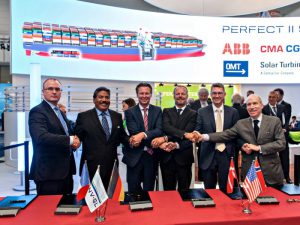
Piston free LNG container vessel project advances
SEPTEMBER 8, 2016—It was announced at SMM 2016 in Hamburg, Germany, that project partners GTT, CMA CGM (and its subsidiary CMA Ships) and DNV GL have joined with new project participants ABB,
SEPTEMBER 8, 2016—It was announced at SMM 2016 in Hamburg, Germany, that project partners GTT, CMA CGM (and its subsidiary CMA Ships) and DNV GL have joined with new project participants ABB,
SEPTEMBER 1, 2016 — Leaders from all parts of the global maritime industry will discuss the fundamental shift in the economy and new technological advances at the Danish Maritime Forum in Copenhagen
APRIL 20, 2016 — CMA CGM, COSCO Container Lines, Evergreen Line and Orient Overseas Container Line today signed a Memorandum of Understanding to form a new alliance enabling each of them to
DECEMBER 23, 2015—While he played a major role in the founding of the U.S., Benjamin Franklin was never this big in life. As we reported last week, the day after Christmas, the
1. ISLA BELLA, WORLD’S FIRST LNG-FUELED CONTAINERSHIP (pictured above)
TOTE Maritime’s 3,100-TEU containership Isla Bella was due to set sail for San Juan, PR, on November 24, marking the first time a ship in a Jones Act liner service will burn Liquefied Natural Gas (LNG) as a marine fuel. When the 764-foot-long Isla Bella transited the Panama Canal back on October 30 on her way to the Port of Jacksonville, Panama Canal Administrator/CEO Jorge L. Quijano called her “a true engineering feat.”
Among the principal maritime stakeholders involved in the successful launch of the Isla Bella and her sister Perla del Caribe are: owner and operator TOTE, shipbuilder General Dynamics NASSCO, designer DSEC (Daewoo Shipbuilding and Marine Engineering’s ship design arm), engine licensee MAN Diesel & Turbo, classification society ABS, and regulator U.S. Coast Guard.
The two Marlin Class containerships were contracted by TOTE in December 2012 and are being built at a total cost of about $375 million.
The 764-ft Isla Bella is equipped with the world’s first dual-fuel slow-speed engine, an 8L70ME-GI built by Korea’s Doosan Engine, under license from MAN Diesel & Turbo. With a 3,100 TEU capacity, the LNG-powered Isla Bella reduces NOx emissions by 98 percent, SOx emissions by 97 percent and CO2 emissions by 76 percent. The technology makes the ship one of the world’s most environmentally friendly containerships afloat.
During LNG will allow the Marlin Class Isla Bella to be fully compliant with strict emissions regulations while operating in both the North American Emissions Control Area and the U.S. Caribbean ECA.
At the time of her delivery, Kevin Graney, Vice President and General Manager of General Dynamics NASSCO, said, “Successfully building and delivering the world’s first LNG-powered containership here in the United States for coastwise service demonstrates that commercial shipbuilders, and owners and operators, are leading the world in the introduction of cutting-edge, green technology in support of the Jones Act.”
The moment is bittersweet for TOTE as it unfolds within the shadow of the tragic loss of the SS El Faro with all hands aboard during Hurricane Joaquin on October 1. The ship’s crew of 28 and five Polish nationals onboard were lost. The U.S. Navy, working with the National Transportation Safety Board (NTSB), has located the ship in waters 15,000 feet deep near the Crooked Island in the Bahamas.
The Isla Bella will be joined by the Perla del Caribe in Puerto Rico cargo service in the first quarter of 2016.
2. OHIO, LNG-READY PRODUCT TANKER
The 330,000 bbl Ohio was became the first product tanker to be built with the future consideration for the future use of LNG as fuel when it was delivered earlier this year to Crowley Maritime Corp. by Aker Philadelphia Shipyard, Philadelphia, PA.
The Ohio received American Bureau of Shipping’s (ABS) LNG-Ready Level 1 approval, meaning Crowley has the option to convert the tanker to Liquefied Natural Gas (LNG) propulsion in the future.
The Ohio along with her three ships being built at Aker Philadelphia are based on a proven Hyundai Mipo Dockyards (HMD) design which incorporates numerous fuel efficiency features, flexible cargo capability, and a slow-speed diesel engine built under license from MAN Diesel & Turbo. The 600 feet long Ohio is capable of carrying crude oil or refined petroleum products.
Crowley’s Seattle-based, naval architecture and marine engineering subsidiary Jensen Maritime is providing construction management services for the product tankers. Jensen now has an on-site office and personnel at the Philadelphia shipyard to ensure strong working relationships with shipyard staff and a seamless construction and delivery program.
“We are excited to offer our customers cutting-edge technology available in these new tankers, which not only embraces operational excellence and top safety, but also offers the potential to be powered by environmentally friendly LNG in the future,” said Crowley’s Rob Grune, senior vice president and general manager, petroleum and chemical transportation. “Adding these new Jones Act tankers to our fleet allows us to continue providing our customers with diverse and modern equipment to transport their petroleum and chemical products in a safe and reliable manner.”
3. NEW MINI TANKER FOR NY HARBOR
Blount Boats, Inc., Warren, RI, delivered the Chandra B, a new mini-tanker for American Petroleum & Transport, Inc., Miller Place, NY. The 79 ft by 23 ft, double-hull bunkering tanker operates in New York Harbor and New Jersey supplying fuel to ferries, dinner boats, dredges, and other vessels.
Propulsion power for the tanker is supplied by two EPA Tier 3-compliant Cummins Model QSL9, six-cylinder diesel engines rated at 330 hp at 1,800 rev/min with ZF Model W325 marine hydraulic gears that will have 4.91:1 reduction ratio. The self-propelled Chandra B is equipped with a 50 hp Wesmar hydraulic bow thruster, providing it with enhanced maneuverability.
Designed by Farrell & Norton Naval Architects, Newcastle, ME, the Chandra B is built to USCG Subchapter “D” specifications and is less than 100 gross tons. Farrell & Norton also designed one of the tank barges in American Petroleum & Transport’s fleet. The double-hull Chandra B will replace the 1979-built single hull Capt. Log in American Petroleum & Transport’s fleet.
American Petroleum & Transport (APT) has had to retire all of its single-hull tankers because of OPA 90 regulations.
APT vessels crisscross New York Harbor delivering ultra low sulfur diesel to clients such as Circle Line, New York Water Taxi, Great Lakes Dredge & Dock, and Sterling Equipment, as well as for the auxiliary engines of larger ships. The Chandra B has cargo fuel tankage is designed to hold a capacity of 56,450 gallons.
4. SAKIGAKE, JAPAN’S FIRST LNG-POWERED TUG
This past year, NYK took delivery of Sakigake, Japan’s first LNG fueled tug. Built at NYK’s wholly owned subsidiary Keihin Dock Co’s Oppama shipyard, the 37.2 m x 10.2 m Sakigake is operated by Wing Maritime Service Corporation, mainly in the ports of Yokohama and Kawasaki. Wing Maritime also operates the hybrid tug Tsubasa.
The Sakigake is equipped with two Niigata 6L28AHX-DF dual-fuel engines, each developing 1,618 kW. Propulsion is supplied by two Niigata Z-Pellers.
The DF engines can burn either LNG or diesel oil. The environmental advantages of operating on LNG as compared with conventionally powered tugs that use marine diesel oil is Sakigake emits about 30 percent less CO2, 80 percent less NOx, and no SOx.
While the project posed several challenges—the relatively small size and limited amount of space on the tug, and the large variation in engine power—Keihin Dock was able to achieve the desired level of environmental performance while maintaining the same hull form and steering performance of existing tugs. Keihin Dock worked closely with both Niigata Power Systems and Air Water Plant & Engineering Inc. to develop equipment for supplying LNG.
The project was supported by subsidies from Japan’s Ministry of Economy, Trade and Industry and the Ministry of Land, Infrastructure and Transport. ClassNK also provided joint research support.
5. JS INEOS INSIGHT, FIRST ETHANE-POWERED SHIP
Emblazoned on the JS Ineos Insight’s hull is the phrase, “Shale Gas for Manufacturing.” Built specifically to transport shale gas from the U.S. to Europe, the JS Ineos Insight is the first of eight 180m x 26.6m ethane gas carriers built by China’s Sinopacific for Denmark’s Evergas.
Named on July 14, the JS Ineos Insight can not only carry ethane, LPG or LNG, but can also burn ethane, LNG and conventional diesel in its two Wartsila 50DF dual fuel engines.
The eight Ineos ships will transport over 800,000 tons of ethane gas at -90°C per annum across the Atlantic from the U.S. to Norway and Scotland.
Classed by Bureau Veritas, the Dragon vessels were originally designed as dual-fuel LNG/diesel-powered vessels, with two 1,000 m3 LNG tanks on deck powering two Wärtsilä 6L20 DF main engines with a total output of 2,112 kW and two shaft generators with a total output of 3,600 kW power. The vessels will initially transport ethane from the U.S, to the U.K. Ineos refineries, the ability to also burn ethane was added to allow use of the cargo gas as fuel.
At the christening of the JS Ineos Insight and the JS Ineos Ingenuity, Ineos Chairman Jim Ratcliffe says, “Today is a landmark day for both Ineos and Europe. We have seen how U.S. shale gas revolutionized U.S. manufacturing and we believe these huge ships will help do the same for Europe. Ineos together with Evergas has commissioned eight brand new ships, accessed hundreds of miles of new pipeline and built two enormous terminals to get U.S. Shale gas to Europe. The scale of the whole project is truly breathtaking.”
According to Bureau Veritas Business Development Manager Martial Claudepierre, the ability to burn ethane and LNG as fuel in the Dragon Class ships “is a major step forward in the use of clean fuels.” He says that BV worked with Evergas and the Danish Maritime Authority to verify and ensure that the use of ethane is at least as safe as required by the IGC and will not impair the engine compliance with MARPOL Annex VI.
According to Claudepierre, using ethane required extra engine room ventilation and additional gas detection, plus modifications to the main engines including a lower compression ratio, different turbocharger nozzles and de-rating of the engine to cope with the lower knocking resistance of ethane. “But,” he says, “The gains in not carrying an additional fuel and in environmental performance from being able to burn clean fuel throughout the voyage are significant.”
6. MARJORIE C, NEW JONES ACT CONRO
Capable of carrying up to 1,200 cars and 1,400 TEU of containers, the Combination Container and Roll-on/Roll-Off (ConRO) vessel Marjorie C entered Jones Act service this year between the U.S. West Coast and Hawaii.
Built by VT Halter Marine, Pascagoula, MS, the Marjorie C was engineered from a proven design by Grimaldi at Croatia’s Uljanik Shipyard. The 692 ft x 106 ft ConRO has a draft of 31 ft, deadweight of 21,132.5 metric tons, with nine decks. It has a stern ramp capacity of 350 metric tons. The ship has a service speed of 21.5 knots.
The vessel’s design incorporates the highest level of operating efficiencies as well as reduced environmental impacts. The sister vessel, Jean Anne, was Pasha Hawaii’s first Jones Act vessel and has been serving the Hawaii/Mainland trade since March 2005. The Marjorie C entered into service this past May.
The ship is named in honor of Pasha Hawaii’s President and CEO George Pasha, IV’s grandmother, Marjorie Catherine Ryan.
“After more than three and a half years of planning and construction, we are pleased to unveil a ship that has been designed to not only accommodate the varying needs of our customers, but a vessel that minimizes our carbon footprint through extensive fuel consumption efficiencies and other green technologies,” said Pasha Hawaii’s President and CEO, George Pasha, IV. “With the addition of the Marjorie C we can now offer customers increased service and capacity between the West Coast and Hawaii trade lane on vessels providing superior reliability and cargo protection.”
7. NEIL ARMSTRONG, FIRST OF NEW CLASS OF RESEARCH VESSELS
This past Halloween, the first-of-class oceanographic research vessel R/V Neil Armstrong (AGOR 27) set sail from Dakota Creek Industries, Anacortes, WA, to San Francisco, CA, on its inaugural voyage. As we went to press, the Neil Armstong was waiting its turn to pass through the Panama Canal on its way north to the Woods Hole Oceanographic Institute in Woods Hole, MA. The ship will be operated by the Woods Hole Oceanographic Institution under a charter party agreement with Office of Naval Research (ONR).
Designed by Guido Perla & Associates, Inc., Seattle, WA and owned by the U.S. Navy, Neil Armstrong is 238 ft x 50 ft with a depth of 22 ft and draft of 15 ft. The first of two research vessels, the Neil Armstrong has four main 1,400 kW diesel generators, two 876 kW propulsion motors, and two controllable pitch propellers. The ship has a sustained speed of 12 knots and maximum speed of 12.8 knots.
The ship was classed by ABS Under 90 meter rules A1, Circle E, AMS, ACCU, NIBS, Ice Class D0, UWILD, 46 CFR Subchapter U, SOLAS (Oceanographic Vessels), MARPOL.
The Neil Armstrong’s sister vessel, the R/V Sally Ride (AGOR 28), is also under construction at Dakota Creek Industries.
During acceptance trials, Mike Kosar, Program Manager for the Support Ships, Boats and Craft office within the Program Executive Office (PEO), Ships, says, “The results of these tests and the outstanding fit, finish and quality of the vessel, stand as a testament to the preparation and effort of our entire shipbuilding team. It reflects the exceptionalism of AGOR 27’s namesake, Neil Armstrong.”
Neil Armstrong Class AGORS incorporate the latest technologies, including high-efficiency diesel engines, emissions controls for stack gasses, and new information technology tools both for monitoring shipboard systems and for communicating with the world. These ships will provide scientists with the tools and capabilities to support ongoing research including in the Atlantic, western Pacific and Indian Ocean regions across a wide variety of missions.
The lab areas include the main lab of 1,023 ft2, the wet area of 398 ft2, computer area of 311 ft2, and staging area bay of 303 ft2.
Neil Armstrong will be capable of assisting with integrated, interdisciplinary, general purpose oceanographic research in coastal and deep ocean areas. The vessel will operate with a crew of 20 with accommodations for 24 scientists.
8. BARZAN, FIRST OF NEW CLASS OF GAS READY BOXSHIPS
Recently named in a ceremony at shipbuilder Hyundai Samho Heavy Industries’ Mokpo, South Korea, shipyard, Barzan is the first in a series of six 18,800 TEU containerships ordered by Dubai headquartered United Arab Shipping Company (UASC). It is the first vessel to receive classification society DNV GL’s new GAS READY notation. Her five sister ships and eleven 15,000 TEU vessels of UASC’s newest eco-ship generation, will also receive the notation.
The ships have been designed and constructed to enable a quick and cost efficient retrofit to LNG fueling at a later stage. The GAS READY notation, with nominators (D, S, MEc, AEi) demonstrates that the vessel is in compliance with the gas fueled notation rules, that structural reinforcements to support the fuel containment system (LNG tank) have been verified (S), that the main engines installed can be converted to dual fuel (MEc ) and that the auxiliary engines installed can be operated on gas (AEi).
“We believe that this vessel, as well as the rest of the vessels in our new building program, demonstrates our commitment to technical innovation and eco-effectiveness,” says Jørn Hinge, President and CEO of UASC. “For UASC, achieving optimum efficiency levels is not a single initiative or project, it is a strategy and an ongoing commitment, and we will continue to work with DNV GL on the remaining newbuild vessels that have the lowest levels of CO2 output in their class.”
As well as being LNG ready, Barzan and her sister vessels incorporate several innovative energy saving methods, including a Siemens’ Siship SGM environmentally friendly drive and power generation system.
The Waste Heat Recovery System (WHRS) converts thermal energy from the exhaust gas from the main engines into electrical power to maximize the efficiency of the system.
The Barzan was expected to have an EEDI (Energy Efficiency Design Index) value that is close to 50 per cent less than the 2025 limit set by IMO, with a CO2 output per TEU that is more than 60 per cent lower than a 13,500 TEU vessel delivered just three years ago.
Barzan has been constructed to DNV GL class rules with the notations: 1A1 Container Carrier DG-P Shore Power E0 NAUT-OC HMON (A1,C1,G4) CLEAN BWM-T BIS TMON NAUTICUS (Newbuilding) GAS READY (D, S, MEc, AEi).
9. CROWN POINT, NEW GENERATION GREEN TUG
Tidewater Transportation and Terminals, Vancouver, WA, recently took delivery of the Crown Point, the first in a series of three 102 ft x 38 ft towboats being built at Vigor Industrial in Portland, OR.
The three towboats are the first new vessels to be built for the Tidewater fleet in 30 years, and are critical for the company to meet the anticipated rising customer demand on the Columbia-Snake River system. “The launching of the Crown Point, and the forthcoming Granite Point and Ryan Point vessels, marks an important step for Tidewater,” says Marc Schwartz, Maintenance & Engineering Manager at Tidewater. The vessels will strengthen our fleet, as well as reinforce Tidewater’s commitment to our customers, community, and environment.”
Tidewater operates the largest barge transportation and terminal network on the Columbia-Snake River system. The Crown Point joins the company’s current fleet of 16 vessels and 160 barges. Tidewater transports a wide range of cargo among a network of ports, terminals and grain elevators throughout the entire Columbia-Snake River system, which stretches some 465 miles of waterways. We also operate five strategically located terminals and five pipelines with key intermodal connections to railroads, highways and other pipelines.
Designed by CT Marine, Naval Architects and Marine Engineers of Edgecomb, ME, the Crown Point is an environmentally friendly tug with EPA Tier 3 compliant diesel engines that reduce air emissions and improve fuel efficiency. Main propulsion is supplied by two Caterpillar 3516C EPA Tier 3 certified diesel engines producing 2,240 bhp, each at 1,600 rev/min. The engines drive two 92 in. x 100 in. fixed pitch, stainless steel propellers through CT28 Kort Nozzles capable of a service speed of 8 knots. Operating in the Columbia River Gorge high winds, extreme currents and swells can be considered normal piloting conditions. That’s why the Crown Pount abd her sister towboats are fitted with an enhanced steering system using four steering and four flanking rudders was designed. The towboat has a wheelhouse with exceptional all-round visibility through full height windows, leading edge navigation and communications equipment, and enhanced accommodations for the captain and crew.
“During the last year and a half, a great deal of effort went into designing, engineering and building a towboat that would meet or exceed performance parameters,” explains Bruce Reed, Tidewater COO and Vice President. “With crew endurance being a priority, we employed Noise Control Engineers, Billerica, MA to develop a sound and vibration control package for the vessel. By incorporating Christie and Grey vibration control mounts and comprehensive acoustic insulation, noise levels register at less than 60 decibels in the accommodations during vessel operation.”
Other equipment onboard the Crown Point includes two C7.1, Tier 3 generators, rated at 480v, 200 kW at 1,800 rev/min. The generators are controlled through an automatic transfer system that ensures the vessel will recover from a generator power loss in less than 30 seconds. Deck machinery includes seven Patterson WWP 65E-7.5, 65-ton electric deck winches, with pilothouse remote operation and local push button control stations on the main deck. Each winch has Samson 1 3/8” Turbo 75 Synthetic Line.
In order to use the newest technology and minimize power usage, variable frequency drives were used in all major rotating machinery applications and LED lighting was employed in both interior and exterior lighting applications. The vessel is fitted with a Kidde NOVEC 1230 fire suppression system. Centralized fire detection and alarms cover both the machinery spaces and accommodations.
10. MULTRATUG 28, A HYBRID TUG
This past year, Netherlands-based towage and salvage specialist Multraship took delivery of Multratug 28, a Damen ASD 2810 Hybrid tug built at Damen Shipyards Galaţi, in Romania, as part of a fleet expansion program.
Classed by Lloyd’s Register, the hybrid Multratug 28 is 28.67m x 10.43m, with a maximum draft of 4.9m. The propulsion system includes two MTU 16V4000M63R diesel engines with one MTU 12V 2000 M41B propulsion genset of 800 kvA, 440V-60Hz. The battery pack are two 120 kWh. Two Rolls Royce US205 azimuth thrusters provide propulsion. The tug has a bollard pull of 62 tons, diesel direct speed of 13 knots, diesel electric speed of 8 knots, and battery pack speed of 4 knots.
The ASD 2810 HYBRID is developed to save fuel by 30% and to reduce emissions by 50%. To achieve this the vessel is provided with a propulsion system that can operate diesel-direct, diesel-electric or fully-electric. Fully-electric sailing on the batteries, with zero emissions and extremely low noise levels, is possible for time periods of up to one hour at a speed of 4 knots.
In June 2014, the first Damen ASD 2810 Hybrid was delivered to Iskes Towage & Salvage. Being green does not mean sacrificing power, the Bernardus still has a bollard pull of 60 tonnes. The Bernardus operates in the Port of IJmuiden near Amsterdam, the Netherlands.
“This hybrid tug is a unique concept,” says Dinu Berariu, Project Manager at Damen Shipyards Galaţi. “It features a diesel-direct, diesel-electric and battery powered propulsion system. This hybrid configuration will enable Multraship to lower fuel costs by up to 30 percent and emissions by up to 60 percent.”
Headquartered in the harbor city of Terneuzen, Multraship operates in the ports around the Scheldt estuary, in Zeeland seaports and the Belgian ports of Ghent and Antwerp, as well as the Bulgarian port of Burgas on the Black Sea.
Multraship’s fleet expansion program stems from its increasing customer base in the offshore sectors as well as growing demand for harbor towage services.
11. VASCO DE GAMA, FIRST 18,000 TEU BOX SHIP FROM A CHINESE YARD
As we went to press, the world’s third largest containership company, CMA CGM Group, Marseilles, France, was closing in on the acquisition of Singapore-based NOL, the world’s fourth largest. It successful, privately held CMA CGM would leapfrog over MSC to become number two in the world.
A big part of CMA CGM’s success is its investments in larger, more energy efficient tonnage to improve pricing and economies of scale. An excellent example is the CMA CGM Vasco De Gama delivered this summer to CMA CGM by China State Shipbuilding Corporation (CSSC).
With a length of 399 m and breadth of 54 m, the 18,000 TEU vessel is the largest containership in the CMA CGM Group and is the first 18,000 TEU containership to be built by a Chinese shipyard. CSSC is also building two more of the giant box ships, the CMA CGM Zheng He and CMA CGM Benjamin Franklin.
Flying the U.K. flag, CMA CGM Vasco De Gama is equipped with the latest environmental technologies including a latest generation main engine, a twisted leading edge rudder with bulb from Germany’s Becker Marine Systems and an optimized hull design. These innovations decrease the vessel’s CO2 emissions by 10% compared to the previous vessel generation. With an estimated emission of 37g of CO2/km for each container carried, the giant containership provides one of the world’s greenest goods transportation options.
The ship’s environmental footprint meets the 2025 energy efficiency regulations.
CMA CGM Vasco De Gama calls at 11 different countries on CMA CGM Group’s French Asia Line (FAL) service between Europe and Asia.
CMA CGM is also building three 20,600 TEU containerships—the largest yet built—at Korea’s Hanjin Heavy Industries. Those three ships will each have full spade twisted rudders (TLKSR) from Becker Marine Systems and Becker Twisted Fins. Both Becker products will make a significant contribution to the vessel’s efficiency improvement.
12. ESVAGT FROUDE, SPECIALIZED WIND FARM VESSEL
As of September this past year, Denmark’s ESVAGT had new owners; 3i Infrastructure and AMP Capital acquired the shares of A.P. Møller-Maersk Group and ESE-Holding. While ESVAGT’s primary market will continue to be oil and gas support and standby rescue in the North Sea, the company is broadening its portfolio with a push into the offshore wind energy market.
This past summer, ESVAGT entered the offshore wind industry with the christening of the world’s first purpose-built Service Operation Vessels at Siemens AG in Rostock and Hamburg, Germany.
The Service Operation Vessels (SOV), Esvagt Froude and Esvagt Faraday are each 83.7m x 17.6m, with a draft of 6.5m. Both of the Danish-flag SOVs were built in Norway by Havyard Ship Technology and are based on a Havyard 832 SOV design. The SOVs both have diesel-electric propulsion and DC power systems, enabling optimized fuel and energy efficiency and crew comfort. The service speed is 14 knots.
The SOVs are essentially “service stations at sea,” offering technicians a safe, efficient platform for wind turbine maintenance. Using the ship’s DP system, the ship can connect to wind turbines via its Ampelmann A-type Walk-to-work hydraulic gangway system offering a stable, safe platform to connect to the wind turbine.
Each offers accommodations for 60 people. The vessels are designed to reduce the level of vibration and increase the level of comfort for everyone onboard.
“As a supplement to the “Walk-to-Work” gangway, we have equipped the Service Operation Vessels with the newly developed ESVAGT Safe Transfer Boats (STB 7 and STB 12),” says Søren Nørgaard Thomsen, Managing Director for ESVAGT. “They are designed in-house based on more than 20 years of experience in boat development and more than 100,000 boat transfers. These boats will in a safe manner provide the industry with additional efficiencies and cost reductions.”
Each of the ships carry ESVAGT STB 7B Safe Transfer Boat, ESVAGT STB 12A Safe Transport Boat, ESVAGT FRB 15C Fast Rescue Boat.
A third ESVAGT SOV is on order and under construction at Havyard for delivery in 2016. The third ESVAGT SOV will service the 400 MW Dudgeon Wind Farm off the East Coast of England in the fall of 2016.
The vessel will later call at the Port of Oakland on December, 31.
CMA CGM Group Chairman and CEO Jacques R.Saadé made the decision to deploy an 18,000-TEU capacity vessel to the U.S.
CMA CGM will be the first carrier to call at a U.S. port with vessels of this size. It says it reflects its faith in the long-term growth potential of the U.S. economy and its commitment to increasing its U.S. market share.
A pioneer in deploying large-capacity vessels to the U.S., the CMA CGM Group has been working closely with the Ports of Los Angeles and Oakland to ensure there is sufficient infrastructure to support an 18,000 TEU vessel. It says it looks forward to working with other ports throughout the U.S. as they begin similar assessments of their infrastructure.
CMA CGM offers 23 shipping lines connecting the U.S. to the rest of the world and employs more than 800 people in the U.S. through its subsidiary CMA CGM (America) LLC.
The U.K. flagged CMA CGM Benjamin Franklin will be deployed on the Pearl River Express, a service connecting the main China ports, including Xiamen, Nansha and Yantian, with the U.S. West Coast ports.
The 399.2 m x 54 m vessel was delivered December 4 by shipbuilder Shanghai Jiangnan Changxing Heavy Industry Co., Ltd.
Singapore-based Neptune Orient Lines Limited (NOL) issued a statement on November 7 confirming that it is in “preliminary discussions with CMA CGM SA and A.P. Moeller-Maersk A/S with respect to a potential acquisition of NOL.”
Speculation that NOL, whose principle operating entity is APL, has been seeking a suitor has been rising since it announced a third quarter loss of $96 million, compared to a net loss of $23 million in third quarter 2014.
“NOL has a duty to assess all options to maximize shareholder value and improve its competitiveness,” said the November 7 statement. “From time to time, NOL enters into discussions on possible combinations involving NOL, while remaining focused on returning its core liner business to sustainable growth and profitability.”
It promised that “NOL will make an appropriate announcement in the event that there are any material developments” and advised shareholders investors to “exercise caution when dealing in shares in and other securities of NOL.”
The partners in the study — LNG containment system specialist GTT, containership operator CMA CGM (and its subsidiary CMA Ships) and classification society DNV GL — say the concept that has the potential to offer a more efficient, more flexible and greener box ship design than current 20,000 TEU two-stroke diesel engine driven ultra large container vessels.
They have dubbed the vessel the “Piston Engine Room Free Efficient Containership” (PERFECt).
Essentially, the concept ship takes advantage of the flexibility of electric drive to use space previously occupied by the main to carry cargo, more than offsetting the extra volume required by the LNG fuel tanks in comparison with conventional HFO tanks.
A comprehensive analysis with the DNV GL COSSMOS tool simulated components of the power production and propulsion system to analyze the COGAS system, making it possible to get detailed data for the calculation of the overall fuel efficiency for a complete round voyage.
Using a global FEM analysis, the project partners also evaluated the impact of the changes that were made to the general arrangement.
The two 10,960 cu.m LNG fuel tanks are located below the deck house, giving the vessel enough fuel capacity for an Asia/Europe round trip.
With the gas and steam turbines integrated at deck level within the same deck house as the tanks, space normally occupied by the conventional engine room can be used to increase cargo capacity significantly.
The dissociation of electric power generation from electric propulsion allows the electric power plant to be moved away from the main propulsion system, giving a great deal of flexibility. In fact, say the partners “an engine room is not needed any more.”
The three electric main motors, which are arranged on one common shaft, can be run fully independently of each other providing increased redundancy and reliability and a high level of safety.
With gas turbine-driven power production utilizing a very clean fuel as well as electric propulsion, the ship’s machinery systems will be simplified and more robust. This approach is also expected to lead to new maintenance strategies, already common practice in aviation, that would enable shipping companies to reduce the ship’s engine crew and save costs.
The study also suggests that optimizing the power plant through minimizing the steam turbine size, reducing power capacities, condenser cooling, and using a two-stage pressure steam turbine and steam generator will increase the system’s efficiency further. The next phase of the study aims to optimize the propulsion system and ship design to attain even greater efficiency and increased cargo capacity.
THE PRICE TAG
As part of the analysis, costs for additional and reduced systems to the base case ship (CMA CGM’s 20,000 TEU Marco Polo) were considered.Additional costs included:
Costs that could be eliminated or reduced in compared to the two-stroke engine system included:
At the end, the CAPEX (capital expenditure) for the COGAS ship are seen as being to be 20% to 24% above those for a conventionally-fueled vessel.
The OPEX (operating expenditure) costs largely depend on the difference in fuel price, the additional income related to the additional containers which can be transported and the savings related to a possibly higher system efficiency.
On the basis of the current gas price in Europe, which is nearly the same as the HFO price a business case in comparison with a two stroke ship using HFO plus scrubber as a reference therefore “needs compensation either by a larger difference between gas and LNG price or by additional benefits from efficiency improvement and additional revenue from additional container slots.”
Still, the partners say that the results of the feasibility study, including the CAPEX and OPEX calculations, encourage them to plan a more detailed evaluation of the overall system in a follow-up project.
October 13, 2015 — Hapag-Lloyd secures banking facility for boxship series at Hyundai Samho Heavy Industries (Extended coverage from Marine Log’s October 2015 issue). German container shipping giant Hapag-Lloyd signed a $
The U.K.-flagged Vasco de Gama has a length of 399 m and beam of 54 m.
Delivered July 27 (see earlier story) by China State Shipbuilding Corporation, it is thus largest containership ever delivered from a Chinese shipyard.
Bio-UV says it has been cooperating closely with a great number of partners, including the CMA CGM Group, in order to provide modular, reliable, innovative and energy saving ballast water management systems that are effective in all
water qualities.
The Bio-Sea system uses filtration and high power UV to treat ballast water without requiring any chemicals.