the latest developments from Spay, Germany-based Schottel is the Schottel Rim Thruster (SRT), an electric propulsion system in which the electric motor stator is installed in the outer part of the tunnel, while the propeller blades are attached to the inside of the rotor. This results in a space-saving and low-weight thruster. It converts electric power directly into propulsion power. Surrounding water permanently cools the electric motor, preventing it from overheating.
The latest variant is the Retractable Rim Thruster (SRT-R), covering the power range up to 500 kW, the SRT-R is able to cover a thrust radius of 360 degrees. This not only makes it more versatile, but also allows it to be optimally adapted to any requirement and operation profile, including DP operation or as a take-home device. In retracted position, no additional flow resistance is generated.