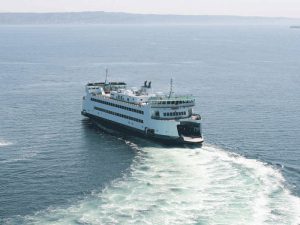
Double-ended ferries: The art of design
“Legally, a ferry is the continuation or prolongation of a highway over a navigable stream.” This quote is from the first Transactions of the Society of Naval Architects and Marine Engineers (SNAME), published in 1893. Given the impact of ferries upon society, it should come as no surprise that they have been a topic of interest to many naval architects for many years. The Pacific Northwest region of the United States contains a mix of islands, rivers, peninsulas and lakes. Salt water and fresh water transportation routes have been a critical part of the economic development of the region beginning with the native peoples and continuing today. Since the arrival of the first settlers in the 1850’s, power-driven ferries have been a common sight, linking the various communities through the movement of goods and people.
What is a double-ended ferry and why choose this configuration? A double-ended ferry is one where vehicles are loaded on and off both ends of the vessel and the direction of travel switches so the bow becomes the stern. The greatest argument for a double-ended ferry is when the route is short such as a river crossing. The time to maneuver the vessel so it can back in to the dock becomes a significant portion of the overall time between departures. The maneuvering time also consumes additional fuel and imposes the risk, however small, of any maneuver going awry. Another advantage is that the vessel will have the same handling characteristics every time it enters or departs a terminal. With its propulsion at each end, the double-ended ferry has excellent stopping power and superior maneuverability, especially if using an azimuthing or cycloidal propulsion system. This all contributes to safety, a critical factor for any ferry.
The origins of Elliott Bay Design Group (EBDG) go back to the late 1920’s with the establishment of W.C. Nickum & Sons. The earliest ferry projects were to modify the double-ended ferries from the San Francisco Bay area that were made superfluous by the bridge building activities there in the 1930s. Since that time EBDG has worked on a wide variety of vessel sizes and propulsion types, to suit routes ranging from short river crossings to 20 nautical mile transits of exposed water.
The typical ferry we have designed has a V hull amidships with a narrow, flat of bottom at baseline. The side shell flares outboard with one or two knuckles between the heavy guard at the deck edge and the bottom. This configuration produces surfaces that are fully developable which facilitates construction. Typically, the waterline beam is 80% of the maximum beam. This shape provides excellent reserve buoyancy for damage stability and adds waterplane area as the vessel heels, thus improving intact stability. Where there is a draft limit, we increase the width of the flat of bottom. At the ends the waterline shape typically narrows to a fine entrance. Because the waterline beam decreases more quickly than the beam at deck, the effect is to create substantial sponsons. These are located sufficiently far above the bow wave to avoid increased wetted surface as the bow wave increases with speed. The shape of these sponsons also needs to consider wave slamming in rough weather, so a compromise is sometimes required between calm water resistance and speed in waves. The lower part of the hull at the ends is fitted with a skeg to support the shaftline (with traditional shafting on centerline) and to support the hull in dry dock. The skeg shape and volume are critical to the shape of the bow wave, hence we carefully consider the section area shape, including skegs. In more recent projects we have seen greater emphasis on reducing hull resistance, especially for ferries that operate on route lengths of greater than 2 nautical miles. Over the 40 to 50 year life of a ferry, small reductions in drag can result in significant fuel savings, and of increasing importance, lower emissions. Through the use of computational fluid dynamics we can find a balance between low resistance and ease of construction.
The double-ended ferry lends itself to a wide variety of propulsion configurations. Historically, these have ranged from steam-driven, side paddlewheels to a cable ferry powered by horses on a treadmill. In more recent times, we have seen the diesel engine become the dominant power source with a variety of means of putting the power into the water. Clearly, there is no preferred approach that works for every ferry. As designers, we look for the machinery configuration that meets the owner’s performance requirements with the best balance between reliability, maintainability, fuel efficiency and operability. This search typically takes the form of a propulsion study where we work with the owner to establish weighting criteria for the various aspects of the propulsion system. Typically, an owner will have strong opinions on what equipment and what configuration works well for his operation.
We are also seeing more clients interested in different forms of propulsion to reduce their overall energy consumption and thus reduce their environmental footprint. Owners are willing to trade off the simplicity and reliability of traditional geared diesel propulsion for reduced energy consumption through use of hybrid propulsion with electric drives, batteries for energy storage, and smart control systems. We are also seeing increased interest in alternative fuels such as liquefied natural gas, biofuels, and even hydrogen.
This year EBDG developed a physics-based simulation tool to evaluate different propulsion technologies for different sizes of ferries operating on different types of routes. This tool calculates hull resistance, weights, fuel requirements, and hull characteristics in an iterative fashion until the basic parameters of weight and buoyancy are in balance. The outputs from the tool are estimates of capital and operating costs as well as carbon emissions. We can now work with ferry operators to assess the economics of using technology to reduce environmental impacts.
So, what has 50 years taught us? First is that there always will be opportunities to improve the art of double-ended ferry design. Some recent trends include:
- Access paths for passengers with disabilities
- Critical scrutiny of fire risk and improved design of both passive and active fire protection measures
- More vehicle clearances to improve speed of loading and unloading
- Large passenger cabins with accessible restrooms
- Seating arrangements to suit both individuals and larger groups
- Greater security for vital spaces such as the engine room and pilothouse
- Changing technologies and environmental issues are challenging to evaluate without a disciplined approach using solid engineering.