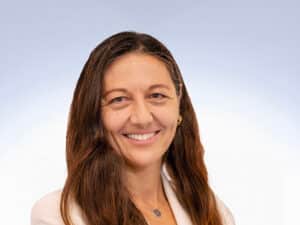
NTSB: Tanker engine problem led to $7.55 million hit on loading dock
Written by Nick Blenkey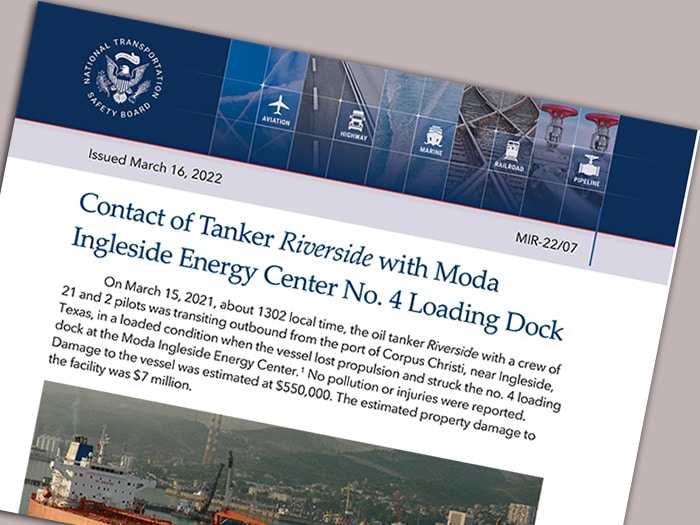
NTSB identified failure to properly address an engine problem as cause of incident
In another example of an engine problem resulting in a big bill, the National Transportation Safety Board (NTSB) has issued its report on a March 15, 2021 incident in which the 115,406 dwt Maltese-flag oil tanker Riverside made contact with a loading dock in the Port of Corpus Christi, Texas. Though no injuries or pollution were reported, the contact resulted in $550,000 in damages to the vessel and $7 million in damages to the dock.
The NTSB determined that the probable cause of the contact was was the ineffective evaluation and incorrect solution of a main engine starting issue by the vessel operator and the ship’s engineers.
Owned by Glory Riverside Navigation and operated by Thome Ship Management, the 820 foot, 2009-built Riverside was powered by a single slow-speed, two-stroke diesel engine, producing 18,184 hp and directly driving a single fixed-pitch propeller. The vessel’s maximum speed was 15 knots. To change the propeller direction, the engine had to completely stop and then restart in the opposite direction. The main engine could be started from three locations: the bridge, the engine control room, and locally at the main engine.
On the date of the casualty, two pilots from Aransas-Corpus Christi Pilots boarded the Riverside in Corpus Christi to assist with maneuvering the vessel out of the port. While outbound in the Corpus Christi Channel, another tank vessel ahead of Riverside was also departing. The pilots of both vessels agreed the Riverside would slow down and allow the other vessel to depart the dock and proceed out of the port. The pilot ordered a series of engine orders to slow the vessel, including stop; the Riverside began to sheer to port and a starboard rudder order was not effective. The pilot ordered dead slow ahead to increase the flow of water across the rudder, which required restarting the engine. The engine failed to restart on multiple occasions. Without propulsion, the Riverside’s maneuverability remained limited, and its port bow struck the mooring dolphin and catwalk at the end of the loading dock.
PREVIOUS ENGINE PROBLEM
The vessel had departed Brazil for Corpus Christi on February 16, and the crew encountered no problems with starting and stopping the engine. During the voyage, no issues were noted with the main engine.
The Riverside switched the main engine fuel supply to low-sulfur marine gas oil on March 11. On March 12, after arriving off the Corpus Christi (Port Aransas) coast at 5.48 a.m., the engine was secured, and the Riverside drifted while the crew waited for the pilots to arrive to take the vessel into port. After drifting for about 5 hours, at 10.30 a.m., the deck watch officer on the bridge attempted to start the main engine in preparation for entering port, but it failed to start. The chief engineer switched engine control to the engine room and successfully started the engine in ahead mode, but it failed to start in astern mode. The chief engineer started the engine again at the local control, but the engine rpm was too low for proper operation, so the engine was secured to troubleshoot the cause. During the crew’s evaluation of the engine to determine why it was not starting properly, they discovered that the chiller for the low-sulfur marine gas oil had not been put in operation, but after the chiller was put in operation, the engine still did not start.
After troubleshooting the engine start system, which included leak testing air control valves on the pneumatic start system and replacing two of them, the engine would start in the ahead mode but still would not start in the astern mode. The chief engineer contacted the operating company for advice. The company’s technician recommended to the chief engineer that the fuel rack position be increased in order to introduce more fuel to start the engine. However, the chief engineer decided it would be more effective to engage the limit cancel mode on fuel injection (a procedure not included in the engine’s instruction manual), which allowed 10% more fuel at engine start. At 3.55 p.m., when the chief engineer made the adjustment to the limit cancel mode, the engine started ahead and was successfully switched between ahead and astern modes. The chief engineer told investigators that no additional evaluation was conducted.
While the engine started successfully, both ahead and astern, the cause of the engine start failure was not properly identified or corrected, leaving the engine unreliable in responding to the maneuvering demands generally encountered while transiting within a commercial port. According to technicians from the engine’s manufacturer, the engagement of the limit cancel mode had no effect on the starting of the engine.
PROBABLE CAUSE
The NTSB determined the probable cause of the contact was the ineffective evaluation and incorrect solution for a main engine start issue by the company and shipboard engineers, overlooking the fouling of the main engine’s no. 6 air start actuator valve within the starting air distributor. Contributing to the casualty was the presence of moisture in and lack of routine drainage of the air start system, which allowed the buildup of hardened grease within the air start actuator valve.
LESSON LEARNED
On vessels with slow-speed diesel propulsion engines, starting and stopping main engines is a critical function for effective maneuverability. The NTSB has investigated multiple casualties involving slow-speed engine pneumatic starting and control systems and, in particular, air actuating valves within the systems. Vessel operators should ensure their crews are equipped with the resources and training to execute timely and thorough maintenance and repair on engines. If the root cause of an engine operating issue cannot be determined, it is critical for a chief engineer and vessel owner/operator to have a diesel technician further evaluate and determine the cause of the engine problem. Vessel reliability is dependent on the complete resolution of equipment malfunctions and abnormalities when they occur.
- As always, there’s much more detail in the full NTSB report