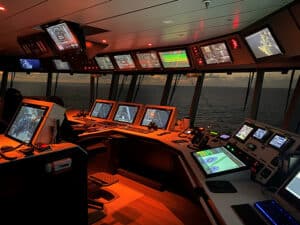
Op-Ed: Building today, but designing for tomorrow
Written by Heather Ervin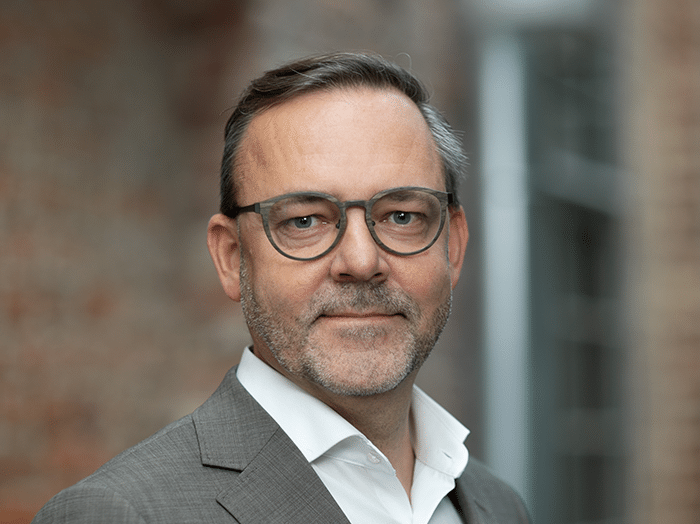
Rami Hirsimaki
By Rami Hirsimaki, Senior Vice President, Marine & Offshore Energy at Elomatic
When it comes to ship design, looking beyond the horizon is more important than ever. Decarbonization is no longer an issue just for newbuilds, but an urgent one for the current fleet—all of which requires owners to navigate a range of design choices and uncertainty.
Alongside future fuel choices, decisions on efficiency technologies and how vessels might perform under new regulations and incentives, the issues that are keeping ship owners awake at night include several they haven’t even fully identified yet, not to mention that above all those new challenges, the ship still needs to be optimized to fulfill its primary mission whether it is a cruise ship, a ferry or an icebreaker.
Only a superior ship design secures the required revenue potential in order to increase competitiveness and accommodate the costs of the energy transition.
The complex challenges of tomorrow are only just at the conception stage for most. That is why it is crucial to be designing for the issues of tomorrow at every stage of the ship design process.
Decisions made at the design stage today will impact an owner for decades to come—and could well determine whether or not an owner will still be operating in the next 10 years and beyond. Exposure to EU ETS or other carbon pricing, and CII ratings, will be essential commercial considerations for any ship owner or operator. It is therefore essential that at every stage, a design partner can thoroughly model and evaluate all options and simulate how they will perform. This requires significant, dedicated resources—decisions today may have major impacts on operations tomorrow.
Owners need support in developing innovative and sustainable—green, efficient & smart —newbuilding ship concepts. They also need a partner to scrutinize existing fleets’ ability to comply with tightening upcoming rules. The design challenges of the future require a level of technical resource and expertise that can iterate on and evaluate a range of concepts and scenarios.
This might, for example, mean adapting designs to specific trading patterns—simulating and forecasting how different concepts will perform over time, rigorously testing and prove designs at an early stage. All of this saves time, money and work later down the line—changes to a design later in the process are far most costly than fully exploring options upfront.
An example of ship design leading the way to zero emissions, can be seen with our work with the Nippon Yusen Kabushiki Kaisha (NYK Line). NYK tasked Elomatic with designing two ship concepts closely resembling their current state-of-the-art vessels but operating on an alternative fuel source. This concept was aimed at identifying the most viable green fuel as the industry makes concerted efforts to move away from hydrocarbon-based fuels. In the end, NYK and Elomatic developed a concept that offers scalability for future deployments.
The concept serves as a next-bridge solution to enable NYK to convert their existing LNG-powered vessels to ammonia at a minimum cost once green ammonia becomes commercially viable and ship engines are suitably engineered to utilize it.
Back to Basics?
At the same time, there are surprising solutions across the board that almost seem to be taking us back to basics. Particularly when it comes to retrofitting existing vessels, sometimes simplicity is key. Take Elomatic’s Elogrid solution for example; the unassuming special tunnel thruster grid significantly reduces the additional resistance and fuel consumption of ships, and demonstrates how even a small piece of equipment, developed using advanced modelling can make a notable, cost-efficient difference on fuel consumption and CII.
At the same time, Elogrid increases side thrust by up to 15% and further saves on tug assistance costs or the reduction of thruster size. In addition to increased safety of maneuvering, Elogrid also removes cavitation in tunnel thrusters and thereby reduces both noise and vibration and increase the comfortability in maneuvering operations.
Restless Innovation
Innovations such as these demonstrate the benefits of committing greater resources than ever before to numerical simulations. In addition to deploying our engineering expertise, we rely on our super-large computer cluster to perform complex calculations that allow us to accurately test and validate concepts. By performing full-scale digital CFD calculations (computational fluid dynamics), we can achieve a paramount level of accuracy, richer in detail, quick and reliable – enabling iterative and parametric investigations.
Whether we are designing the ships of tomorrow, or improving the ships of today, there is no silver bullet, but as long as we keep our eyes on the horizon, we’ll find a smart solution.