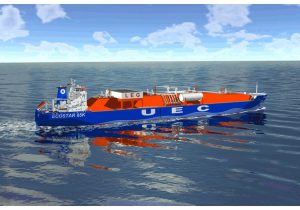
Nordic Technology Incubator
Tucked away in southwestern Finland is Salo, a town of about 50,000, where 40 percent of all the doors for large cruise ships are produced. Antti Marine’s production facility in Salo has produced a quarter of a million doors for 300 cruise ships in just over 20 years. It takes about 10 weeks to produce a typical order of 3,000 doors. They are supplied over a period of six months, as and when the ship’s cabins are built
“We are devoted to lean thinking,” says Commercial Director Markko Takkinen. “The production time of the doors is short, as we do not want them remain in storage here.”
Antti Marine specializes in what it calls ‘“tailored mass production”—necessary because on one cruise ship there may be 150 different types of doors.
Antti Marine is not the only Finnish marine company that benefits from many of the world’s large cruise ship fleet being built in Finland.
Cruise ships also have a lot of toilets and a need for a lot of waste management systems. Finnish headquartered Evac Group has just received its biggest cruise vessel contract ever: total waste management systems for four large cruise ships plus an option to outfit an additional six vessels. The initial four-vessel contract is valued at about EURO 30 million.
Each ship will have an Evac Cleansea wastewater treatment plan, allowing operation in Environmentally Sensitive Sea Areas (ESSAs) and Special Areas (SAs), dry and wet waste treatment systems, a bio sludge treatment unit, plus vacuum collecting systems and some 3,000 vacuum toilets.
Evac also supplies its products to a wide range of users ashore and afloat. So, too, does fire protection specialist Marioff Corporation Oy, but its roots are in the marine market and it last year launched a new generation Hi-Fog 3000 sprinkler series for marine applications that replaces earlier Hi-Fog 1000 and Hi-Fog 2000 sprinkler series.
“With the launch of this new generation of Hi-Fog 3000 sprinklers, we are offering to our marine customers enhanced Hi-Fog systems with faster activation, more efficient suppression and improved passenger and crew safety,” says John Hemgård, Director of Marine Business, Marioff Corporation Oy.
The Hi-Fog 3000 sprinkler series is designed, tested and type approved according to IMO Res.A800(19) as amended in IMO Res.MSC.265(84).
Another Finnish product that really took off after its widespread adoption is ABB’s Azipod. It’s become the propulsor of choice for cruise ships and ABB is currently delivering the complete electrical power plant and propulsion systems for two new 3,300 passenger cruise ships building at Germany’s Meyer Werft. The 20.5 MW Azipod XO propulsion unit for the first of the ships recently left the ABB factory in Helsinki.
ABB has delivered, or has on order, Azipod propulsion units for about 200 vessels
Each Azipod propulsion unit takes about two months for technicians to assemble at ABB’s Vuosaari plant. Across town at ABB’s Helsinki motors, generators and drives factory, the powerful synchronous motors at the system’s core take shape over six months.
COOPERATION AMONG STAKEHOLDERS
The major driver for marine engine designers is bringing engines into compliance with emissions requirements while keeping fuel consumption and maintenance costs under control.
A new pressurized EGR (exhaust gas recovery) economizer from Alfa Laval shows how Scandinavian maritime innovation often results from a cooperation between suppliers, university departments and shipowners. It also illustrates that, for some ships, EGR may be a better means of coming into compliance with new NOx limits than the better known SCR (selective catalytic reduction).
In a project supported by the Danish Energy-Technological Development and Demonstration Program (EUDP) and developed in cooperation with Aalborg University, the EGR economizer has been rigorously tested aboard the containership Maersk Cardiff.
“As a front-runner in the pursuit of green technologies, we were keen to see what the Aalborg EGR-HPE could do,” says Ole Christensen, Senior Machinery Specialist at A.P. Moller-Maersk. “But while we were enthusiastic about the boiler’s potential, we were also somewhat uncertain as how it would handle the physical realities of EGR. The temperatures are twice as high as those of traditional waste heat recovery, and the gas pressures are far greater.”
Those concerns disappeared when the boiler was brought online with the Maersk Cardiff’s two-stroke MAN B&W 6S80ME-C9 engine in November 2014. “Not only did the boiler survive,” says Christensen, “[but also] the results we have seen during testing are very promising.”
“EGR provides Tier III NOx compliance with a very compact footprint, but compliance itself is only part of the full potential,” says John Pedersen, Business Manager, Boilers, Combustion & Heaters at Alfa Laval. “Working closely with MAN Diesel & Turbo to optimize the EGR technology, we saw additional opportunities through our expertise in marine boilers.”
In the EGR process, around 30% of the exhaust gas is directed back into the engine, which reduces the combustion temperature and thus the production of NOx. Since only the remaining 70% of the gas reaches the traditional exhaust gas boiler after the turbocharger, waste heat recovery is reduced by 30% as well.
The Aalborg EGR-HPE is a revolutionary new economizer enclosed in a pressure casing that is placed in-line ahead of the pre-scrubber sprayers in the EGR circuit.
“By moving the break point for waste heat recovery from a medium engine load down to a low load, the Aalborg EGR-HPE enables even slower steaming,” says Pedersen. “That means fuel savings that quickly pay back the economizer, offset the EGR investment and lower CO2 emissions on top of the NOx reduction.”
Positioned ahead of the pre-scrubber spray jets, the Aalborg EGR-HPE has access to much higher temperatures than traditional exhaust gas boilers. It is integrated with the conventional waste heat recovery after the turbocharger by its steam drum, which is shared with the traditional exhaust gas boiler. With the output of the traditional economizer feeding into the shared drum, the Aalborg EGR-HPE produces extremely high-quality steam with a temperature of just above 400°C, bringing the waste heat recovery system to a much higher level of efficiency.
Using the Aalborg EGR-HPE in an integrated system allows waste heat recovery to occur at lower main engine loads than possible with a traditional waste heat recovery system in Tier III operation. This creates the possibility of even slower steaming.
“The EGR economizer makes waste heat recovery beneficial at far lower engine loads, down to around 30%” says Pedersen. “This means that vessels can steam even slower, with huge fuel savings as a result.”
DUAL FUEL
B&W in MAN-B&W stands for Burmeister & Wain and the Burmeister & Wain shipyard in Copenhagen built the Selandia, the world’s first successful diesel-powered oceangoing ship. That was in 1912.
More than a century later MAN Diesel & Turbo in Copenhagen is still on the cutting edge of diesel innovation.
One beneficiary of this is TOTE Maritime which opted for MAN Diesel & Turbo dual fuel technology for its two new Marlin Class, Jones Act containerships. Both of these ships have been delivered for operation between the U.S. and Puerto Rico, burning LNG as fuel and thereby meeting all U.S. SECA emissions requirement. Each is powered by the world’s first dual-fuel slow-speed engine, an MAN-B&W 8L70ME-GI, built in Korea by licensee Doosan Engine.
The technology in the ME-GI engines wasn’t just pulled out of a hat. It is a natural development of the MAN B&W low speed electronically controlled ME family of engines. The first testing of the GI principles was carried out in 1987 and MAN Diesel
& Turbo introduced its first two-stroke ME-GI dual fuel engine series in 2011, adding the ME-LGI engine series (which can burn liquid fuels such as methanol and ethanol) in 2013.
In theory, any ME engine can be converted into an ME-GI engine, but to be recognized by a classification society as “LNG ready” an ME engine equipped newbuild will have to be designed with provision for such things as the necessary LNG fuel tanks, piping and other ancillaries.
MEDIUM SPEEDS, TOO
LNG fueling has also proved an attraction for many operators of vessels with medium speed diesels who have to operate in emissions control area.
That trend sees Wärtsilä set to deliver the 100th Wärtsilä 34DF dual-fuel marine engine from the factory in early 2016. It is part of an order for three new large escort tugs under construction for Norwegian operator Østensjø Rederi by Spanish shipbuilder Astilleros Gondan. The tugs will operate at Statoil’s Melkøya terminal near Hammerfest in Norway.
“These 100 engines do not include those delivered for land-based energy generation applications,” says Lars Anderson, Vice President, Wärtsilä Marine Solutions.
“Within its power range, the Wärtsilä 34DF has become the workhorse of the marine industry, thanks to its superior reliability and lower operating costs. It is a highly efficient engine that is also making a notable contribution to environmental compliance,”
The Wärtsilä 34DF dual-fuel engine was upgraded in 2013 with a higher MCR (maximum continuous rating) and better efficiency than its earlier version, the first of which was delivered in 2010. The upgraded version has a power output range from 3,000 to 10,000 kW at 500 kW per cylinder.
ELIMINATE THE ENGINE?
Of course, if you can eliminate the engine and switch to battery power, that gets rid of emissions issues entirely. One area where this could be possible is in certain short range ferry operations and we have already noted the E-ferry way project under way in Denmark at Søby Værft AS.
Wärtsilä, too, is eyeing this niche. In January it launched a concept for a series of zero or low emission shuttle ferries. The concept has been developed in line with new Norwegian environmental regulations for ferries, and Wärtsilä says this regulatory trend is also evident in other countries.
The ferries are designed to run entirely on batteries or in a battery-engine hybrid configuration where the fuel options are liquefied natural gas (LNG) or biofuel.
In plug-in operation, the fuel consumption is reduced by 100 percent compared to conventional installations, and all local emissions are completely eliminated. With the plug-in hybrid configuration, emissions are reduced by up to 50 percent.
The concept features Wärtsilä’s new wireless inductive charging system, which offers major benefits for typical shuttle ferry operations involving 20,000 or more departures a year because of its time and energy savings. The system eliminates physical cable connections, thus reducing wear and tear and enabling charging to begin immediately when the vessel arrives at quay.
Wärtsilä has now signed an agreement with Cavotec SA to jointly develop a combined induction charging and automatic mooring concept. It would incorporate Wärtsilä’s wireless induction power transfer into a vacuum-based automated mooring technology in which remote controlled vacuum pads recessed into, or mounted on the quayside, moor and release vessels in seconds.
FILTER PROMISES TO CUT NOX
The Exilator, an environmental filter for smaller ships, able to reduce both sulfur, carbon monoxide, NOx and noise, has been successfully tested on a Danish Maritime Authority ship. The technology has been testing over a 12-month project phase followed by a three-month practical test of the concept on the Danish Maritime Authority’s ship Poul Løwenørn. The filter’s performance has been documented by the Danish Technological Institute, and the installation and mounting of the filter has been approved by LR.
The filter has been designed for ships with engines of up to 6 MW. Current regulations don’t require the cleaning of exhaust gas from smaller ships if they already sail on marine diesel with a maximum sulfur content of 0.1%. Still, developer Exilator ApS
believes that there is already a market for the filter, as it reduces soot pollution and NOx on the ship itself and also cuts engine noise considerably — particularly attractive in the yachting sector, or expedition vessels sailing in very sensitive nature areas.
According to the test from the Danish Technological Institute, the filter reduces soot particle emissions by 99,1%, carbon monoxide by 98% and NOx by 11%. Though those tests didn’t cover the filter’s noise reduction properties but the company expects a noise reduction up to 35 dB, including low frequency noise.
Financing for development and testing was secured through the Danish Growth Fund and investment & development company CapNova.
The filter works by catalytically incinerated the soot in the exhaust as soon the ship’s engines reach exhaust temperatures above 325 degrees C. Ash is accumulated in the filter, which means that the filters must be cleaned after about 5,000 operational hours, as part of the recycling process.
The filter requires that the ship uses marine gas oil with a maximum sulfur content of 0.1%. According the test, the filter improves the ship’s fuel consumption by around 1%.
The exhaust gas, after passing through the turbo charger, goes to a muffler that removes the deep resonance. Then comes the particle filter, which also serves as an oxidation catalyst, where the soot is captured and burned – and finally the gas is led through a reducing catalyst, which minimizes NOx and NO2, before being emitted into the atmosphere.
Development is now underway in a collaboration with DTU, the Technological Institute and an engine manufacturer aimed at increasing the filter’s NOx reduction from 11% to 40% in phase 1, and to 80% in the subsequent phase 2. When this is achieved, the filter will enable compliance with IMO Tier III NOx limits.
SCRUBBERS
Shipowners face no shortage of options if they decide to use exhaust gas scrubbers to cut sulfur emissions. Recent customers for Alfa Laval’s PureSOx exhaust gas cleaning systems include Buss Shipping, which is retrofitting hybrid PureSOx systems on two 1,025 TEU container feeder ships that operate exclusively in Emission Control Areas (ECAs). Since they frequent the low-alkalinity waters between Rotterdam and St. Petersburg, as well as ports like Hamburg with zero-discharge requirements, a scrubber with closed-loop mode was a necessity.
Each ship will receive a hybrid PureSOx system with multiple inlets, connecting the main engine and two auxiliary engines to one U-design scrubber. In contrast to earlier systems with multiple inlets, the inlets will now lead into a single scrubber jet section – an advance in construction that will make the scrubber even more compact.
“The PureSOx solution was well engineered and allowed a sophisticated integration of the scrubber system into our container feeder ships,” says Christoph Meier, Project Manager, Buss Shipping. “The custom construction let us avoid major modifications inside the vessel, which together with the pre-outfitting gave us a short installation time. All those factors contributed to a competitive price.”
Though there’s no doubt that scrubbers work, they also involve a substantial investment. That led Finland’s family-owned Langh Ship to develop a scrubber of its own, the decision was made a little easier by the fact that another family-owned company has 40 years’ experience in cleaning washing waters.
The resulting product was successfully tested over an extended period on one of Langth’s own ships, the M/S Laura, and received final class approval from GL in August 2014. All of Langh’s five vessels have now been fitted with the scrubber and last year a hybrid version was installed on Bore Shipping’s M/V Bore Song.
“It has lived up to our expectations: minimum sludge handling, very clean outgoing water and in that respect minimum impact on the environment,” said Jörgen Mansnerus, VP, Marine Management at Bore Ltd.
Scrubbers could become less expensive as the result of a pilot project developed by Norwegian University of Science and Technology (NTNU) researchers Carlos Dorao and Maria Fernandino.
Called the Lynx Separator, the technology now being examined for possible use in marine exhaust gas scrubbers was originally developed for use in the natural gas industry and involves using a steel sponge along with centrifugal force to remove the fluid from a gas stream, offering a brand new solution for the gas industry.
In the Lynx Separator, wet gas flows through the separator. A tubular metal sponge spins rapidly so the liquid is separated from the gas and thrown to the side and down, allowing dry gas to stream up to where it’s needed.
The Research Council of Norway’s Innovation Program MAROFF (Maritime activities and offshore operations) has now funded a pilot project to examine the possibility of applying the separator technology to cleaning ships’ exhaust emissions from ships andetheoretical calculations and testing show promising results
BALLAST WATER MANAGEMENT SYSTEMS
Another major focus of compliance concern for shipowners is, of course, ballast water management. Needless to say, most of the major players in the Scandinavian marine equipment sectors have horses in this race. It’s just to soon to pick any winners given the fact that no system has yet gained full U.S. Type Approval.
As this was written, Norway’s Optimarin was claiming to be on the brink of the coveted approval and was pleased when the U.S. Coast Guard told manufacturers of ultraviolet (UV) based BWMS that it will not accept the Most Probable Number (MPN) testing method in its approval process. The MPN methodology evaluates organisms on the basis of “viable/unviable,” with most UV systems depositing “unviable” organisms back into the water – meaning they are still alive but cannot reproduce. The USCG said that the FDA/CMFDA test, which judges life forms as “living/dead,” must be the standard for approval.
Optimarin says the decision is good news.
The Coast Guard has told UV system manufacturers that it will not accept the Most Probable Number (MPN) testing method in its approval process. The MPN methodology evaluates organisms on the basis of “viable/unviable,” with most UV systems depositing “unviable” organisms back into the water – meaning they are still alive but cannot reproduce.
“This is a clear indication to the industry that USCG wants absolute certainty with regard to standards – they do not want living organisms deposited in their territory,” comments Tore Andersen, Optimarin’s CEO. “MPN is acceptable for IMO, but that won’t be any consolation to shipowners with global fleets that want the flexibility of sailing in and out of U.S. waters.”
He says that Optimarin, which has over 20 years of industry experience and installed the world’s first commercial BWT system in 2000, is the only UV manufacturer that is currently within “touching distance” of USCG approval.
Its technology successfully satisied the FDA/CFMDA criteria during testing last year. Further tests in other water salinities are scheduled for spring 2016, after which point approval is expected later this year.
Andersen says the system’s power is the key to its efficacy. “Each of our system lamps has a 35 kW capacity, which is huge for a UV system. That power instantly kills invasive organisms and that’s exactly what USCG wants to see,” he says