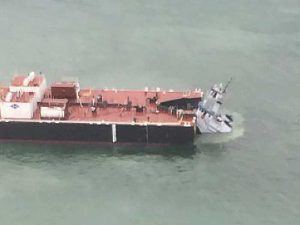
Canadian repairs to barge raise coastwise privilege question
JANUARY 4, 2017 — In addition to all the other problems Kirby Corporation faced when one of its ATBs ran aground in British Columbia waters in October (see earlier story) was that
JANUARY 4, 2017 — In addition to all the other problems Kirby Corporation faced when one of its ATBs ran aground in British Columbia waters in October (see earlier story) was that
DECEMBER 29, 2016 — Shipbroker Marcon International, Inc., Coupeville, WA, has passed a notable milestone. Over the last 35 years it has brokered 322 tugs for sales or charter, totaling 1,005,657 HP.
NOVEMBER 15, 2016 — GE Aviation’s marine gas turbine business has signed a multilateral memorandum of understanding (MOU) with several South Korean partners to cooperate in the joint development of LPG-fueled ferry
Anyone needing reassurance that the shipbuilding sector in the United States is alive and well need look no further than the Great Lakes. While yards along the U.S. Gulf reshuffle business strategies to help during the down oil market, yards along the Great Lakes continue to work on a number of projects, investing in infrastructure and leveraging partnerships to diversify portfolio offerings.
Perhaps the busiest group of all is Fincantieri Marine Group (FMG)—the U.S. subsidiary of one of the world’s largest shipbuilders in the world, Fincantieri. The Fincantieri Marine Group is comprised of three Great Lakes shipyards—Fincantieri Bay Shipbuilding (FBS), Fincantieri Marinette Marine (FMM), and Fincantieri ACE Marine (FAM).
Since acquiring the Wisconsin yards in 2008, Fincantieri has invested well over $100 million to build a shipbuilding group that will provide flexibility for its customers, and provide construction and repair services to both the government and commercial sectors.
Sturgeon Bay, WI-based Fincantieri Bay Shipbuilding (FBS), which is one of the last boat builders remaining in the Bay, has been essentially non-stop the last couple of years. The yard currently has numerous projects under various stages of construction with a backlog that extends through 2018. Most notably, the projects include newbuilds for one of the most active sectors in the country, the ATB market.
This past May, the yard delivered the Articulated Tug Barge (ATB) unit Barbara Carol Ann Moran and the 110,000 barrel ocean tank barge Louisiana to Moran Towing Corporation, New Canaan, CT. The unit was the third delivery to Moran under a 2014 contract.
The 5,300 HP, 121 ft ATB tug Barbara Carol Ann Moran is certified ABS Class +A-1 Towing Service, +AMS, and is equipped with state-of-the-art navigation and communications technology.
What made the delivery of the unit so impressive was that it was delivered on the exact day called for by the contract—emphasizing FBS’ high standards of meeting customer requirements, building a quality vessel and delivering on time.
Currently, FBS is under contract to construct two ATB tugs and two ocean going tank barges for Kirby Corporation; one ATB tug and one oceangoing tank barge for Plains All American Pipeline, LP; and one ATB tug and one oceangoing tank barge for AMA Capital Partners.
“We continue to be optimistic about the future of the industry we serve,” says, Todd Thayse, Fincantieri Bay Shipyard Vice President and General Manager.
To keep the momentum going, Fincantieri recently purchased the Palmer Johnson facility adjacent to the Bay Shipbuilding yard. Bay Shipbuilding has extensive expansion plans set for the 3-acre site, including the construction of new indoor Fabrication/Erection facilities, an indoor Blast and Coating building, outfitting shops and additional office facilities.
“This recent acquisition of the former Palmer Johnson facility has been well received by the industry and will allow us to pursue several new construction projects, which may include fishing vessels, ferries and landing crafts, while continuing to serve our core ATB market. These purpose-designed buildings will increase our overall output and capacity and improve our ability to meet critical schedules,” says Thayse.
“We will also be able to move more construction indoors which will allow FBS to further provide cost-effective solutions for our customers,” he added.
Indoor facilities will enable work to be ongoing for both newbuilds and repair work—especially during the winter months when Great Lakes fleet repairs are vital and time sensitive.
Earlier this year, FBS had 17 vessels at the yard undergoing winter repairs well into April. The vessels ranged from thousand-foot long bulk tankers, to medium-sized ships, to tugs and barges. Work included large-scale scheduled maintenance repairs, scrubber installations, repowering and structural steel renewal, in addition to electrical automation enhancement and ABS and U.S. Coast Guard inspections.
Additionally, Keylakes Shipping’s 768 ft bulk carrier John G. Munson is currently undergoing conversion at Bay Shipbuilding. The vessel is the tenth steam-to-diesel, or diesel-to-diesel repowering project that FBS has been awarded since 2009. The freighter, built in 1952 will undergo a complete repower at FBS. It is expected to undergo sea trials in 2018.
Meanwhile, FMG’s two other Great Lakes shipyards are busy constructing the next generation of warships for the U.S. Navy.
Earlier this summer, a keel laying ceremony was held at Fincantieri Marinette Marine, Marinette, WI, for the U.S. Navy’s 17th Littoral Combat Ship (LCS), the USS Indianapolis. The ship is one of six in various stages of construction at FMM, with an additional three ships in long-lead procurement. The yard has already delivered four LCS ships to the Navy—the USS Freedom (the lead ship in the Freedom variant), the USS Fort Worth, the USS Milwaukee and the USS Detroit.
The Lockheed Martin-led team is made up of Fincantieri Marinette Marine, along with naval architectural firm Gibbs & Cox, and more than 500 suppliers across 37 states. The U.S. Navy’s LCS construction program is divided between two groups—the Lockheed Martin team, building the Freedom variant, and the General Dynamics-led team, with Alabama-based Austal USA building the Independence class LCS.
Fincantieri Ace Marine, Green Bay, WI, also has a hand in producing the Freedom variant of the LCS. The yard, which specializes in the design and construction of high-speed coastal intercept and patrol vessels, most notably the builder of the Response Boat-Medium (RB-M) for the U.S. Coast Guard, produces the aluminum superstructures and additional aluminum components for the class.
To top off FMG’s three shipyards success, all three received the annual “Excellence in Safety” award from the Shipbuilders Council of America earlier this year. The award recognizes a shipyard’s commitment to safety, and the hard work and dedication put forth from shipyard employees.
The Great Lakes Group Eyes Expansion, Partners with Damen
FMG isn’t the only regional player seeking to further develop. This past June, the City of Cleveland authorized the sale of property adjacent to the Great Lakes Towing company headquarters. The acquisition of the property will enable the Great Lakes Shipyard, part of The Great Lakes Group, to operate at full capacity, all year round.
The expansion will include a 68,000 square foot facility that will accommodate a state-of-the-art 770-ton mobile Marine Travelift crane—the largest on the Great Lakes, and third largest in the world.
Great Lakes Group says that with the new facility in place, the Great Lakes Shipyard will be able to continuously provide all services for new vessel construction, as well as custom fabrication, ship maintenance and repairs.
Part of the services Great Lakes Shipyard will offer are those required for Subchapter M. Under Subchapter M regulations, towing vessels greater than 26 ft, or any vessel type moving dangerous or hazardous materials, must obtain a Certificate of Inspection documenting: Drydock inspection; Internal Structure Exam; Annual Inspection and Surveys; and Machinery and Electrical.
Just last month, the yard kicked off construction for the first Damen Stan Tug 1907 ICE. The tug is the first in a series of ten being built in compliance with the new Subchapter M regulations. The tugs are being built for The Great Lakes Towing Company (the Towing Company).
The tugs will measure 65 ft x 24 ft x 9 ft and will be powered by two MTU 8V4000 M54R engines generating 1,000 hp at 1,600 rev/min.
“This new construction program is further evidence of the innovative spirit the Towing Company has always embraced since its founding over 117 years ago, and reflects the commitment we have to our customers and the entire Great Lakes/St. Lawrence Seaway marine transportation industry,” says Joe Starck, President of the Towing Company.
Under the construction program two new harbor tugs will be introduced each year for the next five years—helping to stabilize operations and improve day-to-day business, assures Starck.
“The tugs,” he added, “will be ideal for the long-term sustainability of our harbor towing activities, and provide our customers with an even greater level of reliability, performance, and safety, across our entire Great Lakes service network.”
The Great Lakes Towing Company’s fleet provides ship assist, cargo transportation and logistics, ice breaking, and emergency assistance for every kind of vessel, barge and marine structure on the Great Lakes-St. Lawrence Seaway.
The Damen Stan Tug 1907 ICE are also the first tugs to be built in the U.S. under Damen’s Technical Cooperation program with Great Lakes Shipyard. The agreement, which was entered into at last year’s Workboat show, authorizes the Great Lakes Shipyard as an official builder of Damen designs for the next five years.
Burger Boat’s diverse portfolio
Since 1863 Burger Boat Company, Manitowoc, WI, has done everything in its power to meet the needs of its growing customer base. The boat builder, which has delivered countless vessel types in the range of 50 ft to 200 ft in length, implements what it calls a “lean” philosophy to its business practice, ensuring procedures are performed and completed on time, and vessels are delivered to customers on budget.
A builder of steel and aluminum vessels, Burger builds everything from yachts to passenger vessels, such as the 98 ft passenger vessel Chicago’s Classic Lady for Chicago’s First Lady Cruises—and patrol to research vessels, such as the 78 ft research vessel Arcticus which was delivered to the U.S. Geological Survey in 2014, just to name is a few.
Last year, Burger delivered a tour boat to Chicago-based Wendella Boats. The 340- passenger Lucia is an 89 ft steel vessel that was designed by Timothy Graul Marine Design, Sturgeon Bay, WI. The steel boat is certified USCG Subchapter K, and is powered by two Caterpillar C12 main engines and features two Northern Lights generators.
Most recently, Burger began construction on a custom 103 ft 6 in x 26 ft 5 in full displacement steel and aluminum Explorer Motor Yacht for an unnamed owner.
The expedition style motor yacht has a steel hull and aluminum superstructure. The vessel, designed by DeBasto Design, Miami, FL, will be launched Spring 2017. The ABS class yacht will be powered by two Cat C-18 ACERT main engines, and will be able to reach a cruising speed of 12 knots.
Fraser faces OSHA fine
Located in Superior Wisconsin, on the St. Louis Bay of Lake Superior, Fraser Shipyards, part of the Fraser Industries group which also includes boat builders Lake Assault Boats, provides full shipyard services from its sixty five acre site, featuring two dry docks and approximately 2,200 feet of berthing space. Since 1890, Fraser Shipyards has been a prominent fixture in the Twin Ports of Duluth and Superior, serving the Great Lakes shipping community. Most of its current 150 workers, 75 percent of which are structural welders, equipment operators, fitters and pipe fitters, are third generation employees for the company.
That kind of longevity and loyalty from workers can serve as a testament to Fraser’s commitment to the industry, the community and its employees, but recent findings have raised questions about the yard’s safety culture.
Last month, the U.S. Department of Labor’s Occupational Safety and Health Administration (OSHA) announced that sampling results taken during a recent retrofit determined that 14 of Fraser Shipyards workers were exposed to heavy metals and had lead levels 20 times higher than the exposure limit.
According to OSHA’s Assistant Secretary of Labor, Dr. David Michaels, “Fraser Shipyards accepted a contract with a very low profit margin and penalties for delayed completion, but could not meet the schedule without endangering its workers.”
That contract, from Interlake Steamship Company, Middleburg Heights, OH, was for the modernization of the Herbert C. Jackson. OSHA stated in its report that Fraser Shipyards’ management was aware of the presence of lead and asbestos throughout the 1959 built vessel. The ship arrived at Fraser December 2015 for a six-month retrofit project and was required back in operation for the summer iron ore shipping season.
In a statement, James Farkas, President and Chief Operating Officer of Fraser Industries, said “We are a family-owned company that has been in Superior for 126 years. We see all of our employees, laborers and contractors as part of the family.”
He added, “We take the health and safety of our people and our community seriously. We acted to protect our people as soon as we learned of the problem. We have worked with all of our employees, laborers and contractors to ensure their health by bringing in medical experts, as well as the highest levels of testing, protective equipment and safe operating procedures. We strongly disagree with OSHA’s statement that any of the issues were caused or worsened by business or profit motivations.”
The agency cited 14 willful egregious health violations for each instance of overexposing a worker to lead, and cited five additional willful violations for failing to conduct monitoring to assess lead exposure and failing to implement a lead compliance or respiratory program.
Additionally, OSHA issued 10 serious violations to the company, and placed Fraser Shipyards in its Severe Violator Enforcement Program (SVEP). For companies on the list, mandatory follow-up inspections become the norm.
Since the findings, Fraser has taken steps to help mediate the matter, and protect its employees. According to a statement, as soon as the management learned of the high lead levels it halted work on the Herbert C. Jackson. Fraser Shipyards also went on to engage medical experts from the region’s two leading hospitals, and industrial safety experts from the International Brotherhood of Boilermakers union to advise the company and oversee health testing. And it purchased state-of-the-art safety gear and equipment to protect workers.
Additionally, Fraser engaged medical professionals, OSHA and union officials to develop and implement new safety procedures.
“We appreciate their responsiveness to getting this issue fixed and taking care our members,” said Mark Garrett, Director of Health and Safety Services for the International Brotherhood of Boilermakers, the union that represents workers at the yard. “We don’t get many employers that step up like they did. They were straightforward, asked for our help and put in place our recommendations for safety.”
In total, Fraser could face close to $1.4m in OSHA penalties.
Vessel operators are still very much focused on reducing fuel consumption and lowering emissions. Collaboration early on in the design of a new vessel and its construction between the vessel owner, naval architects, shipbuilders, and propulsion manufacturers can payoff in optimizing the vessel’s hull, reducing costs of construction, and lowering operational costs during a vessel’s lifetime.
“We work with naval architects early in the design process to help optimize the propulsion system, looking to meet all design requirements while minimizing the size and horsepower of the system,” says Elizabeth Boyd, PE, President, Nautican Research & Development Ltd. Boyd says collaboration early in the design phase “can result in significant savings because if the horsepower can be reduced due to efficiency gains, it can lead to size reductions in not just the horsepower and propellers, but also everything that goes along with it—shafts, bearings, etc.—sometimes it can even mean meeting the requirements with a smaller boat. We can quickly show performance and full system configuration for different sizes, allowing the naval architect to explore options very quickly.”
Nautican’s foundation was built on efficiency. More than 40 years ago, company founder Josip Gruzling pioneered the use of hydrofoils to increase the efficiency of tugs and barges. Today, Nautican engineers and manufactures hydrodynamic solutions, including patented Integrated Propulsion Units, High efficiency nozzles and propellers, high aspect ratio triple rudders, pre-swirl stators, and also hydralift skegs for barges. It says independent tests show that its propulsion system solutions increase power and maneuverability, while significantly reducing fuel use and maintenance needs.
One of the Nautican’s latest projects is fabricating the first two sets of 104-inch nozzle units for the 120 ft Kirby Offshore Marine line haul tugs under construction at Nichols Brothers Boat Builders, Whidbey Island, WA.
According to Boyd, initially nozzle development was done using both Computational Fluid Dynamics (CFD) and physical testing in a cavitation tunnel and towing tank. “However,” she says, “our CFD efforts now are focused more on integration with the hull form. For these boats, CFD was not used as the design was already well developed and fairly straight-forward as far as placing the nozzles.”
The designer of the ABS Class tugs is Jensen Maritime, Crowley Maritime Corp.’s Seattle-based naval architecture and marine engineering company.
Each of the two tugboats will be equipped with two Caterpillar 3516C main engines, rated at 2,447 hp at 1,600 rev/min. Reintjes reduction gears, supplied by Karl Senner, LLC, Kenner, LA, will turn two Nautican fixed-pitch propellers with fixed nozzles. Other equipment onboard the tugs will include two C7.1 Caterpillar generators for electrical service, one TESD-34 Markey tow winch, one CEW-60 Markey electric capstan and one Smith Berger Town Pin.
“Kirby owns many boats with Nautican systems, but most of these have been ATBs (Articulated Tug Barge units) to date,” says Boyd. “We worked recently with Nichols on a pair of Kirby 10,000 hp ATB tugs—this project went very well and these vessels are performing exceptionally well in service.”
Nautican designed larger 120 inch nozzle units for another tug for Dunlap Towing. “Dunlap is a Nautican repeat customer,” says Boyd. The new tug, says Boyd is a new design, based on the Phyllis Dunlap, but “fully rethought and redesigned by Hockema Whalen.”
The 5,000 hp, twin-screw tug Phyllis Dunlap was built in 2001 by Hansen Boat Company, Everett, WA.
“Dunlap has been a great customer to work with—they are very involved in all aspects of the design and equipment selection and are very knowledgeable, providing some really useful feedback about performance over the years in their very demanding runs to Hawaii and Alaska.”
Wärtsilä Transverse Thruster
Earlier this year, Wärtsilä expanded its transverse thruster series with the addition of the Wärtsilä WTT-40, with a 4,000 kW power level and a 3,400 mm diameter controllable pitch propeller. While Wärtsilä has designed and built customized transverse thrusters as powerful as 5,500 kW, the WTT-40 and others in the WTT range address customer needs for high power transverse thrusters for bow and stern applications.
Development work on the Wärtsilä WTT-40 began in 2015 with an eye on targeting cruise ships, large OSVs and offshore construction vessels. The high power level is particularly important for the harbor maneuvering and docking of large ships, and for dynamic positioning of offshore vessels working in heavy sea conditions.
Because of its maximum power of 4,000 kW, shipyards and cruise vessel designers have the option of using three WTT-40 thrusters instead of four smaller ones. This translates into a more efficient vessel design with less space required for the transverse thrusters. It also allows thrusters to be installed closer to the bow where they are more effective.
Wärtsilä’s extensive experience with propeller design and tunnel optimizations using CFD analysis, ensures an optimal solution when it comes to propulsion performance, efficiency, and the minimization of noise and vibration.
Another benefit of the Wärtsilä WTT-40 is its integrated hydraulics, which save machinery room space and installation and commissioning time at the shipyard.
Innovative ship propulsion systems made by RENK
Military vessels such as patrol boats, corvettes, and frigates looking for “silent running” might well be interested in the Renk Advanced Electric Drive AED. The new drive from the Augsburg, Germany, plant offers a number of special advantages for shipbuilders, says Renk. The propulsion system is a real alternative to the heavy, space consuming electric motors that are rotating at propeller speed.
Modern power electronics allow the use of high-speed motors in combination with an efficient gearbox. The Renk AED combines electric motor and gearbox on one joint frame. Built on soft elastic mounts and equipped with a highly elastic propulsion coupling an incomparably silent operation is possible. The water-jacket of the water-cooled electric motor as well as the double helical reduction gear add to extremely low noise operation.
A modularized lightweight
Thanks to the compact design as well as the low height the preassembled unit is quickly installed with minimum space requirements. Additionally there is a considerable weight advantage. The drive weights around 40% less than a conventional direct drive motor. By comparison, the Renk AED weighs only 23 tons instead of the 35 tons of a direct drive motor of the same power.
Suitable for fixed pitch propellers as well as controllable pitch propellers the drive speed can be flexibly adjusted to the respective propeller requirements. The propulsion systems is built modularly and can be delivered in four sizes from 1.4 to 6 MW. For uses where the requirements are between sizes RENK simply adjusts the capacity of the bigger engine. In this way the complete range of capacities can be covered individually and economically. The motors work with low or mid ranged voltage and are designed –depending on size- for propeller revolutions of 190-450 rev/min.
Investing in new production & testing facilities
Besides pouring millions of dollars into research and development, marine propulsion manufacturers are also investing in new production and testing facilities. Earlier this year, Renk opened one of the largest and most modern test facilities in Europe for gear units at its headquarters in Augsburg. Whether for the shipbuilding, automobile or industrial sector: The multifunctional test facility is especially suitable for the testing of prototypes or special equipment. Renk will not only test its own special gearboxes and propulsion systems, but also those of other propulsion systems or propulsion component manufacturers. The test facility allows for a power capacity of up to 12 MW at 10 revolutions per minute and can take a torque of up to 11 million Nm.
Just this past June, Rolls-Royce Marine unveiled plans for a EURO 57 million plan to upgrade its azimuth thruster plant in Rauma, Finland, and consolidate its thruster assembly and testing to one site.
Rauma produces a wide range of mechanical azimuth thrusters for use on a wide range of applications including semi-submersible drilling rigs and drillships, tugs and offshore vessels. Rauma also produces thrusters for specialist vessels such as icebreakers and polar research ships.
Mikael Makinen, Rolls-Royce, President – Marine, says, “Our azimuth thrusters are one of our most important products, providing mission critical power and propulsion for some of the largest floating objects on the planet. To be able to make this significant investment in Rauma not only prepares us for future growth in this market, but is a vote of confidence in the capability and expertise of our people.””
Azimuthing thrusters rotate through 360 degrees, providing propulsion and maneuverability without the need for a rudder. The largest and most powerful thrusters from Rauma are the ARC type which power icebreakers including the Finnish vessel Fennica. They are among the largest products produced by Rolls-Royce and can each weigh up to 190 tonnes, providing 7.5Mw of power.
Two of the world’s largest floating structures are powered by another range of thrusters produced in Rauma, UUC underwater mountable thrusters:
The heavylift vessel Pioneering Spirit, owned by Allseas, which is used for decommissioning oil platforms, has13 UUC thrusters; and Shell’s Prelude, the world’s first floating LNG production facility, will feature three large UUC thrusters, for position keeping. The thrusters are installed in a novel arrangement that allows them to be removed and maintained within the ship.
The work to transform Rauma will begin immediately and is due for completion in 2020. The investment will include installation of a crane capable of lifting 200 tons, and at least six factory acceptance test rigs. Offices and IT systems will also be refurbished.
Engineering company GTT has more than 50 years’ experience in the design of membrane cargo containment systems, but one project underway right now in Orange, TX, is quite unique. That’s because it’s the first Liquefied Natural Gas (LNG) bunker transport barge in the United States.
One of 118 GTT projects currently underway worldwide, the tank barge is taking shape at Conrad Orange shipyard, Aziz Bamik, General Manager of GTT North America, told delegates at Marine Log Tugs & Barges 2016 Conference & Expo held last month in Seattle. While Conrad has decades of experience building all types of tank barges—dirty oil, products, chemicals, and LPG—this is the first time that it is building a vessel with one of GTT’s Mark III Flex membrane tank technology. Following a certification process, Conrad signed a license agreement with GTT back in January 2015 to construct the Mark III Flex.
Designed to operate in inland waterways, bays, harbors, and U.S. coastal waters, the new 2,200 m3 tank barge will be used to refuel TOTE’s two 3,100-TEU LNG-powered containerships. The barge will travel about a mile from its mooring facility to fuel the two Orca Class containerships, which operate out of the Port of Jacksonville, FL to San Juan, PR. The barge is designed not as an Articulated Tug Barge unit, but rather to be towed by hawser wire, pushed or maneuvered by hip, says Bamik.
In anticipation of increasing demand for LNG as a marine fuel, Bamik also mentioned to the conference audience that GTT North America was working with Conrad on a larger Articulated Tug Barge unit that will have a capacity of 4,800 m3, with two GTT Mark III Flex Cargo Containment System tanks. The 319 ft x 62 ft barge would have cold LNG delivery with onboard reliquefaction.
COMING DEMAND FOR LNG
The interest in LNG as a marine fuel seems to have waned in the U.S. with the drop in the price of oil. As of today, five vessels burn LNG as fuel in the Jones Act market. Besides TOTE’s two containerships, the Harvey Power, the third in a series of six dual fuel Platform Supply Vessels for Harvey Gulf International Marine, New Orleans, recently entered service in the Gulf of Mexico under charter for Shell. Next year, Crowley Maritime will take delivery of two Commitment Class Container Roll-on/Roll-Off (CONRO) ships for Puerto Rico. Those are being classed by DNV GL. All the other Jones Act LNG fuelled vessels are being built to ABS class.
Additional LNG Ready classed tonnage delivered or being built by General Dynamics NASSCO in San Diego and Philly Shipyard Inc. in Philadelphia could grow the LNG-fueled Jones Act fleet if converted in the future. TOTE is also converting its two Orcas Class RO/RO ships for Alaska service in Singapore.
Globally, there are about 77 gas-fueled vessels in operation and another 79 confirmed newbuildings as of March 2016, according to Anthony Teo, Technology and LNG Business Development Manager, North America, DNV GL. “There are about another 50 LNG Ready vessels have been contracted,” Teo told delegates. He said that DNV GL estimates there will be 360 LNG fuelled vessels in operation by 2020.
The widespread adoption of LNG as a fuel, Teo pointed out, was is being hindered by the lack of gas fuel bunkering facilities in ports.
A panel of naval architects, liquefied natural gas reliquefaction technology providers, and regulators discussed more in-depth the current hurdles hindering the expansion of the adoption of LNG as a marine fuel for the tugs and towboats in the Jones Act market.
Panelist Rafael Riva, Marine Business Development Manager, ECA, Lloyd’s Register pointed out that the technology was well proven in Europe. The first LNG tugs, for example, were built in Turkish shipyard Sanmar for Norway’s Bukser og Berging AS and have been in service for Statoil AS since 2014. The DNV GL class tugs are equipped with lean burn gas engines from Rolls-Royce and Rolls-Royce azimuthing thrusters.
The LNG powered propulsion systems does require more space. The Shearer Group’s Engineering Manager Joshua Sebastian, PE, mentioned the complexities of integrating the necessary fuel tank, piping, and control systems required to burn LNG on the smaller towboat platform. Sebastian’s company, naval architectural firm The Shearer Group, has been contracted for the conversion of a 65-foot-long conventional diesel-powered towboat to burn LNG.
LNG-powered tugs also require small volumes of fuel with a dedicated delivery solution. Fueling can be accomplished either via tanker trucks, shore LNG storage tanks, portable gas fuel tanks or ship to ship or barge to ship transfer.
Panelist John Dwyer, Officer in Charge, Marine Inspection/Chief, Inspection Division at USCG Sector Puget Sound, provided the regulatory view on the development of LNG as a marine fuel in the U.S.
The U.S. Coast Guard has issued a number of policy letters and guidance on the design and operation of ships using LNG as a marine fuel, as well as ships and facilities transferring LNG as fuel. The U.S. Coast Guard has addressed designs and facilities on a case-by-case basis.
Waller Marine’s Beau Berthelot pointed out that his company has worked on a number of refueling solutions. Waller Marine, for example, has been granted an Agreement in Principle (AIP) by ABS for a new liquefied natural gas (LNG) and regasification articulated tug barge concept. The vessel has the ability to load LNG from existing LNG terminals, liquefaction facilities or traditional LNG carriers and transport the LNG to existing tanks, traditional LNG carriers, trucks or marine vessels using LNG as a fuel. The barge also is equipped for regasification of LNG directly to a pipeline or to a power plant. An additional feature will be the use of natural gas as a fuel in the dual fuel engines of the tug to drive the tug-barge unit.
The benefit of the LNG Articulated Tug and Barge Regas Vessel (ATB RV) is that it allows LNG to be moved and delivered more efficiently on a small-scale basis in locations where large LNG infrastructure would be cumbersome, costly and time consuming.
Another possible solution for small footprint applications mentioned by panelists David Grucza, Director, Drilling and Marine U.S., Siemens, and Michael Walhof, Sales Director, Distributed LNG Solutions, Dresser-Rand, a Siemens company, was Dresser-Rand’s LNGo system is a modularized, portable natural gas liquefaction plant. This point-of-use production plant is a standardized product made up of four packaged skids: a power module, compressor module, process module and a conditioning module. The natural gas consumed powers the unit and is also used as the process refrigerant to eliminate complexity and maintenance.
SHIPYARDS CONTINUE TO BE BUSY
Meanwhile, U.S. shipyards continue to book orders for conventionally powered harbor tugs and Articulated Tug Barge (ATB) units. The continued orders for ATBs, in particular, are in response to transport refined products in the U.S.
Just last month, Gunderson Marine, Portland, OR, secured an order to build two 82,000 bbl, 430 foot-long oceangoing tank barges for Harley Marine Services, Inc., Seattle. The tank barges will be part of an ATB unit.
Gunderson last built a barge for Harley Marine in 2009. Construction on the barges will begin this year, with delivery of both vessels set for the second half of 2017.
As of press time, Harley Marine Services was negotiating with a Gulf Coast shipyard for the construction of the ATB tugs that would be coupled to the tank barges being built by Gunderson.
Over the past nine months, Gunderson Marine has delivered two 578 ft ATB oceangoing barges for chemical and oil service for Kirby Offshore Marine.
For its tank barges, Kirby Offshore Marine took delivery of two 10,000 hp ATB tugs from Nichols Brothers Boat Builders, Whidbey Island, WA. Speaking at Marine Log Tugs & Barges 2016, Nichols Brothers Boat Builders President & CEO Gavin Higgins said that ATBs enjoy several cost advantages over coastal tankers when it comes to moving refined products. Crew costs are far less, nine crew vs. 18 crew. Additionally, ATBs are more ship shape, offering speed advantages over towed tank barges.
The shipyard has also signed a contract with Kirby for two line haul tugs, as well as two 8,000 hp ATB tugs based on a design by naval architect Robert Hill of Ocean Tug & Barge Engineering. The companion tank barges are being built by Vigor.
FINCANTIERI BAY SHIPBUILDING
Fincantieri Marine Group’s Fincantieri Bay Shipbuilding (FBS), Sturgeon Bay, WI, has delivered the Articulated Tug Barge unit (ATB) Barbara Carol Ann Moran and the 110,000-barrel ocean tank barge Louisiana to Moran Towing Corporation, New Canaan, CT.
The 5,300-HP, 121-foot ATB tug Barbara Carol Ann Moran is certified ABS Class +A-1 Towing Service, +AMS, and is equipped with state-of-the-art navigation and communications technology. The Louisiana is 468 ft x 78 ft.
The ATB unit will work the East Coast of the United States and the Gulf of Mexico.
This is the shipyard’s third delivery to Moran under a 2014 contract, with a tank barge delivered in May of 2015, and another ATB—the tug Leigh Ann Moran and tank barge Mississippi—delivered December 1, 2015.
VANE BROTHERS SERIES AT ST. JOHNS
Vane Brothers, Baltimore, MD, continues to invest in new tonnage. It has a long running newbuild program at Chesapeake Shipbuilding in Salisbury, MD, where it is constructing a series of 3,000 hp ATB tugs and has now added the second of eight 4,200 horsepower tugboats from St. Johns Ship Building, Palatka, FL.
The new tug, Hudson, is the second of Vane’s Elizabeth Anne Class, under construction at St. Johns Ship Building. Lead vessel of the class, the Elizabeth Anne, was delivered in January, while the third in the series, the Baltimore, is set for completion this summer.
The new tug will be paired with the Double Skin 601, the first in a new series of 55,000 bbl barges and will be followed later this year by the Double Skin 602, both built by the Conrad Deepwater South Shipyard in Amelia, LA.
“Our ongoing fleet construction program ensures that we have state-of-the-art equipment available to service all of our customers’ needs with the utmost safety and efficiency,” says Vane Brothers President C. Duff Hughes.
Designed by Frank Basile, P.E., of Entech Designs, LLC, Vane Brothers’ Elizabeth Anne Class tugboats are close cousins to the Basile-designed Patapsco Class tugboats, 15 of which were produced between 2004 and 2009.
Measuring 100 feet long and 34 feet wide, with a hull depth of 15 feet, the model bow Hudson is powered by two Caterpillar 3516 Tier 3 engines, each generating 2,100 horsepower at 1,600 rev/min. Two John Deere PowerTech 4045, 99 kW generators deliver service power to the boat, while a third John Deere 4045 teamed with an Allison transmission drives the chain-driven Intercon DD200 towing winch. The Elizabeth Anne also has Reintjes marine gears supplied by Karl Senner, LLC, Kenner, LA.
The Hudson features the latest in solid-state, Simrad electronics and handsomely appointed, mahogany upper and lower pilothouses, as well as spacious accommodations for up to seven crew members.
Meanwhile, the Double Skin 601 is configured and outfitted in a nearly identical fashion to the most recent 55,000 bbl Vane Brothers barges that were delivered in 2015 by Indiana-based Jeffboat Shipyard. Like them, the Double Skin 601 is equipped with an 8,600 BTU thermal fluid heating system, vapor control system and cargo tanks coated with International Interline 994 Epoxy Novolac. However, the Double Skin 601 has a raised forecastle bow design, which provides additional reserve buoyancy.
The DS-601 and its sister, the DS-602, are both fitted with two fixed boom pedestal cranes each, Model F1-65, with a 65-foot boom length supplied by Techcrane International, Covington, LA.
Primarily tasked with towing petroleum barges engaged in the North Atlantic coastwise trade, the Hudson has joined the Elizabeth Anne among more than 20 vessels that are part of Vane’s Delta Fleet, based in Philadelphia. The DS-601 is also a new Delta Fleet member.
NEW TUG FOR SEA VISTA
In early April, BAE Systems Southeast Shipyards, Mobile, AL, launched the first of two 12,000 hp ATB tugs for Sea-Vista ATB, LLC.
One of the interesting features of the tug M/V Sea Power is that it has two independently controlled and operated hydro-dynamic Van der Velden Barke rudders. Independent Proportional Steering will allow the rudders to be actuated either independently or synchronized. The rudders were supplied by Dutch company Van der Velden Marine Systems (VDVMS) in conjunction with its U.S. representative Ships Machinery International, Inc. (SMI).
Van der Velden says that tank tests showed that rudder design was extremely effective for this type of vessel. This ATB tug will have enhanced maneuverability and excellent course keeping stability. The efficiency provided by this high technology rudder solution will result in significant savings over the life of the vessel.
The 43m x 14m ATB tug, with a draft of 6.75m, is designed by Seattle-based Guido Perla and Associates, Inc. (GPA). The tug’s power is supplied by two 4,640 kW main engines and three 250 kW main generators, with a standby emergency generator of 150 kW. The vessel uses a pin connector system between the tug and the barge and fully complies with ABS Under 90 m Rules, Maltese Cross A1 AMS ACCU Towing Vessel, SOLAS, USCG Subchapter I.
“We are pleased that our client selected this state of the art rudder system for their new vessel,” said SMI Vice President Arthur Dewey, and “we are confident that their faith in Van der Velden rudders will be rewarded over the long haul.” Van der Velden reports that the Sea Power is the only vessel of its kind in the U.S. at present time.
The tug will have exceptional maneuverability, with two independently controlled and operated hydrodynamic Van der Velden Barke rudders. Independent Proportional Steering will allow the rudders to be actuated either independently or synchronized.
Van der Velden has done a lot of work to facilitate the installation of these rudders into a hull and worked closely with Guido Perla Associates Inc. and BAE Systems to assure a smooth transition from initial design to final installation.
GPAI Chairman Guido Perla commented, “Van der Velden provided excellent technical support and on time delivery of design documents that helped us develop the engineering and design for the installation of their steering system. Their coordination with our staff was prompt and to the point. We appreciated their support.”
Van der Velden says that the key driver behind the Barke rudder is its innovative and sophisticated progressive high lift design, offering unsurpassed maneuvering and course-keeping performance, as well as smooth operational comfort. The progressively operating flap linkage system is contained in a fully enclosed, grease-lubricated Barke housing. This results in minimum wear on the linkage components and eliminates the problems caused by contact with floating objects.
Another set of Barke high-lift rudders will be installed on a second ATB tug before this summer.
BARGE FOR PROVPORT
Conrad Shipyard, Amelia, LA, recently delivered a 300-foot long x 72-foot wide rake/box barge with a deck rating of over 6,000 pounds per square foot to ProvPort, Providence, RI, according to naval architect JMS Naval Architects, Mystic, CT. The crane barge design allows for the easy loading and unloading of cargo from ships to the dock or from ship to ship.
JMS Naval Architects, Mystic, CT, engineered and designed the crane barge for the State of Rhode Island that will be used for stevedoring operations at ProvPort Inc.
ProvPort is a nonprofit public-private partnership, formed in 1994, which owns and operates the municipal port of the City of Providence, RI. ProvPort is New England’s premier deep-water multimodal facility for international trade and domestic distribution and one of the busiest ports in America’s northeast.
JMS designed the barge to carry and operate the facility’s 440-ton Liebherr LHM 550 mobile harbor cranes. The barge is ABS classed A1 with notation “Deck Barge,” uninspected and unmanned. JMS also created the technical specification documents to utilize for the solicitation of shipyard bids and provided owner’s representative services during the construction of the barge at Conrad Industries.
The contract was funded by the State of Rhode Island’s Transportation Investments Generating Economic Recovery (TIGER) II grant program award managed by the Rhode Island Commerce Corporation. The grant was created by Congress in the 2010 Transportation Appropriations Act and allowed the purchase and installation of the barge and two high performance harbor cranes. The new stevedoring equipment will modernize and enhance the port’s ability to continue its existing bulk material operations while expanding its capabilities to accommodate container operations; thus alleviating demand on the Port of Boston—the only existing container port in New England. The new crane barge will be critical for the port which has relied on 30-year-old rented crane barges that have been prone to breakdowns and have been out service for prolonged periods. The crane barges are estimated to remove on average 1,000 trucks per week off the northeast corridor highway system—one of the most congested in the country.
NEW HARBOR TUGS FOR BAYDELTA, MCALLISTER
Jensen Maritime, Seattle, is designing tractor tugs for both U.S. East Coast and West operators. One is for Vessel Chartering LLC, a wholly owned dividsion of BayDelta Navigation. The new tug is powered by a pair of 3,385-horsepower Caterpillar 3516 EPA Tier 4 engines and is the third tugboat designed by Jensen Maritime with engines meeting EPA Tier 4 requirement.
The tug was designed without ballast tanks, eliminating the need for ballast water discharge and therefore ballast water treatment systems. To maintain proper trim, the vessel will transfer fuel, as necessary.
The tug is being built by JT Marine Inc. shipyard in Vancouver, WA, for delivery in second quarter 2017.
Jointly developed by Vessel Chartering and Jensen, the 110-ft x 40 ft tug has the ship assist and escort capabilities of smaller harbor tugs, while delivering the improved towing performance and increased range of larger ocean-going tugs.
The design offers the flexibility to support ship escorts, assists and towing, with the escort capability being enhanced to provide support for assisting the large, 18,000 TEU containerships expected to make an increasing number of West Coast port calls.
With an electrically powered, double drum tow winch aft by Rapp USA and an electrically powered hawser winch forward by Markey Machinery as deck machinery, the vessel will be capable of a 93-to-95 short-ton bollard pull. Both winches’ electrical power will remove any chance of a hydraulic oil spill on deck.
The tug is designed to carry up to 123,000 gallons of fuel, 4,300 gallons of fresh water, and up to 4,500 gallons of urea, which is used in the main engine exhaust Selective Catalyst Reduction (SCR) treatment system used to meet EPA Tier 4 emissions requirements.
On the East Coast, McAllister Towing, New York, NY, has contracted with Horizon Shipbuilding, Inc., Bayou La Batre, AL, to build it two new 100 ft x 40 ft new escort tugs.
The tugs will be powered by 3516E EPA Tier 4-compliant Caterpillar engines with Schottel SRP4000FP propulsion units producing 6,770 hp and 80 metric tons bollard pull.
The tugs will be the 31st and 32nd tractors and the first Tier IV tugs in McAllister’s fleet.
They will be ABS classed Maltese Cross A-1 Towing, Escort Service, FiFi 1 and Maltese Cross AMS.
The hull has been designed by Jensen Maritime for enhanced ship docking abilities in addition to direct and indirect escorting and the tugs have been designed and simulator tested to assist new Post-Panamax and Ultra-Large Vessels.
Towing machinery will include a Markey asymmetric render-recover winch on the bow and a Markey tow winch with a spool capacity of 2,500 ft of 2¼ in wire on the stern.
MARCON BROKER FOR NEW DESIGN TUG
Purple Water Ltd. has appointed Marcon International, Inc., Coupeville, WA, as exclusive broker to handle the shipyard licensing for construction of an innovative new tug in the Americas.
Called the Giano tug, the compact double-ended tug has a high displacement tunnel hull form, two large structural keels and a straight-line controllable pitch thruster configuration designed and built solely for ship handing.
With intuitive in-line handling controls, the tug can produce 55 tonnes (70 tonnes) of bollard thrust and pull in all directions at full power with true 360 degree maneuverability, while maintaining a 0 degree list – plus a side-stepping speed of 7 knots – from full ahead to full speed sideways in 10 seconds.
The tug works equally well from the bow or stern and is fitted with 75 tonne escort winches fore and aft.
The design is claimed to has the highest stability numbers of any escort tug afloat, not only in its own 24 m compact class, but also compared with the 32 m escort terminal class.
Two separate engine rooms, a separate generator room and a double hull with integral “W” heavy duty fendering and patented underwater fenders provide a high level of safety, and allow the tug the unique capacity to side thrust and push at full power without listing, while assisting vessels in confined spaces
The Gianotug design is patented over 40 countries.
After four years of research and development, the first tug of this class, is now available in Italy for shipowners and shipyards interested in licensing and building the design to inspect and experience a “hands-on” demonstration of the tug’s capabilities.
Built by Chinese shipbuilder Guangdong Bonny Fair Heavy Industry, the 25.75 m x 13.02 m x 5.20 m depth / 5.30 m Giano is powered by twin 1,678 kW CAT 3512C-HD diesels developing a total power of 4,562 HP at 1,800 RPM.
A Schottel SRP-3000 azimuthing drive with a controllable pitch prop is mounted in a straight line at each end, with the tunnel hull specifically designed to eliminate propeller interference.
Topside access and ultra-short shaft lines allow for main engine removal in a few hours.
The U.K. flagged Giano is classed LR +100A1, Escort Tug, FiFi-1 (2,400 cu.m/h) with water spray, Unrestricted – MCA WB Area 1 (up to 150 miles from safe haven). While this first vessel has a 55 tonnes bollard pull, the unified design allows for both 55 tonnes and 70 tonnes bollard pull versions to be built.
MAY 3, 2016 — The members of the American Waterways Operators (AWO), the national trade association representing the tugboat, towboat and barge industry, have elected a new slate of leaders. James F.
APRIL 28, 2016—Gunderson Marine, Portland, OR, has secured an order to build two 82,000 bbl, 430 foot-long Articulated oceangoing tank barges for Harley Marine Services, Inc., Seattle, WA. Gunderson last built a
Nichols Brothers Boat Builders recently completed sea trials on the second of 10,000 hp oceangoing tugs for Kirby Offshore Marine, the coastal tug and barge arm of Kirby Corporation, Houston, TX. The 136 ft x 44 ft tug, Tina Pyne, will be connected to the 185,000 bbl ocean tank barge 185-02 built by Gunderson Marine, Portland, OR.
Kirby’s newbuild plan also includes two 155,000 bbl/6,000 hp Articulated Tug Barge (ATB) units under construction at Fincantieri Bay Shipbuilding in Sturgeon Bay, WI, as well as two 120 ft x 35 ft, 4,894 hp tugs being built by Nichols Brothers Boat Builders. Each tug will be powered by two Caterpillar 3516C engines, each rated at 2,447 hp at 1,600 rev/min, with Reintjes reduction gears turning two Nautican fixed-pitched propellers with fixed nozzles. The Reintjes gears were supplied by Karl Senner, LLC, Kenner, LA. The tugs will also have two C7.1 Caterpillar generators for electrical service. Selected deck machinery includes one TESD-34 Markey tow winch, one CEW-60 Markey electric capstan, and one Smith Berger Tow Pin.
Kirby Offshore Marine is the largest U.S. operator of coastal tank barges that provide regional distribution of refined petroleum products, black oil and crude oil. Kirby grew its coastal marine transportation business through the acquisition of K-Sea Transportation Partners L.P. back in 2011 in a transaction valued at about $604 million. At that time, Kirby acquired 58 tank barges (only 54 were double hull) with a capacity of 3.8 million barrels and 63 tugs.
Already the operator of the largest inland tank barges and towboats, Kirby Corporation will grow further with the purchase of Seacor Holdings Inc.’s inland tank barge fleet for about $88 million in cash.
Under the terms of the deal struck last month, Kirby will acquire 27 inland 30,000 bbl tank barges and 13 inland towboats, plus one 30,000 bbl tank barge and one towboat currently under construction. As part of the agreement, Kirby will transfer to Seacor the ownership of one Florida-based ship-docking tugboat.
Kirby Inland Marine currently has 898 active inland tank barges and 243 towboats, with a total carrying capacity of 17.9 million barrels. The primary cargoes transported by this fleet are chemicals, petrochemical feedstocks, gasoline additives, refined petroleum products, liquid fertilizer, black oil and pressurized products.
Kirby President and CEO David Grzebinski, says “Operating primarily in the refined products trade, these assets will be complementary to our existing fleet and will allow us to continue to enhance customer service.”
TRIPLE-SCREW BOATS FOR MID-RIVER
Over the years, Rodriguez Shipbuilding, Inc.’s triple-screw towboats have won a following operating in the shallow waters where the Mississippi River meets the Gulf of Mexico. These Lugger-type vessels are designed with a distinctive aft-cabin.
Mid-River Terminals of Osceola, AR, recently took delivery of a new design towboat from Rodriguez Shipbuilding, Coden, AL. With a conventional forward-house pusher configuration, the new 70 ft x 30 ft MV/ Dianna Lynn uses the same propulsion as the Lugger tugs. This is composed of three in-line six-cylinder Cummins QSK 19 engines, each delivering 660 hp. Each engine turns a 66-inch stainless steel propeller through ZF gears with 6:1 reduction ratio. The combination gives the 1,980 hp towboat an eight-foot operating draft.
Fitted with large windows, the wheelhouse has a full 360-degree view and is set atop two accommodation decks and a half deck that also serves for bridge electronics support. This gives the towboat a 31-foot high eye-level, with full tanks, for working high barges.
Steering and flanking rudders are controlled by wheelhouse levers with mechanical shafts through the houses and connected to the hydraulic actuator valves in the upper engine room.
A set of push knees and deck winches with cheek blocks facilitates barge work. A pair of 55 kW gensets meets the boat’s electrical requirements.
Zero discharge tanks, built integral to the hull, provide storage for treated sewage and all drains. A separate tank handles waste oil.
The M/V Dianna Lynn is the fourth boat in the Mid-River Terminal fleet, all of which are Cummins powered. Owner Rick Ellis said, “We wanted the three engines for redundancy so that even if we loose an engine we still have over 1,200 horsepower.”
The new boat will be primarily involved in fleeting and harbor work, “Rodriguez did a great job and it is a great handling boat,” Ellis added.
BOUCHARD, MORAN EXPANDING FLEETS
As we highlighted last month, Bouchard Transportation’s multi-million-dollar newbuild program is winding down. The Melville, NY, owner is completing the construction of two new 6,000 hp, 310 ft x 38 ft Intercon tugs at VT Halter Marine, Pascagoula, MS. The tugs Morton S. Bouchard Jr. and Fredrick E. Bouchard will be connected to the B. No. 210 and B. No. 220. The two tank barges were the first double hull tank barges built by Bouchard,. Both were built as wire barges, but following their conversion and stretch at Bollinger Shipyards, Inc., both will be Intercon, flat deck double hulls capable of carrying 110,000 bbl of oil.
Moran Towing, New Canaan, CT, expects to take delivery shortly of a 5,300 hp/110,000 bbl ATB unit from Fincantieri Bay Shipbuilding. The Sturgeon Bay, WI, has another 8,000hp/155,000 bbl ATB unit under construction for Plains All American Pipeline, with an option for a second unit, and signed a hotly contested order for another 8,000 hp/185,000 for another earlier last month. That contract includes an option for another.
The new barge will have a capacity of 185,000-barrels with dimensions of 578 feet by 78 feet. The tug will be an 8.000-HP unit equipped with Tier 4 engines—believed to be GE Marine—to meet the latest EPA emission standards.
When complete, the ATB will operate on the U.S. East Coast and Gulf of Mexico.
“We are pleased to have this opportunity,” said Francesco Valente, FMG President and CEO. “This new contract marks an additional expansion of our product portfolio, confirms our ability to win business with new customers in a very competitive market and further consolidates our presence and reach in the U.S. market.”
“This award increases our pipeline of new construction to 10 vessels and provides additional stability to our business,” said FBS Vice-President and General Manager, Todd Thayse. “We are grateful for the confidence that our customers continue to place in our reputation for quality and the strong shipbuilding skills of our workforce.”
Conrad Shipyards, Morgan City, LA, meanwhile, is building the 80,000 bbl ATB unit for John W. Stone, as well as two ATB tugs for Harley Marine Services, Seattle, WA. Conrad Orange Shipyard in Orange, TX, recently delivered the 35,000 bbl Double Skin 315 to Vane Brothers Company. That barge was towed to New York by the Elizabeth Anne, the first in a series of eight 4,200 hp tugs being built by St. Johns Ship Building, Palatka, FL.
Designed by Frank Basile, P.E. of Entech Designs, LLC, the Elizabeth Anne Class tugboat is a close cousin to Vane’s Basile-designed Patapsco Class tugboats, 15 of which were produced between 2004 and 2009. Measuring 100 feet long and 34 feet wide, with a hull depth of 15 feet, the model-bow Elizabeth Anne utilizes two Caterpillar 3516 Tier 3 engines, each generating 2,100 hhp at 1,600 rev/min. Two John Deere PowerTech 4045, 99 kW generators deliver service power to the boat, while a third John Deere 4045 teamed with an Allison transmission drives the chain-driven INTERCON DD200 towing winch.
ROBERT ALLAN’S LATEST
Over the years, world renowned naval architectural and marine engineering firm Robert Allan Ltd. Has successfully teamed with shipyards around the world to bring new innovative tug designs to the market. Its latest is the VectRA 3000 Class Tug, a high performance VSP Tractor tug designed by Robert Allan Ltd in close collaboration with Turkish ship builder Sanmar and Voith Turbo Propulsion. The tug is designed for maximum efficiency in the performance of towing, harbor ship-handling and escorting of large ships. Performance has been verified with extensive model tests at the commencement of the design cycle. The unique propulsion arrangement features high-speed diesel engines connected to the Voith units via reduction gearboxes with integral clutches. With a bollard pull of 70 tonnes, the VectRA 3000 form can generate escort steering forces in excess of 100 tonnes. Additionally, the design has fire-fighting and oil recovery capabilities and is fully MLC compliant.
The VectRA 3000 has been designed exclusively for Sanmar to offer as one of its highly successful stable of progressive tugboats for the world market.
The first vessel in the series, the M/T Ares, built for Italian tugowner Tripmare SpA, was successfully launched at Sanmar’s new Altinova advanced shipbuilding facility this past February.
The tug has an overall length of 30.25 m, beam of 13m, depth of 5.1m, and design draft of 6.1m.
The vessels are built and classed to the following ABS notation: ✠ A1 Towing Vessel, Escort Vessel, ✠ AMS, Unrestricted Service, UWILD, HAB (WB), ABCU Fire-Fighting Vessel Class 1 Oil Spill Recovery – Capability Class 2 (>60° C) (OSR – C2).
Rather uniquely for a VSP installation, the propulsion drivetrain comprises two Cat 3516C high-speed diesel engines, each rated 2,525 kW at 1,800 rev/min, and driving Voith 32R5EC/265-2 cycloidal propellers. The engines are connected to the Voith drives through a pair of Reintjes WAF 863 gearboxes and Vulkan composite shafts, rather than using the more traditional turbo coupling. This combination is smaller, lighter and less costly than the traditional medium speed drive system. The electrical plant consists of two identical diesel gensets, each with a rated output of 86 ekW.
Crew accommodations are all located on the main deck level for optimal crew comfort. There are 4 single crew cabins plus 1 double crew cabin, each with an en-suite bathroom. A comfortable lounge/mess area and galley facilities are also in the deckhouse, with galley stores and laundry room located below the main deck forward.
All towing, ship handling, and escort work is performed using a double drum escort winch and escort rated staple fitted on the aft deck. One drum can store 710 meters of steel wire line, while the other stores 150 meters of synthetic towline. For increased operational flexibility radial type tow hooks are installed on the main deck forward and aft.
As in a traditional tractor configuration, the stern is the working end of the tug, and as such features heavy-duty cylindrical fendering with a course of ‘W’ fenders below. Hollow ‘D’ fenders protect the sheer lines and tie neatly into the ‘W’ fenders at the bow.
The wheelhouse is designed for excellent 360-degree visibility and includes overhead windows. The split type console is biased aft to ensure unobstructed visibility of the working deck (including the winch, staple, bulwarks and fenders) during operations.
CARGILL’s PUSHBOATS FOR THE AMAZON
In Brazil, the construction of a fleet of Robert Allan Ltd.-designed pushboats and barges for Cargill Transportation is nearing completion. To be used for transporting grain products on the Amazon River system, the fleet includes two shallow-draft RApide 2800-Z2 class pushboats built at INACE in Fortaleza, Brazil and 20 hopper barges built at Rio Maguari in Belem, Brazil.
Each of the two new RApide 2800-Z2 Class pushboats are 28m x 10.5m, with a minimum operating draft of 2.2m and normal operating draft of 2.5m. The two sister vessels, the Cargill Cachara and Cargill Tucunare, are designed to push barge convoys on the Amazon River system.
During the early phases of design, extensive CFD simulations were undertaken to optimize the pushboat’s hull shape to minimize total convoy resistance.
This work was completed in conjunction with extensive logistics modeling of the transportation system to optimize the selection of vessels for the desired route and to analyze operational drafts and cargo throughput at various river levels.
The pushboats were designed to ABS and Brazilian NORMAM-02 requirements and are outfitted to the highest standards.
The wheelhouse is designed for maximum all-round visibility with a split forward control station providing maximum visibility to the foredeck working area of the tug as well as to the convoy of barges ahead. Accommodation for up to 13 people is provided onboard and a large galley and mess is provided on the main deck.
The deckhouse extends aft over the main propulsion components, which comprise a pair of Caterpillar 3512B diesel engines, driving Schottel SRP 550 Z-drive units. The drives are fitted in tunnels designed to optimize flow while reducing draft. Two identical Caterpillar diesel gensets are provided in the vessel’s auxiliary machinery space located below the main deck.
The corresponding 61m x 15m box and rake barges were designed by Robert Allan Ltd. to ABS River Rule requirements. Additional extensive FEA analysis of the structure was performed in order to optimize the design for minimum steel weight while ensuring long service life during river operations. Sliding aluminum hatch covers have been supplied to ensure the cargo stays dry at all times.
“In the more than seven years that Shell has held leases in the Chukchi, it has only recently been allowed to complete a single well. What we have here is a case in which a company’s commercial efforts could not overcome a burdensome and often contradictory regulatory environment,” says Murkowski. “The Interior Department has made no effort to extend lease terms, as recommended by the National Petroleum Council. Instead, Interior placed significant limits on this season’s activities, which resulted in a drilling rig sitting idle, and is widely expected to issue additional regulations in the coming weeks that will make it even harder to drill. Add this all up, and it is clear that the federal regulatory environment—uncertain, ever-changing, and continuing to deteriorate—was a significant factor in Shell’s decision.”
Murkowski made the point that just because the U.S. has created a difficult environment for offshore drilling in the Arctic, it doesn’t mean other countries have. “Development in the Arctic is going to happen—if not here, then in Russia and Canada, and by non-Arctic nations,” says Murkowski. “I personally believe that America should lead the way. The Arctic is crucial to our entire nation’s future, and we can no longer rely solely on private companies to bring investments in science and infrastructure to the region. As the Arctic continues to open, we urgently need to accelerate our national security investments in icebreakers, ports, and other necessities.”
Some Congressional opponents of Arctic drilling applauded Shell’s move. Senator Jeff Merkley (D-OR) called offshore Arctic drilling “unacceptable” and irresponsible. Rep. Jared Huffman (D-CA) went so far as to introduce the Stop Arctic Ocean Drilling Act of 2015, which would prohibit new or renewed oil and gas leasing in the Arctic Ocean Planning Areas of the Outer Continental Shelf.
But this should probably be viewed more like a pause as opposed to a full stop. A more favorable regulatory environment for Arctic offshore drilling could develop if a Republican is in the White House in 2017 backed by a Republican-controlled Congress. Additionally, cheap oil and gas should also increase consumption and eventually lead to higher prices and make Arctic drilling more economically attractive.
Shipyards, naval architects team on projects
Portland, OR, headquartered Vigor Industrial, the largest shipyard group in the Pacific Northwest with 12 facilities in Alaska, Washington, and Oregon, had bolstered its capabilities in anticipation of an increased workload. It added an 80,000-ton lifting capacity dry dock to enhance its ship repair and maintenance capabilities and merged with Kvichak Marine Industries, Seattle, WA, to add capabilities in new aluminum vessel construction. Vigor had supported Shell’s earlier efforts in Alaska, including the activation of the drilling barge Kulluk, and more recently repaired the damaged icebreaker Fennica.
Vigor is part of a vibrant Washington State maritime cluster that includes logistics and shipping, fishing and seafood, and shipbuilding and repair. According to a recent economic impact study, generated 148,000 direct and indirect jobs and directly creates $15.2 billion in gross business income and has a total impact of $30 billion on the state’s economy.
Back in March, Vigor “christened” its dry dock Vigourous with work on the cruise ship Norwegian Star and followed that up with repairs to the USNS John Glenn and USNS Montford Point. Now Vigor will turn its attention to completing the third Olympic Class 144-car ferry for Washington State Ferries and look forward to building the fourth in the series, which recently received $122 million in funding by the state legislature. There’s plenty of more coverage on the ferry market in this issue, including Seattle-based Elliott Bay Design Group’s support of ferry projects for the New York City Department of Transportation and Texas Department of Transportation.
Special launch system
Designed by Seattle-based naval architectural firm Guido Perla Associates, Inc., the144-car ferry is a joint construction effort between Vigor and neighboring Nichols Brothers Boat Builders, Whidbey Island, WA. Nichols Brothers Boat Builders has been contracted to build the superstructure for the first three Olympic Class ferries. Nichols Brothers Boat Builders has used a new track and dolly system developed by Engineered Heavy Service (EHS), Everett, WA, for transferring the ferry superstructures it on to a barge for transport to assembly with the hull at Vigor Fab in Seattle.
That same transfer system is pictured on this month’s cover, to launch the ATB tug Nancy Peterkin, the first of two 136 ft x 44 ft x 19 ft sister ATB tugs being built for Kirby Offshore Marine.
This past May, Gunderson Marine, Portland, OR, had launched the Kirby 185-01, a oil & chemical tank barge.
The Nancy Peterkin’s sister ATB tug, the Tina Pyne, is set for launch this December.
The EHS launch system moved the ATB from the shipyard to the launch ramp. General Construction provided two floating cranes to assist in the final lifting of the vessel, shuttling it to deeper water.
The vessel was towed to Everett, for lightship, stability testing and fuel transfer. Following this the tug will be towed to Nichols Brothers outfitting pier in Langley, WA, located across the Puget Sound from Everett, WA, for final outfitting, dock and sea trials before its final delivery.
Used for vessels greater than 1,000 tons, the new launch system significantly increases the displacement and draft of the vessels that Nichols Brothers can haul and launch in the future. Currently the shipbuilder is engineering to install ridged buoyancy tanks to the side of the launch frame, eliminating the need for the floating cranes in the future.
Nichols Brothers followed up the launch with the signing of a construction security agreement with Kirby Offshore Marine to build two new 120 ft x 35 ft x 19 ft-3 in tugs. Each tug will be powered by two Caterpillar 3516C, 2,447 bhp at 1,600 rev/min main engines with Reintjes reduction gears turning two NautiCAN fixed pitched propellers with fixed nozzles. Karl Senner, Inc., Kenner, LA, supplied the reduction gears for the vessel. These vessels will also have two C7.1 Caterpillar generators for electrical service. Selected deck machinery includes one TESD-34 Markey tow winch, one CEW-60 Markey electric capstan, and one Smith Berger Tow Pin.
Keels will be laid for both vessels this fall with delivery of the first vessel scheduled for May 2017 and the second vessel is scheduled for delivery in November 2017.
Jensen Maritime Consultants, Seattle, the naval architectural and engineering arm of Crowley Maritime, will provide the ABS Class and functional design for the tugboats. These tugboats will carry an ABS loadline, compliant with USCG, as required at delivery.
Nichols Brothers is currently working on the second ATB Tug for Kirby Offshore Marine.
Nichols Brothers spokesperson Lacey Greene says the shipyard has just begun construction of the American Samoa 140 ft Multi-Purpose Cargo/Passenger Ferry, and next year will begin construction on the superstructure and final assembly of the WETA 400-passenger high speed catamarans.
“The vessel construction boom in the Pacific Northwest has impacted the economy in so many different ways,” says Greene. “Specific to our location our community is flourishing. Nichols Brothers is the largest private employer on Whidbey Island in Washington State and employs 300 men and women. We foresee the economic boom expanding even further; the tug market is strong in all aspects, from ATB tugs, tractor Tugs, to line tugs. We also see the passenger vessel industry sector thriving, and we predict additional passenger only high-speed ferries coming down the pipeline as well as leisure vessels.”
Jensen Maritime is also providing construction management services for the Crowley product tankers under construction at Aker Philadelphia Shipyard. It’s also been busy working on developing LNG bunker barge concepts and recently received approval from ABS for a 452 ft-long ATB version.
Engineering consultant Art Anderson Associates, Bremerton, WA, has been increasing its staff and supporting the development of passenger-only ferry service in Puget Sound. Art Anderson’s Patrick R. Vasicek, PE, LEED AP, will be on hand at the Marine Log FERRIES 2015 Conference & Expo in Seattle to discuss, “An Exportable Life Cycle Assessment Tool for Determining Sustainable Visibility of Passenger-Only Ferry Routes and Systems.”
Ballast water treatment solution
Seattle-based naval architectural and engineering consultancy Glosten reports that Marine Systems Inc. (MSI) has delivered a pair of Ballast Treatment System Deck Modules, designed for tank barge and ship operations.
MSI turned to Glosten to develop the design in response to requests from vessel operators and the first of a kind modular ballast water treatment units combine expertise from Glosten, MSI and Alfa Laval, which provided PureBallast 3.1 treatment systems, Filtrex high efficiency filters, and expertise from hundreds of ballast water management system installations.
The resulting modules, built at the Foss Seattle Shipyard, complete with lighting, ventilation, and integrated controls, were shipped ready for “plug-and-play.”
Each Ballast Module packs a treatment capacity of 1,000 m3/hr within a 20-foot shipping container footprint and is ABS and U.S. Coast Guard approved for hazardous area installations.
Using the module reduces the technical demands on busy shipyards. Rather than juggling independent components and vendors, shipyards can instead focus on fabricating a few well-defined interfaces and foundation system. Each purchased module comes pre-approved by USCG and ABS, is fully tested prior to shipment, and includes integration support from MSI and Glosten engineers.
“The demands of the vessel operator drove this design,” says Kevin Reynolds, Principal at Glosten. “Doing this as a manufactured product ensures that we get it right, every time.”