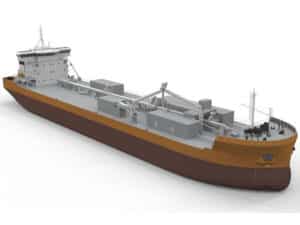
Digital management of parts supply makes MRO operations more efficient
Written by Marine Log Staff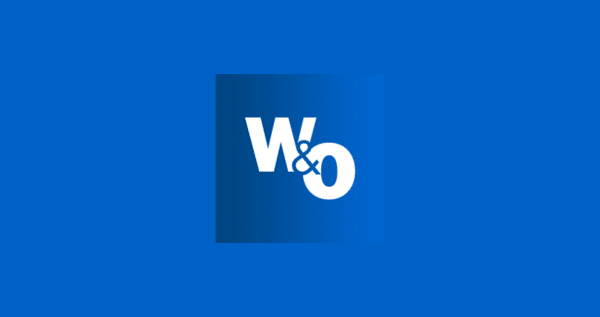
SPONSORED CONTENT: The inland waterways sector holds a significant importance in the transportation of key commodities within the United States, being responsible for roughly 15% of the nation’s freight movement. It serves as a vital support system for industries dealing with energy, chemicals, and grains, offering a swift, efficient, and environmentally friendly means of transportation.
Tugs and barges present one of the most economically viable freight solutions across various sectors. It’s imperative for operators to manage costs effectively to sustain their competitiveness in this market. One of the hindrances to efficiency is the cost of maintaining, repairing, and overhauling of both infrastructure and vessels.
With the demand for waterborne freight capacity remaining strong, operators are incentivized to maintain high utilization rates for their fleet. This necessitates conducting maintenance, repair, and overhaul dry-docking operations with utmost efficiency.
Operators and owners strive to minimize operational losses by speeding the process of dry-dock process. However, procuring replacement parts can pose challenges, especially when there is limited knowledge about the installed parts and valves. The absence of records regarding installed valves complicates the accurate specification of replacement parts.
Effective planning of Maintenance, Repair, and Overhaul (MRO) projects can be facilitated by collaborating closely with knowledgeable suppliers. An expert supplier combines technical expertise with a comprehensive understanding of the supply chain, ensuring timely delivery of the right parts at competitive prices.
Surveying vessels, to identify what parts need replacing, is a necessary step in the maintenance program. At W&O, our team of technical experts perform these assessments before vessels are taken out of service, alleviating time constraints for owners and contractors. Rushed procurement of valves during maintenance projects may lead to premature failures, emphasizing the importance of careful selection based on suitability.
Prior to dry-dock inspections, technical teams meticulously record essential details of valves, including size, materials, location, and installation date. Subsequently, a radio frequency identification (RFID) tag is affixed to each valve, linking it to pertinent information stored in an online database. This enables technicians to effortlessly access valve specifications using mobile devices, facilitating accurate part procurement in the future.
At W&O, we specialize in supplying parts to the maritime industry. Our extensive distribution network ensures that we have the required parts in stock, ready for prompt shipment. Backed by a dedicated team of experts, we offer technical support nationwide, aiding in minimizing delays and cost overruns in
maintenance operations and swiftly returning vessels to profitable operations. For more information on products or services from W&O, please visit: wosupply.com or call +1 800.962.9696.