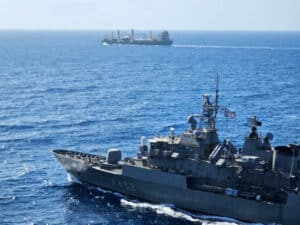
ABB adds to Azipod line
Written by Nick Blenkey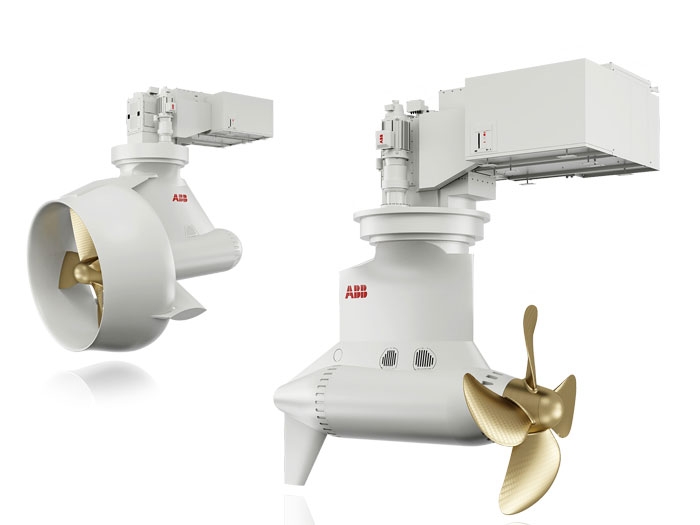
Azipod D is available in open propeller and ducted versions
MARCH 24, 2015 — ABB has expanded its line of Azipod electric propulsion systems. Its new Azipod D thrusters cover the power range from 1.6 MW to 7 MW per unit and require up to 25 percent less installed power. This is partly due to the fact that new hybrid cooling increases the performance of the electric motor by up to 45 percent.
Since its development in1987, the Azipod electric propulsion system, a streamlined steerable pod motor mounted below the ship, with the propeller connected directly to the motor shaft, has become the preferred propulsion system across a range of shipping segments. The unit power of Azipod propulsion systems is available up to 22 MW.
Today, the total power output of all installed and ordered Azipod units is more than 4,000 MW, which corresponds to the power consumption of Greater London.
The new thruster is appropriate for a wide variety of vessels including offshore vessels, merchant ships and special vessels. There are open propeller and ducted versions covering needs of both high thrust and high speed applications – and everything in between.
Azipod D features hybrid cooling system
“We’re excited to expand the Azipod propulsion family and make the benefits of electric propulsion available to a wider range of ships. Shipowners and operators demand solutions that are reliable and improve their competitiveness in a volatile market – the Azipod D is our answer to these demands,” said Peter Terwiesch, President of ABB’s Process Automation division.
ABB says that due to inherent simplicity and simple interfaces Azipod D installation is straightforward and minimizes assembly work at shipyard.
The gearless construction, high motor efficiency and advanced hydrodynamic design ensure fuel consumption that is typically 10-15 % lower than with geared thrusters. Simplicity also reduces maintenance.
Azipod D thrusters cover the power range from 1.6 MW to 7 MW per unit
Gearless construction means that wearing components like bevel gears are not needed and the number of such critical components as bearings and seals is minimized, to only 3 main bearings and 3 seals. Simplicity increases the thruster’s internal efficiency by about 3 – 6% compared to mechanical thrusters.
The electric motor is either a permanent magnet synchronous motor or an asynchronous motor. The use of a permanent magnet motor improves the efficiency by another 2- 10% depending on operation conditions.
The electric motor performance is increased up to 45 % by hybrid cooling using a combination of direct sea water cooling and internal air cooling. Without air cooling the thruster unit can still run up to 70 % load.
Higher efficiency is achieved by the superior hydrodynamics and flexibility in fitting the pod to the ship hull. Strut height is adjustable with free mounting angle max ± 6° both backward and sideways. The fin and large strut area recover rotational losses and improve course keeping. The electrical steering system is well proven in Azipod C and Azipod X thrusters.
The new hybrid cooling system allows a very high output torque which means improved hydrodynamic efficiency.
Maintenance and service access have been central considerations in the design of the Azipod D thruster. As a result, all preventive maintenance can be undertaken in dry-dock. Seals and shaftline bearings can be changed within 48 hours. Underwater mountable types can be swapped in 24 hours.
ABB says that as a result of the thruster’s robust design with minimized number of wearing components, the overhaul interval can be up to 10 years, depending on application.
Enhanced condition monitoring yields reliable information on the status of thruster components. This, says ABB, is a risk management tool that lifts predictability into the next level, supporting service needs by optimizing maintenance work over the whole life cycle of the Azipod D thruster.
Leave a Reply
You must be logged in to post a comment.