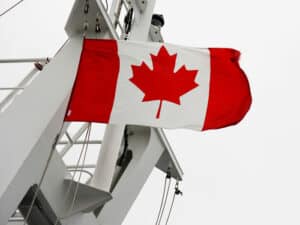
ABB reports turbocharger technology milestones
Written byABB Turbocharging reports significant developments with both its latest generation single stage turbochargers and its “Power2” two stage turbocharging systems.
The company’s latest generation of high efficiency, high pressure single stage turbochargers is the A100 series. ABB says that the A100 has set a new efficiency record. In final testing of the A190-L turbocharger for two -stroke low speed diesels,ABB technicians measured peak efficiency at 75.8 percent.
“The 75.8 percent figure is all the more impressive because it was measured on a turbocharger featuring a higher pressure ratio than the model that achieved the previous record figure,” notes Urs Gribi, Vice President of Engineering at the Baden, Switzerland headquarters of ABB Turbocharging.
In a second A100 landmark, ABB Turbocharging’s application engineers have devised a new A100-L turbocharger configuration for slow speed engines which facilitates rapid conversion from a higher power output matched to a ship’s normal cruising speed to a lower rating matched to a slower fuel saving speed – i.e. “slow steaming”.
The concept is devised to meet the “dual rating” engine specifications of a series of 10 containership newbuildings contracted by major Singapore-based containership operator NOL. It takes advantage of the very wide compressor maps of the A100-turbocharger to achieve this aim by varying the number of turbochargers in the engines’ exhaust gas stream rather than by fitting new turbochargers, modifying the internal components of existing turbochargers or using techniques like variable turbine geometry to vary turbocharger air delivery characteristics.
In detail, the ABB system adopted for the new containerships is designed to allow the ten, 12 cylinder 98 cm. bore low speed two-stroke diesel to achieve ratings of just over 72 MW at 104 rpm or just over 54 MW x 97 rpm.
The solution comprises four A190-L turbochargers, one of which can be cut-off from the exhaust gas stream. This is achieved either via a motorized valve or a simple blanking plate. In spite of the reduced level of energy in the engine exhaust gases due to the lower engine power rating, the A190-L’s wide compressor maps allow the three turbochargers still in the exhaust gas flow to efficiently produce charge air at the pressures and volumes needed for the lower engine slow steaming rating.
The compressor map is a measure of turbocharger performance that reflects how effectively and flexibly energy in the engine exhaust gases driving the turbine can be converted into compressed air on the compressor side. The A100 turbochargers combine very wide compressor maps while offering high pressure ratios of 4.7 and above in the A100-L versions for low speed two stroke engines and 5.8 in the A100-M and A100-H versions for medium and high speed engines.
“Substantially modifying the compressor map of a turbocharger can involve the exchange of many of its internal components,” notes ABB’s head of global turbocharger sales for the low speed engine segment, Arie Smits. “In the extreme case this can mean the turbine and compressor wheels as well as the nozzle ring and diffusers. In any event, the turbocharger has to be opened, dismantled and reassembled. But with the A100-L’s excellent compressor maps it was possible to achieve dual ratings with optimized fuel consumption by, essentially, only reducing the number of the turbochargers providing combustion air to the engines.”
POWER2
Having equipped the first gas engine to enter commercial service with “Power2” two stage turbocharging equipment, ABB Turbocharging has now carried out type testing on a Power2 system in the presence of the classification societies on a hot gas test rig at its Technical Center in Baden, Switzerland.
Power2 has thus passed a major milestone on its path to type approval for use on four-stroke, medium speed marine diesel engines.
The type test involved running a two stage turbocharging system consisting of a high and low pressure turbocharger connected in tandem on the hot gas test rig for one hour at its maximum operating speed and maximum operating temperature. Subsequently the turbochargers were dismantled and their components inspected.
Power2 two stage turbocharging technology is capable of producing pressure ratios as high as 8 and above. It is one of the major enabling technologies of strong Miller Cycles, which can substantially reduce emissions of oxides of nitrogen (NOx) from diesel engines, while also making possible enhanced power densities and fuel efficiencies.
On four stroke diesels it has been demonstrated that the pressure ratios produced by Power2 technology are high enough to achieve Miller Cycles capable of giving very high double digit NOx reduction percentages on four-stroke diesel engines. Simulations for Power2’s potential made by ABB Turbocharging’s development engineers using advance software indicate that, for example, the 80 percent reduction in NOx values vis-à-vis IMO Tier I required under IMO Tier III for ships operating in designated Emissions Control Areas (ECAs), is a prospect.
The Power2 two stage turbocharging system consists essentially of high pressure and low pressure turbochargers in tandem. On the compressor side they are connected via an intermediate air cooler which reduces the work second turbocharger needs to do and thus allows it to be more compact.
April 12, 2011
Leave a Reply
You must be logged in to post a comment.